- Use of oxide containing 20% iron to obtain discharge voltage comparable to that of conventional cathode materials -
Mitsuharu Tabuchi (Senior Research Scientist) and Tomonari Takeuchi (Senior Research Scientist), the Advanced Battery Research Group (Leader: Kuniaki Tatsumi), the Research Institute for Ubiquitous Energy Devices (Director: Tetsuhiko Kobayashi) of the National Institute of Advanced Industrial Science and Technology (AIST) (President: Tamotsu Nomakuchi), Junji Akimoto (Leader), the Crystal Materials Engineering Group, the Advanced Manufacturing Research Institute (Director: Nobumitsu Murayama) of AIST, and Junichi Imaizumi (Team Leader), the Analysis Team, Research and Development Department of Tanaka Chemical Corporation (President: Tamotsu Tanaka) have jointly developed two types of cobalt-free oxides, namely, (Li1+x(Fe0.2Ni0.4Mn0.4)1-xO2 and Li1+x(Fe0.2Ni0.2Mn0.6)1-xO2that can be used as cathode materials for lithium ion secondary batteries. Approximately 20% of the total amount of transition metals in the oxide materials is iron, which is abundant and inexpensive.
These materials do not contain cobalt (a rare metal). Despite their high iron content, their discharge voltages of 3.5–3.7 V are higher than the discharge voltage (3.0 V) of Li1+x(Fe0.5Mn0.5)1-xO2, which was previously developed by AIST, and are closer to the discharge voltage (4 V) of the conventional cathode materials such as LiNi1/3Mn1/3Co1/3O2 and LiNi1/2Mn1/2O2. The use of iron is advantageous since it is abundant and reduces costs; however, it used be difficult to develop oxides containing iron as cathode materials. The successful use of iron will help conserve resources and reduce the costs of lithium ion secondary batteries for electric vehicles including hybrid cars.
The details of this study will be published in the 50th Battery Symposium in Japan held at Kyoto International Conference Center, from November 30 to December 2, 2009. The study was conducted as part of a sponsored research project, "Development of battery systems for next-generation vehicles (Li-EAD project)– R & D of novel and high-capacity positive electrode material consists of low-cost constituent oxides (from FY2007 to FY2009)," funded by New Energy and Industrial Technology Development Organization (NEDO).
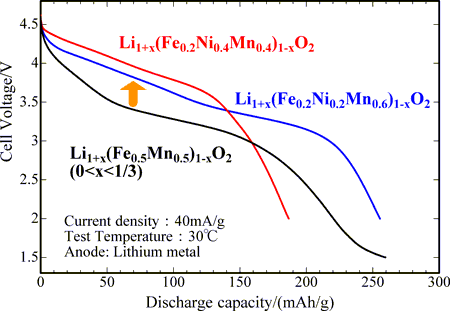
|
Fig. 1 Initial discharge curves of the cathode materials after charging to 5 V: newly developed (red and blue) and preciously developed (black) |
With growing awareness regarding environmental issues and energy conservation, electrical vehicles that use batteries and hybrid cars are attracting attention. Although nickel-metal-hydride batteries are the main power sources for electrical vehicles, the use of lithium ion secondary batteries is increasing because of their competitiveness with respect to their energy density, i.e. the electrical energy charged and discharged per unit weight or volume. Japanese battery manufacturers have developed and supplied lithium ion secondary batteries for cellular phones and notebook computers, and they maintain a position of technical superiority compared to battery manufacturers in the world.
In order to realize wider use of lithium ion secondary batteries in electrical vehicles, we need improvement in their performance and cost reduction as well as ensuring safety. To reduce the cost, the constituent materials used as cathodes, anodes and electrolytes must be replaced with less expensive materials. Oxides of lithium and transition metals such as cobalt, which is a rare metal, are cathode materials and are very expensive materials in batteries. Hence, there is a great demand for developing cathode materials that contain inexpensive, abundantly available metals such as iron with minimum influence on performance; the costs of oxides of iron, manganese, and titanium are approximately 1/10, 1/8, and 1/4, respectively, of the cost of the oxide of cobalt. However, we have not yet found the ideal alternative materials for inexpensive, high-performance cathodes. There is a great demand for the development of such materials.
AIST has been studying lithium manganese oxides that contain iron and titanium. These elements are characterized by their abundance, low cost, and low toxicity. The oxides can be used as cathode materials for lithium ion secondary batteries (press releases of October 21, 2004, November 22, 2004, and November 6, 2006). The charging and discharging mechanisms of lithium manganese oxides containing iron were studied by using an analytical electron microscope, etc. The role of iron and the relation between the chemical composition and fabrication process of materials and their charge and discharge capacities was clarified (press release of August 18, 2008).
Iron and titanium have not been used in cathode because their charge and discharge characteristics depend greatly on the fabrication process, and conventional fabrication processes including solid-state reactions did not yield good results. It was found that particle size is a key factor: smaller the particle size, larger is the discharge capacity. In 2007, AIST and Tanaka Chemical Corporation, which has accumulated sufficient technical knowledge of the co-precipitation process, started a collaborative research in solid solutions of iron or titanium and lithium manganese oxide for cathodes, with an emphasis on synthetic processes such as co-precipitation.
The complex oxides for cathode previously developed in AIST contained iron, manganese, and titanium; these oxides may be advantageous with respect to material costs and abundance of resources. However, a disadvantage is that the average discharge voltage is low (3.0 V) and is much smaller than that (4.0 V) of the existing materials such as LiNi1/3Mn1/3Co1/3O2 and LiNi1/2Mn1/2O2. In this research, in order to improve the average discharge voltage, we added nickel, which is a popular material for the battery industry, to iron-containing lithium manganate (Li2MnO3). Nickel is less expensive than cobalt; the cost of nickel oxide is 1/2–1/3 that of cobalt oxide. Two cathode materials, A and B, were designed. The nickel content of these materials was less than 40%, and the iron content is more than 20% of the total amount of transition metals:
Material A: Li1+x(Fe0.2Ni0.2Mn0.6)1-xO2 (0 < x < 1/3)
Material B: Li1+x(Fe0.2Ni0.4Mn0.4)1-xO2 (0 < x < 1/3)
In material A, for the electrochemical activation, a 1:1 mixture of iron and nickel, instead of only iron, is added to Li2MnO3. In material B, a 4 V-class LiNi1/2Mn1/2O2 cathode is used instead of 3 V-class Li2MnO3 one as the matrix; iron is added to this matrix.
Cathode materials are manufactured by a co-precipitation–hydrothermal reaction–calcination method developed at AIST.
1. Co-precipitation process: The aqueous solution of iron nitrate, nickel nitrate, and manganese chloride is cooled and added dropwise into the aqueous solution of lithium hydroxide. Ethanol was added to the lithium hydroxide solution as antifreeze liquid. Iron, nickel, and manganese containing co-precipitate was prepared through the wet air oxidation of the precipitate at room temperature.
2. Hydrothermal reaction process: The co-precipitate is put into distilled water containing lithium hydroxide, potassium hydroxide, and potassium chlorate, and is hydrothermally-processed for 48 hours in an autoclave (temperature: 220 °C, pressure: approximately 2 MPa).
3. Calcination process: The hydrothermally processed co-precipitate is dispersed in the solution of lithium hydroxide; it is crushed after drying. The material is calcined for 20 hours in air or in a nitrogen flow in an electric furnace at 700 or 750 °C. The product is crushed, washed with distilled water, filtrated, and dried to prepare a cathode material.
Charge and discharge characteristics can degrade if grains containing iron grow during high-temperature calcination process. The new technique enables effective utilization of iron because it requires a low calcination temperature, and ensures a uniform distribution of the transition metal ions. Note that in the co-precipitation process, wet air oxidation after co-precipitation is the key process in the stable production of high-quality samples. For this purpose, it is important to ensure the uniformity of oxidation over a sample. The homogeneity of a sample is further improved by lengthening the hydrothermal reaction time. By adopting the new method both materials A and B obtain layered rock salt-type Li2MnO3 structure, which is very similar to that of the existing cathode materials of voltage 4 V, LiNi1/3Mn1/3Co1/3O2 and LiNi1/2Mn1/2O2.
The discharge curve after charging to 5 V is shown in Fig. 1 for material A (calcined in a nitrogen flow at 750 °C). Initially, its charge capacity, discharge capacity, and average discharge voltage are 349 mAh/g, 255 mAh/g, and 3.46 V, respectively. As listed in Table 1, its charge and discharge capacities are close to the capacity of an existing cathode material (LiNi1/3Mn1/3Co1/3O2), 220 mAh/g (a literature value). The discharge voltage of material A is higher than that of a previously developed material (Li1+x(Fe0.5Mn0.5)1-xO2) by 0.5 V. The discharge curve after charging to 5 V charging for material B (calcined in a nitrogen flow at 750 °C) is also shown in Fig. 1. Initially, its charge capacity, discharge capacity, and average discharge voltage are 261 mAh/g, 187 mAh/g, and 3.67 V, respectively. As listed in Table 1, the charging and discharging capacities are close to the capacity of an existing cathode (LiNi1/2Mn1/2O2), 200 mAh/g (a literature value). The discharge voltage of material B is greater than that of previously developed materials by 0.7 V. Although the average discharge voltages of cathode materials containing iron are relatively low, their charge and discharge characteristics are very similar to those of the existing cathode materials. The charge and discharge curves show similar features after 20 cycles, and 76% (material A) and 65% (material B) of the initial discharging capacity is retained even after 20 cycles. This performance assures that the new materials can be applied in cathodes in lithium secondary batteries for electric vehicles.
Table 1 Charge and discharge characteristics of materials A and B, existing materials and previously developed material |
|
Figure 2 shows the relationships between the transition metal composition and the average discharge voltage; the characteristics of the newly developed and other cathode materials are provided for comparison. The horizontal axis shows the percentages of iron, manganese, and titanium (i.e., the total amount of transition metals excluding the amount of cobalt and nickel) with reference to the total amount of transition metals; this indicates the content (in percentage) of inexpensive and resource saving elements. The vertical axis shows the initial average discharge voltage, which indicates the voltage consistency with voltage 4 V of existing cathode materials.
The discharge voltage of the newly developed cathode materials is higher than that of voltage 3 V of previous cathode materials developed at AIST by 0.5 V, and is close to that of existing cathode materials. The latter contain only three transition metals, namely, iron, manganese, and titanium. Use of nickel may increase the cost, but the new materials can replace the existing materials because they do not contain cobalt and their nickel content is comparable to that in the existing cathode materials. Furthermore, the new materials contain a large amount of iron, which is abundant and inexpensive. We can reduce costs and conserve resources by replacing the existing voltage 4 V cathode materials with the new materials of voltage 3.5–3.7 V; the newly developed materials can be practically used as iron containing cathode materials, and they are also easier to use than the previously developed materials.
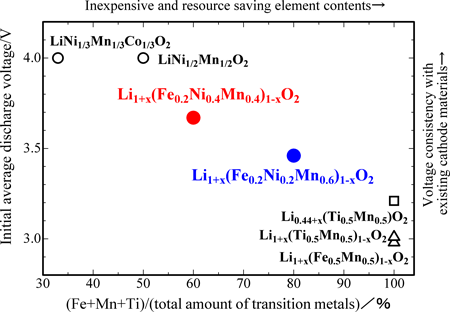
|
Fig. 2 Relationship between initial average discharge voltage and percentages of iron, manganese, and titanium with reference to the total amount of transition metals in the newly developed cathode materials; the characteristics of the two existing cathode materials, and the three cathode materials previously developed at AIST are shown for comparison. |
The fabrication process will be stabilized in order to supply samples to battery manufacturers in early 2010. Research on the composition of oxides and fabrication conditions will be advanced to achieve good charge and discharge characteristics in materials containing a large amount of iron.