- Towards the building of a compact hydrogen fueling station using formic acid -
Hajime Kawanami (Leader) and Masayuki Iguchi (AIST Postdoctoral Researcher), the Micro Flow Chemistry Group, the Research Institute for Chemical Process Technology (Director: Satoshi Hamakawa), the National Institute of Advanced Industrial Science and Technology (AIST; President: Ryoji Chubachi), and Yuichiro Himeda (Chief Senior Researcher), the Hydrogen Energy Carrier Team, the Renewable Energy Research Center (Director: Shigeru Niki), AIST, have developed a technology for continuous supply of high-pressure hydrogen from formic acid without using a compressor.
The developed technology can easily and continuously produce high-pressure hydrogen of 40 MPa or higher without any compressor through the decomposition of formic acid, which is a hydrogen carrier, into hydrogen and carbon dioxide, in the presence of an iridium complex as a catalyst. Existing hydrogen production technologies using hydrogen carriers need to go through multi-stage refining to remove raw materials and impurities. On the contrary, the developed technology uses the fact that the carbon dioxide and hydrogen to be refined are under high pressure, so that carbon dioxide can be liquefied and separated easily from the generated gases, producing high-pressure hydrogen solely. Furthermore, theoretical yield of high-pressure hydrogen that could be obtained from the developed technology was 200 MPa or higher, therefore the developed technology possesses sufficient capability of supplying high-pressure hydrogen (at 70 MPa) to fuel cell vehicles, etc., and is expected to greatly reduce the cost of building hydrogen fueling stations in the future.
The technology was developed as a part of research themes of the Strategic Basic Research Programs (CREST) of the Japan Science and Technology Agency (JST). The results will be presented at PACIFICHEM held on December 15 - 20, 2015, in Honolulu, USA. The results were also published in a German scientific journal, ChemCatChem, on December 10, 2015 (http://doi.wiley.com/10.1002/cctc.201501296).
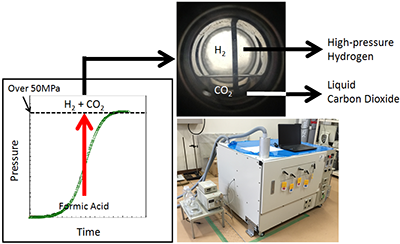 |
Diagram of the developed method for continuous production of high-pressure hydrogen |
In recent years, fuel cell vehicles are commercialized in Japan, and the number of hydrogen fueling stations is quickly growing. However, establishing hydrogen fueling stations requires expensive equipment, and maintenance costs. In particular, the compressors used to compress hydrogen account for about 30 % of equipment costs (or about 45 % including pressure accumulators). Furthermore, the cost of compressing hydrogen makes up about 50 % of the price of the hydrogen supply. Therefore finding a cost-effective and energy-saving way in the compression process when producing high-pressure hydrogen would have a great impact not only on the establishment of hydrogen fueling stations, but also on the hydrogen supply with cost reduction, which consequently expands the use of hydrogen in society. Thus, there is a strong need for a technology that can produce high-pressure hydrogen at low cost and with minimal energy consumption.
AIST is pursuing research and development of high-efficiency hydrogen production systems using hydrogen carriers. Using formic acid as a new hydrogen carrier, recent research has striven to innovate a high-pressure hydrogen production process that uses less energy and has extremely low costs that has been difficult to realize up to now. A highly efficient iridium complex catalyst has already been developed for hydrogen production process technology using formic acid as the hydrogen carrier at a temperature of lower than 100 °C (AIST press release on March 19, 2012). However, hydrogen produced from formic acid contains an equimolar amount of carbon dioxide. Supplying hydrogen to a fuel cell vehicle requires a refining process to remove carbon dioxide as well as a process to compress hydrogen to a high-pressure state. This research, therefore, sought to produce high-pressure hydrogen with an iridium complex catalyst and additionally use the high pressure to separate hydrogen from carbon dioxide to develop a technology for rapid and easy production of high-pressure hydrogen of 40 MPa or highter from formic acid.
This research and development was supported by the research project “Development of efficient production of high-pressure hydrogen by dehydrogenation of formic acid (FY2013 - 2018)” (Research Director: Yuichiro Himeda) within the project “Creation of Innovative Core Technology for Manufacture and Use of Energy Carriers from Renewable Energy” (Research Supervisor: Koichi Eguchi, Professor, Graduate School of Engineering, Kyoto University) of the Strategic Basic Research Programs (CREST) of the Japan Science and Technology Agency.
The developed technology uses a reaction that efficiently produces hydrogen from formic acid with an iridium complex, and thus is able to extract chemical energy as pressure energy and generate high-pressure hydrogen. Using this technology, it is possible to supply high-pressure hydrogen easily and continuously without using any compressor. For the reaction, formic acid and the iridium complex catalyst are placed in a pressure-resistant reaction vessel and the reaction is occurred at 80 °C, which produces high-pressure hydrogen and carbon dioxide gases of 40 MPa or higher easily and continuously (Fig. 1). It is theoretically possible to produce high-pressure gas of 225 MPa, and pressures of up to 50 MPa have been confirmed at this time. The speed of pressure increase per gram of metal used in the catalyst is approximately 1.2 MPa/sec/g-metal (4378 MPa/h/g-metal). The rate of gas production at 40 MPa is 224 L/h/g. This is more than double of the rate using a ruthenium complex catalyst which was reported in the literature. The only high-pressure gases produced are hydrogen and carbon dioxide. Although there is a possibility of the generation of carbon monoxide as a by-product in the formic acid decomposition, none was detected with the developed technology.
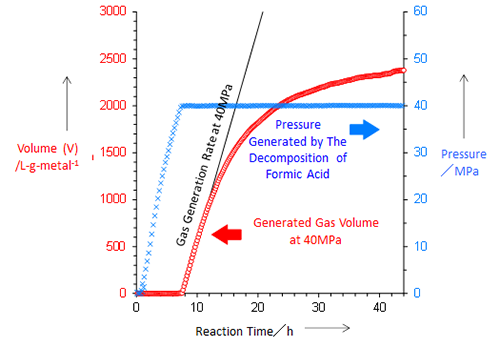 |
Figure 1: Amount and pressure of hydrogen and carbon dioxide produced from formic acid |
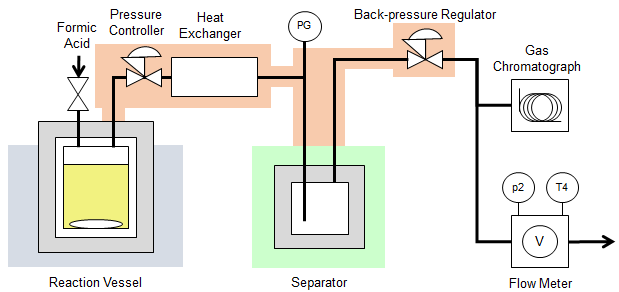 |
Figure 2: Diagram of reaction equipment |
The high-pressure gas of 30 MPa, consisting of hydrogen and carbon dioxide, produced from formic acid was rapidly cooled to -10 °C with a micro heat exchanger (Fig. 2). At that point, the homogeneous phase was separated into gaseous and liquid phases easily (Fig. 3). If the cooling temperature is lowered to -50 °C, measurements of the gaseous phase show 85 % hydrogen (and 15 % carbon dioxide). The process uses the phenomenon that when the generated hydrogen and carbon dioxide in the homogeneous phase as a supercritical fluid are instantly chilled so they change from a supercritical state to a high-pressure state, the mixture separates into two phases: gaseous (mainly hydrogen) and liquid (mainly carbon dioxide).
Moreover, using this method it is possible to refine hydrogen up to 93 % under ideal conditions. In the future, the researchers’ target will be the production of high-pressure hydrogen of high purity for practical use (99.99 % or higher purity) from formic acid by combining this method with heat exchangers that can chill the mixture more rapidly and with a separate technology that absorbs and removes carbon dioxide under high pressure.
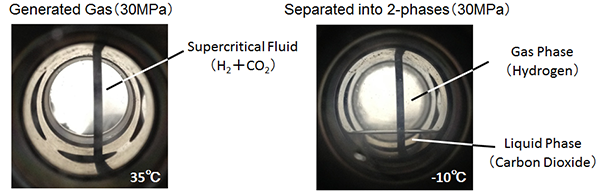 |
Figure 3: Produced high-pressure gases (hydrogen and carbon dioxide) and the same gases separated into two phases |
The researchers are aiming at a level closer to practical use as a technology that can minimize both the number of compressors needed to be installed during the construction of hydrogen fueling stations and the amount of compression energy required during operation. Specifically, they are aiming at a technology that can produce hydrogen of 70 MPa pressure with purity approaching 99.999 %. In addition, further research and development will be conducted to build an ideal hydrogen carrier system that also utilizes the high-pressure liquid carbon dioxide generated from the process.