- Towards the full-scale development of a novel technique for producing secondary batteries using aerosol deposition -
Jun Akedo (Prime Senior Researcher) of the Advanced Manufacturing Research Institute (AMRI; Director: Norimitsu Murayama), the National Institute of Advanced Industrial Science and Technology (AIST; President: Tamotsu Nomakuchi), and Daniel Popovici (AIST Postdoctoral Researcher) of the Integration Process Technology Group (Leader: Jun Akedo), AMRI, AIST, in collaboration with Seigou Fujishima (Leader), Hideyuki Nagai (Technical Staff) and others of Department for Development of Battery Production Technology (Vice-president and Director: Yasuo Ishiguro), Toyota Motor Corporation (TOYOTA; president and CEO: Akio Toyoda), have prepared an all-solid-state thin-film lithium (Li)-ion battery prototype (Fig. 1) using the aerosol deposition method (AD method), a room-temperature high-speed coating process for ceramics that was developed by AIST. The prototype consists of three thin layers of oxides, a cathode, an anode, and a solid electrolyte, deposited on a metal substrate. This prototype was able to charge and discharge successfully, its operation as a storage battery being demonstrated for the first time in the world.
Unlike conventional thin film forming, AD method does not require heating of substrates and can be used to easily thicken films. Therefore, a film can be formed within a short period of time, offering prospects of the improved efficiency of storage battery production and substantial reduction in processing costs. We will continue our cooperative development aiming at practical all-solid-state batteries fabricated using AD method.
The results of this study will be presented at the 3rd International Congress on Ceramics (ICC3) that will be held at Osaka International Convention Center in Osaka, Japan, from November 14 to 18, 2010.
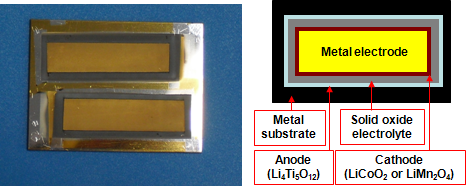 |
Figure 1 : All-solid-state Li-ion battery prototype |
To address energy and environmental issues, performance improvement in plug-in hybrid vehicles and electric vehicles has been pursued. In this context, the development of a high-energy-density next-generation storage battery technology is the key to significant improvement in the performance of these vehicles, and efforts in the aspects of materials and manufacturing processes have become important.
An all-solid-state Li-ion battery that is one of the next-generation storage batteries uses a non-flammable solid-state electrolyte with no fluidity. This enables control systems to be simplified, for example by using unit cells connected in series in one pack, and is expected to yield a battery pack with a high energy density (Fig. 2).
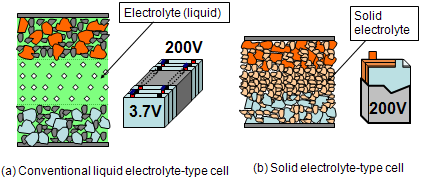 |
Figure 2 : (a) Conventional liquid-electrolyte Li-ion battery and (b) all-solid-state Li-ion battery |
AIST has succeeded in room-temperature fabrication of a 60-cm-square highly transparent ceramic thick film using AD method, a high-speed coating technique at room temperature (AIST press release, May 20, 2004). AIST has been addressing thinning and thickening of film materials for Li batteries since 2006 by utilizing this room-temperature process.
Meanwhile, TOYOTA has been addressing the need to reduce oil consumption and diversify energy supplies by focusing on hybrid vehicle technology to strengthen low-carbon-oriented activities including “turning to energy alternatives to petroleum,” “reducing CO2 emissions (a measure against global warming)”, and “prevention of air pollution.” There has been ongoing R&D of innovative next-generation batteries that will surpass conventional liquid Li-ion batteries in performance and will be crucial for alternative-fuel vehicles including plug-in hybrid vehicles and electric vehicles.
AIST and TOYOTA have launched cooperative research aiming at the development of next-generation batteries by merging their respective technologies.
All-solid-state Li-ion batteries use solid-state electrolytes to replace the liquid electrolyte of the conventional Li-ion batteries. Solid electrolytes have much less ionic conductivities than those of liquid electrolytes. Therefore, in the development of all-solid-state batteries, it is important to make an electrolyte layer thinner while maintaining electrical insulation and to search for solid electrolyte materials with increased ionic conductivity in order to increase the ion conductivity of the electrolyte layer.
There have been some reports of bulk battery prototypes using solid-state sulfide electrolytes with high conductivity. Sulfide materials, however, present difficulties in the preparation of densified structures or the fabrication of thin films. Also, sulfides tend to generate hydrogen sulfide gas and to react with water and deteriorate. To form a battery, a sulfide electrolyte is sandwiched between a cathode and an anode and pressed at room temperature. As the density of electrolyte cannot be increased by the press molding, the battery does not exhibit acceptable properties. Fine interfaces between the electrolyte layer and the electrodes have to be formed in order to avoid disturbance of ionic conduction, but the interface forming also comes with some problems. Sintering, a conventional ceramic technique, can be used to fabricate a cathode, an electrolyte, and an anode. High temperature sintering is required to form a high-density solid electrolyte layer and to obtain a sufficiently thin electrolyte layer. Because of high reactivity of Li compounds, mutual diffusion at the interfaces occurs and it is difficult to form fine interfaces. Although there have been some reports of all-solid-state thin-film oxides batteries prepared by spattering and other conventional thin-film forming methods, these methods require heating of a substrate and/or post-film formation thermal processes and a long time for film forming. Therefore, using conventional techniques, there are problems related to fabrication of larger batteries and cost reduction in battery production.
Theoretically, AD method enables a highly dense solid-state electrolyte thin film to be formed at room temperature and its successful deposition between the cathode and the anode layers. In this study, we examined various Li oxide materials as solid electrolyte materials and solid electrolyte films with ionic conductivity of 3 to 5 × 10-6 (S/cm) were formed by using AD method with optimized conditions and suitable particulate raw materials. We also used common electrode materials, i.e. LiCoO2 or LiMn2O4 as the cathode and Li4Ti5O12 as the anode. Then the three layers forming the battery cell structure were fabricated using AD method (Fig. 3).
Very high impacting pressure (over 3 GPa) is applied to raw material particles when they collide with the substrate in AD method. The AD process is the powder compaction process that is using very high impacting pressure to ensure deposition of highly dense layers at room temperature. In addition, this high pressure is applied only to parts of the substrate and the underlayer surfaces for a limited time, thus damage to the substrate and the interfaces between the layers is minimum and mutual diffusion caused by heat is not observed. In this study, an oxide-based all-solid-state thin-film Li-ion battery was prepared by optimizing the thicknesses of the cathode, the anode, and the electrolyte layer (Fig. 4). The charge–discharge property of such type of battery was confirmed for the first time in the world.
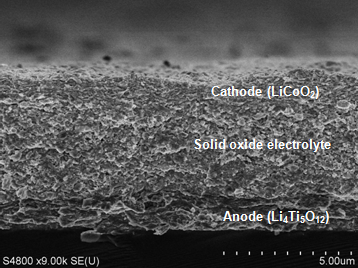 |
Figure 3 : Cross-sectional structure of a three-layer fabricated film consisting of a solid-state oxide electrolyte layer sandwiched between a cathode (LiCoO2 or LiMn2O4) and an anode (Li4Ti5O12) |
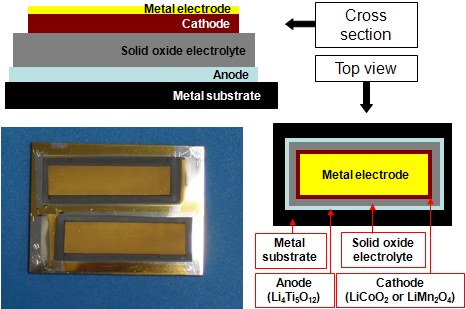 |
Figure 4 : Prototype of the all-solid-state Li-ion battery |
The all-solid-state Li-ion battery prototype is still in an early stage of development and its performance has not yet reached a practical level. However, the operation of the oxide-based all-solid-state Li-ion battery fabricated using AD method, a room-temperature process, proves that AD method is one of the promising methods for storage battery production. By optimizing the microstructure of the thin films, as well as by searching for solid electrolyte materials with higher performance, we aim to realize an all-solid-state Li-ion battery that will have better performance than conventional Li-ion batteries.