- A safe and secure production process has been achieved using MEMS technology -
Sohei Matsumoto (Leader) and Tomoya Inoue (Senior Research Scientist) et al., Hetero Convergence Team, Research Center for Ubiquitous MEMS and Micro Engineering (Director: Ryutaro Maeda), the National Institute of Advanced Industrial Science and Technology (AIST; President: Tamotsu Nomakuchi), have developed a direct synthesis process for hydrogen peroxide production through a microreactor, applying micro-electromechanical systems (MEMS) technology to its fabrication, in collaboration with Mitsubishi Gas Chemical Company, Inc. (MGC; President: Kazuo Sakai).
This technology has been developed by combining AIST's MEMS and microreactor technologies with MGC's catalyst technology. It enables the production of hydrogen peroxide solution at a required concentration, with hydrogen and oxygen directly reacted under comparatively conditions, namely at room temperature and at a pressure of 10 atm.
Details of this technology will be presented at the Meeting of Catalysis Society of Japan to be held from September 15 to 18 in Kofu, Yamanashi.
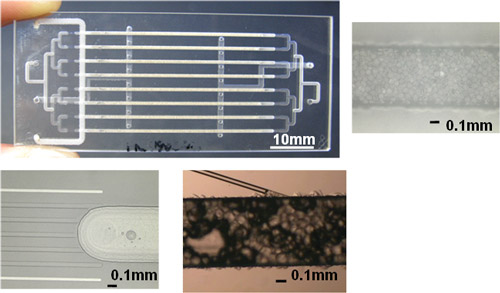 |
Figure : Microreactor used in the production of hydrogen peroxide at concentrations higher than 10 % |
Hydrogen peroxide is a basic chemical with a wide range of applications from household disinfection to washing in semiconductor processes. It is produced mostly in petrochemical complexes, but no practical process has ever been realized that allows on-site production of hydrogen peroxide for a wide variety of applications in required quantities. In the on-site production of hydrogen peroxide, the direct synthesis from hydrogen and oxygen is preferable in terms of environmental benignity and reduction of carbon emissions, a process expected to be made into a reality. It has long been studied as a way of significantly simplifying the current production process. However, this alternative requires the elimination of the danger of an explosion as well as the high reaction pressure (50 to 100 atm), which makes it difficult to achieve safety and economy simultaneously. Due to this fact, it has not been put to practical use yet.
In recent years, the use of microreactors in production processes to ensure the safety and security has attracted attention. We have so far studied and demonstrated low-environmental-load chemical processes using microreactor technology. The application of microreactor technology to the direct synthesis of hydrogen peroxide has been explored globally. Despite the worldwide efforts, it has remained difficult to produce hydrogen peroxide directly at a concentration of 1 % or more. This is because a sophisticated combination of microfabrication techniques is required to develop a microreactor and the catalysts suitable for the direct synthesis are not used effectively.
AIST has developed an original, new glass microreactor by advancing the microchemical chip fabricaion technology developed by Prof. Takehiko Kitamori, Department of Applied Chemistry, Graduate School of Engineering, the University of Tokyo and Micro Chemistry Group, Kanagawa Academy of Science and Technology (Leader: Prof. Takehiko Kitamori; the project was completed in March 2009). MGC, which has high potential in the area of catalyst technology, is focusing on the development of a new hydrogen peroxide production process, while it has been accelerating the overseas business of hydrogen peroxide and started the operation of a new plant in China in 2009. By combining the technologies of both AIST and MGC, we have developed a new method for direct synthesis of highly concentrated hydrogen peroxide.
A part of this research was supported by a Grant for Industrial Technology Research of the New Energy and Industrial Technology Development Organization.
The developed direct synthesis process safely produces hydrogen peroxide from hydrogen and oxygen by using a microreactor. In a world first, it can produce hydrogen peroxide at concentrations higher than 10 % under mild conditions, namely at room temperature and at a pressure of 10 atm, while maintaining a high yield of more than 40 % against hydrogen.
The technology has three characteristics.
First, the optimum reaction field has been prepared by the use of microchannels filled with catalysts. By limiting the width of the microchannel to approximately 600 μm, the safety of the direct reaction between hydrogen and oxygen is ensured. This is a mixed phase reaction among three phases: gas (hydrogen and oxygen), liquid (aqueous solution), and solid (solid catalyst). The microchannel requires a structure that enables a uniform mixing of gas and liquid on solid catalysts, and we have successfully formed this with MEMS technology. Figure 1 shows the structure of the microreactor (one channel) developed for the gas-liquid mixed-phase reaction.
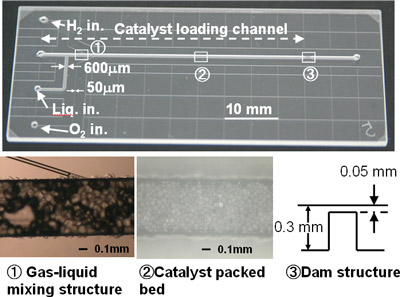 |
Figure 1 : Microreactor (one channel) for the gas-liquid mixed-phase reaction |
Second, we have developed a reaction process by forming multiple microchannels in parallel in a microreactor. One of the issues involved in chemical processes that employ microreactors is how a technique (numbering-up) to enhance productivity should be included while taking advantage of the characteristics. Whether the numbering-up succeeds or not depends on achieving the high uniformity of reaction conditions in each of the microchannels arranged in parallel. Figure 2 shows the numbered-up microreactor and the successful microstructure leading to uniform distribution of liquid phase.
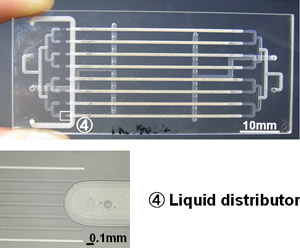 |
Figure 2 : Numbered-up microreactor |
The third characteristic is the catalyst. Although the only by-product of the direct synthesis of hydrogen peroxide is water, a catalyst with high selectivity for hydrogen peroxide is essential to achieve the direct production of highly concentrated hydrogen peroxide. AIST and MGC have used the catalyst technology accumulated by MGC to develop catalysts that have much higher hydrogen peroxide selectivity than commercially available ones and the developed catalysts are suitable for use in microchannels. Development of these catalysts has made it possible to produce highly concentrated (more than 10 %) hydrogen peroxide (Fig. 3).
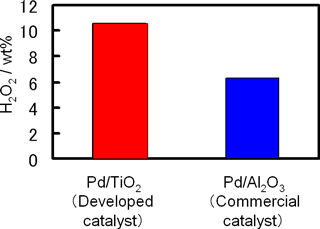 |
Figure 3 : Comparison between the newly developed catalyst (Pd/TiO2) and commercially available conventional catalysts (Pd/Al2O3) |
AIST and MGC will conduct demonstration research on on-site hydrogen peroxide production apparatus while continuing and furthering the collaborative research. This direct synthesis of hydrogen peroxide by using a microreactor is a low-environmental-load process suitable for on-site production of high-purity hydrogen peroxide in required quantities. We aim at its practical use by further developing a numbering-up technique and ancillary equipment for the process.
The results of this research have demonstrated the effectiveness of microreactors in gas-liquid-solid three-phase reactions. This microreactor technology can be applied to a wide range of areas, and we are developing applications such as fine-chemical production.