Update(MM/DD/YYYY):11/08/2010
Development of HRP-4, a Research and Development Platform for Working Humanoid Robots
- Supply to external research organizations from January 2011 -
Points
-
A new lightweight and slim body following the legacy of the HRP Series
-
Cost reduction by optimizing the specifications, simplifying parts, and adopting common parts
-
Improved research efficiency due to the adoption of OpenRTM-aist, which enables the use of domestic and international software assets
Summary
Kawada Industries, Inc. (Kawada Industries; President: Tadahiro Kawada), a subsidiary of Kawada Technologies, Inc. (President: Tadahiro Kawada), has developed HRP-4, a new research and development platform for working humanoid robots, in collaboration with the National Institute of Advanced Industrial Science and Technology (AIST; President: Tamotsu Nomakuchi). In this joint project, Kawada Industries developed the humanoid robot hardware, while Fumio Kanehiro (Senior Research Scientist), Humanoid Research Group (Leader: Kazuhiro Yokoi), the Intelligent Systems Research Institute of AIST and other members developed the motion control software.
The high-density implementation technology used for HRP-4C, the cybernetic human developed by AIST, is applied to HRP-4. HRP-4 has a total of 34 degrees of freedom, including 7 degrees of freedom for each arm to facilitate object handling and has a slim, lightweight body with a height of 151 cm and weight of 39 kg. Furthermore, the HRP-4 control system adopts a software platform OpenRTM-aist and the Linux kernel with the RT-Preempt patch. Therefore, many domestic and international software assets for robot systems, including OpenHRP3, an open-source robot simulator, can be utilized. HRP-4 is expected to accelerate the research and development of next-generation robot systems necessary for the future robot industry, such as human-cooperative robots capable of operating under various environments.
HRP-4 will be exhibited at the Annual Conference of the Robotics Society of Japan held at Nagoya Institute of Technology from September 22 to 24, 2010.
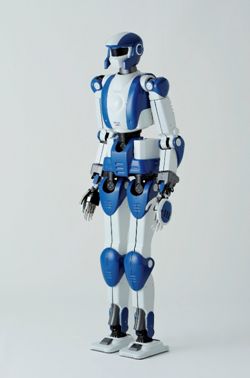 |
HRP-4 |
Social Background of Research
There has been a rapid decline in the birth rate and an increase in the aging population in Japan. Hence, at the beginning of the 21st century, there is an urgent need for the development of robots that can assist or substitute for human beings in simple and repetitive tasks at the places where the robots and human beings coexist. Since work environments, houses, and machines are designed to suit human beings, the use of life-size humanoid robots is expected to help minimize the cost involved in reconstruction of the working or home environment and reduce the overall cost for the society. Life-size humanoid robots are expected as one of the final versions of next-generation robots. In recent years, private companies as well as universities and research institutes have been carrying out active research on such robots.
However, for the industrialization of life-size humanoid robots, it is necessary to address many technological issues. One such issue is reduction of the production cost. At present, the cost reduction issue has been successfully resolved for small humanoid robots (height: 50 cm or lesser), and these robots have been commercialized in domestic and overseas markets. However, these robots have some problems including their size when they are used in serious research in a real environment that includes human activities. For this reason, low-price, life-size humanoid robots are in demand.
In many cases, the software required for the operation of robots is developed from scratch for each type of operation by individual organizations. This is one of the serious impediments to the industrialization of humanoid robots. Further, because of the lack of standards and interface compatibility among systems, a lot of work would be required when reusing the software assets developed by other institutions. Hence, it is expected that the interoperability of software for humanoid robots would be improved by adopting interfaces conforming to international standards.
History of Research
Since March 2003, Kawada Industries, General Robotix, Inc. (GRX; CEO: Takakatsu Isozumi) and AIST have been supplying domestic and overseas universities and research institutes with hardware and control software for the humanoid robot HRP-2, the existing research and development platform for working humanoid robots. However, the platform is still expensive. As eight years have already passed since the development and announcement of HRP-2, the specifications and performance of HRP-2 as well as those of its parts are unsuitable for some of the new research projects. Therefore, there has been a growing demand for a new research and development platform for working humanoid robots.
AIST has developed the cybernetic human HRP-4C as a part of a three-year industry-academia collaboration project launched in FY 2006, "User Centered Robot Open Architecture" (UCROA) under the AIST Industrial Transformation Research Initiative. Kawada Industries was in charge of manufacturing the robot. AIST and Kawada Industries took this opportunity to commence the collaborative development of a low-price research and development platform for life-size working humanoid robots in June 2009. We adopted OpenRTM-aist, a software platform developed by AIST, as the control system in order to facilitate the combination of various functional components of robots via a communication network. Thus, we succeeded in the development of HRP-4, a lightweight, compact, and low-cost platform.
HRP-4 has been developed based on the technologies for HRP-2, HRP-3, and HRP-4C, and through the implementation of the patents filed by Honda Motor Co., Ltd.
Details of Research
Kawada Industries, which aims at the business of working humanoid robots that can coexist with human beings, re-examined the design of the existing humanoid robot and made improvements so that they would be well suited for the research on interactive technologies. Some of these improvements included increasing the number of degrees of freedom of both arms, which plays a vital role in object handling, and making the humanoid robot lighter, slimmer, and more compact than the conventional HRP Series robots in order to realize the safe cooperation of the robot with human beings. In addition, Kawada Industries adopted low power motors (lower than 80 W) for the joint shafts of the robot to respond to the safety demand for robots. Thus, HRP-4, a new research and development platform for working humanoid robots, has been realized. The specific features of HRP-4 are listed below:
-
34 degrees of freedom, including 7 degrees of freedom for each arm, and a slim body with a height of 151 cm and weight of 39 kg (the conventional HRP-2 has 30 degrees of freedom, with a height of 154 cm and weight of 58 kg)
-
Low power motors operating at 80 W or lower for all joint shafts (safety consideration)
-
Payload of each arm: 0.5 kg
-
Low cost as a result of optimization of the mounted systems and joint shaft structure and the use of common and simple parts in the structural design
-
For enhanced scalability of information processing capacity, a small notebook PC can be equipped on the back
-
Affinity with human beings in terms of appearance designed with the "slim athlete" concept
Figure 1
|
Figure 2
|
AIST developed a motion control system and adopted the Linux kernel with the RT-Preempt patch to ensure that the OS is suited for hard real-time processing. Thus, the development of real-time software programs utilizing the standard POSIX API and the effective use of multicore processors, which have gained popularity in recent years, have become possible. AIST adopted OpenRTM-aist as the middleware of the system. OpenRTM-aist is the implementation of RT Middleware, a software basic technology that enables the combination of various functional components of robots via a communication network. The motion control software comprises a group of RT components incorporated with the motion control technologies developed for the HRP Series as the core logic. This enables efficient development of software by utilizing the development tools supporting RT Middleware and the existing RT components. The details of the system are listed as follows:
-
Facilitates stable walking motion with low power motors by succeeding the motion control technologies developed for the HRP Series
-
Provides a robot model compatible with OpenHRP3, a robot simulator, and RT components for motion control
-
Facilitates efficient development because of the use of OpenRTP, a software development tool chain that supports RT Middleware
-
Realization of rich applications by simply combining existing software programs that support RT Middleware, including OpenHRI that provides RT components for voice recognition, voice synthesis, and interaction control for addressing communication functions as well as RT components using the image-processing library OpenCV.
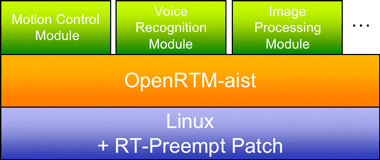 |
Figure : Software system for HRP-4 |
Future Schedule
Efforts will be made to ensure that the total cost for HRP-4 including the maintenance cost is dramatically lower than that for the conventional HRP Series, so that the research and development of humanoid robots is accelerated. Orders for HRP-4 will be received by Kawada Industries, which will begin to manufacture and supply the robots to both domestic and overseas universities and research institutions in January 2011.