Yasumasa Chino (Research Scientist), the Group for Microstructure Control of Materials (Leader: Naobumi Saito), the Materials Research Institute for Sustainable Development (Director: Mamoru Nakamura) of the National Institute of Advanced Industrial Science and Technology (AIST) (President: Hiroyuki Yoshikawa), and Prof. Mamoru Mabuchi of the Department of Energy Science and Technology, Graduate School of Energy Science, Kyoto University, have jointly developed a new rolled Mg alloy with excellent formability at room temperature equivalent to that of Al alloy sheets.
The new Mg alloy sheet is composed of Mg-Zn alloy with a dilute content of rare earth (such as cerium) and processed from hot rolling. The new Mg alloy sheet exhibits an excellent room-temperature formability equivalent to Al alloy sheets (Erichsen value: 9.0). The excellent formability is attributed to a formation of the unique texture in the new Mg alloy sheet.
It is known that room temperature formability of Mg alloy sheets is much lower than that of steel and Al sheets. Thus, it is recognized that press-forming of Mg alloy sheet must be carried out at elevated temperature, where an installation of additional equipments for die and sheet heating is inevitable. On the other hand, an application of the new Mg alloy sheets enables to carry out press-forming at room temperature. This means that a conventional press-forming machine without the heating equipment is available for the press-forming of the new Mg alloy sheet, indicating that a significant cost reduction can be expected.
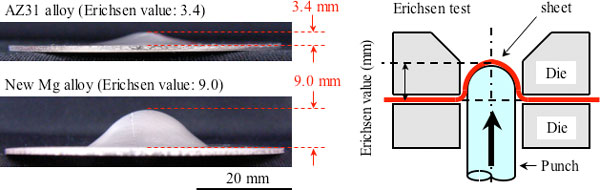 |
Figure 1 Results of Erichsen tests for the AZ31 alloy and the new Mg alloy.
|
Mg alloys are promising structural light materials due to their high specific strength, high specific stiffness, and high Clarke number. Now, the utilization of cast Mg alloy products is expanding, particularly in automobile industry and consumer electronics industry. Hereafter, an application of rolled Mg alloy sheets to their industries will be required for constructing further large light-weight components because of its high specific strength compared with cast Mg alloys. However, since rolled Mg alloys exhibit poor formability at room temperature, press-forming of Mg alloy sheet must be carried out at elevated temperature (around 523 K), where an installation of additional equipments for die and sheet heating is inevitable. This is a main reason for significant cost increase in press-forming of Mg alloy sheets compared with that of the other metal sheets. Therefore, development of new Mg alloy sheets with excellent room-temperature formability is essential for significant cost reduction for press-forming of Mg alloy sheets.
It is well-known that a dilute rare-earth (cerium) addition in Mg promotes cold rollability of Mg sheets. However, a deformation mechanism of the Mg-Ce alloy has not been still clarified. AIST and Kyoto University have a joint research, and revealed that a dilute cerium addition promotes an activity of prismatic slip in Mg.
As a result of the systematic research for alloy design of the new Mg alloy based on the knowledge obtained by the joint research, authors finally found that a hot-rolled Mg-Zn alloy with dilute content of cerium exhibits an excellent room-temperature formability equivalent to that of Al alloys. Then, detailed studies on the texture and room-temperature formability of the new Mg alloy have been continuously carried out.
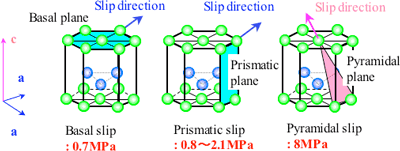 |
Figure 2 Slip planes of magnesium and their critical resolved shear stress.
|
It is known that Mg, whose crystal structure is HCP, shows much poor ductility compared with Al, whose crystal structure is FCC, due to its crystal anisotropy. Figure 2 shows slip planes of Mg and their critical resolved shear stress (CRSS). Slip system of Mg is composed of three slips, which are parallel to basal, prismatic and pyramidal slips. Since, the CRSS of pyramidal slip is much larger than that of the other slips, it is difficult to activate pyramidal slip at room temperature. Thus, slip in the c-axis direction (the vertical direction in Fig. 2) cannot be expected in Mg crystal.
In general, since rolled Mg alloy sheets show the strong basal texture, in which basal plane is distributed parallel to the rolled-sheet surface (See Fig. 3 (a)), basal and prismatic slips can operate parallel to the rolling direction and width direction, but not parallel to the thickness direction (See Fig. 3 (b)). Therefore, rolled Mg alloy sheets hardly deform to the thickness direction, resulting in a fracture at an initial stage of press-forming at room temperature. Thus, it is recognized that press-forming of Mg alloy sheet is extremely difficult at room temperature. For the reason described above, it is important to prevent the strong basal texture formation during hot rolling in order to improve room-temperature formability of Mg alloy sheet.
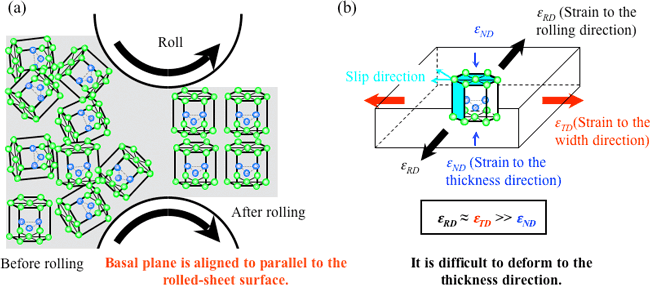 |
Figure 3 (a) Texture formation of rolled Mg alloy, (b) Effects of texture formation of press-forming
|
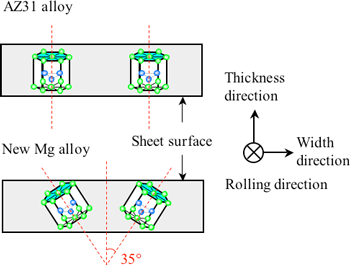 |
Figure 4 Schematic illustrations of the basal plane texture of a current Mg alloy (AZ31 alloy) and the new Mg alloy sheets.
|
The new Mg alloy sheet is composed of Mg-Zn alloy with a dilute content of rare earth (such as cerium), and processed from hot rolling. Figure 4 shows schematic illustrations of the basal plane texture of a current Mg alloy (AZ31 alloy) and the new Mg alloy sheets. In the case of AZ31 alloy sheet, the basal plane tends to distribute parallel to the rolled-sheet surface. On the other hand, the basal plane texture of the new Mg alloy is entirely different from that of AZ31 alloy, where the position of the basal poles (normal line of the basal plane) is tilted by about ±35°from the thickness direction toward the width direction of the rolled sheets. As a result, it is easy for the new Mg alloy to deform to the thickness direction, resulting in the significant improvement of room temperature formability. It is considered that the formation of the unique texture in the new Mg alloy is attributed to an activation of prismatic slip by dilute cerium addition in the new Mg alloy.
Figure 5 shows the relationships between elongation-to-failure obtained by unidirectional tensile tests and Erichsen value obtained by Erichsen tests for Mg alloys and Al alloys. It is known that elongation-to-failure of AZ31 alloy sheets is almost the same as that of Al alloys, but formability (Erichsen value) of A31 alloy sheets is much lower than that of Al alloy sheets. On the other hand, as shown in Figs 1 & 5, the new Mg alloy sheet exhibits an excellent room-temperature formability equivalent to 3000, 5000 and 6000 series Al alloys (Erichsen value: 9.0), indicating that an application of the new Mg alloy promises to realize a press forming at room temperature.
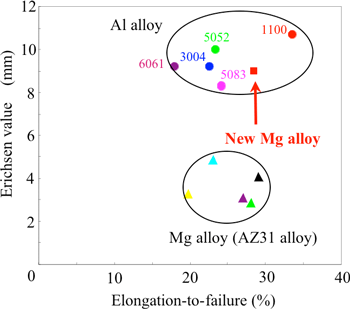 |
Figure 5 Relationships between elongation-to-failure obtained by unidirectional tensile tests and Erichsen value obtained by Erichsen tests for Mg alloys and Al alloys.
|
Feasibility study for the new Mg alloy sheets will be cooperatively carried out with material companies.