Yoshiaki Kinemuchi (Research Scientist) of the Advanced Sintering Technology Group (Group Leader: Koji Watari), the Advanced Manufacturing Research Institute (Director: Hideto Mitome) of the National Institute of Advanced Industrial Science and Technology (AIST) (President: Hiroyuki Yoshikawa) and Hisashi Kaga (former Post-Doctoral Research Scientist of the group) developed a new process, “centrifugally pressurized solidification”, utilizing uniform pressure by centrifugal force, and produced thermoelectric thick films jointly with Sintokogio, Ltd. (Sintokogio) (President: Atsushi Nagai) and Sinto V-Cerax, Ltd. (Sinto V) (President: Etsuzo Kawai) (see Figure 1). This process enables the production of thick films with structure close to a single crystal. The films show thermoelectric performance of the practical level.
A thermoelectric generation device comprising thick films is characterized by its ability to function as a cooling fin and keep a sufficient temperature difference for thermoelectric generation even by natural cooling, and the ability to be applied to curved structure such as exhaust pipes. The newly developed centrifugally pressurized solidification not only produces thermoelectric thick films close to a single crystal but also simplifies the manufacturing process drastically and increases the yield dramatically as compared to the conventional method.
The research results will be presented in the annual meeting of the Ceramic Society of Japan, 2008 (March 21), the spring convention of the Japan Institute of Metals, 2008 (March 27), and the 55th Spring Meeting of The Japan Society of Applied Physics and Related Societies, 2008 (March 30).
|
Fig. 1 Thermoelectric thick film with a thickness of 200µm. (right) The left is a machined substrate.
|
Thermoelectric generation is the technology in which thermal energy is transformed into electric energy directly. This technology can be characterized by excellent reliability, lack of requirement of maintenance, and long life of the equipment used for thermoelectric generation, due to the lack of moving parts. Generation efficiency does not deteriorate despite the small size of thermoelectric modules. A large amount of unused waste heat is produced by manufacturing plants and automobiles. An effective reutilization of such unused heat by thermoelectric generation will significantly contribute to the solution of problems related to energy and the environment, with which our society faces. However, with the exception of special cases, thermoelectric generation has never been used in the private sector because of low energy conversion efficiency and the high production cost of generation devices.
A high-efficiency and low-cost thermoelectric generation technology for collecting waste heat energy as electric energy is strongly desired. In particular, generation devices comprising thick films are regarded as important for the effective utilization of waste energy because they are applicable to a wide variety of thermal energy sources that are dilute and dispersed.
AIST, Sintokogio and Sinto V-Cerax have developed sintering equipment for noncontact pressurization by using centrifugal force (centrifugal sintering), and they have established a technology for thick films, laminated body, and small ceramics (press release of February 2, 2004).
The screen-printing sintering method and the plating method are mainly used to produce thermoelectric thick films. The former method yields a film density as low as 80% because it requires sintering, while the latter method needs complicated processes and it is hard to make films with thicknesses the order of several hundreds of micrometers using the latter method. To solve these problems, we have been conducting joint research to realize thermoelectric films characterized by a high output, low production cost, and small size through the application of centrifugal sintering and its related technologies.
In the newly developed method (centrifugally pressurized solidification), a closed space is created by putting a lid on a mold with grooves (an insulator oxide substrate) after filling a set amount of raw material in the grooves. Then, thick thermoelectric films are produced by melting and subsequent solidifying the raw material while applying centrifugal force along the thickness direction (Figure 2). The produced films have a density of nearly 100%, and the high density contributes to the increase in the output of the films. The method consists of simpler processes than the plating method and enables the production of fairly thick films.
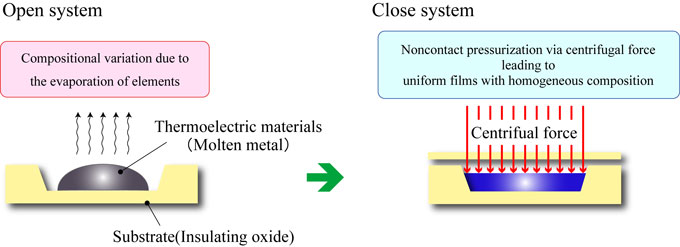 |
Fig. 2 Centrifugally pressurized solidification is the deposition in a close system leading to homogeneous thermoelectric films with high quality.
|
This method has the following three characteristics.
1. It allows for noncontact and uniform pressurization because it uses centrifugal force. It is possible to fabricate uniform films in accordance with the pattern on a substrate due to the uniform pressure. Thus, waste heat can be utilized effectively by designing the pattern in accordance with thermal flow.
2. Heating raw materials inside the closed space does not cause a deviance in the composition of the raw material due to vaporization, and composition of films can be controlled easily. The yield improves because all input raw materials are utilized as thermoelectric devices without vaporization loss and no post-processing is required.
3. It is possible to form a film with a thickness in the range of several tens of micrometers to several millimeters by adjusting the amount of raw materials.
We have produced a thermoelectric thick film of bismuth-telluride (200 µm thick, 3 mm wide, and 12 mm long) by the centrifugally pressurized solidification; the power factor of the film at room temperature is 4.2 × 10-3 W/mK2, and the dimensionless figure of merit exceeds practical level as a thermoelectric material, i.e. 1. As the film has a structure similar to the structure of a single crystal and its c axes are aligned with the direction of the film thickness, high conductivity was achieved, and thus such a high performance was realized.
Figure 3 shows a thick-film thermoelectric device produced by the centrifugally pressurized solidification. We filled the raw materials of p-type and n-type bismuth-telluride alternately in the groove on the substrate, heated the substrate to a temperature higher than the melting point of the raw materials while applying a centrifugal force of 1000 G, and cooled the substrate to produce p-type and n-type thermoelectric thick films. The produced thick-film thermoelectric device (200 µm thick, 1.5 mm wide, and 12 mm long) was composed of seven pairs of p-n pairs, all of which had a high output factor.
As described above, the centrifugally pressurized solidification enables the production of high-performance thick-film thermoelectric devices by simple processes. The thermoelectric devices with a high output, low production cost, and small size would be produced by the new method.
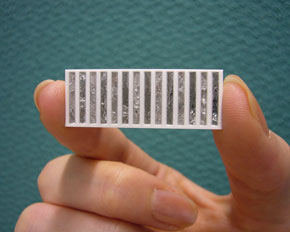 |
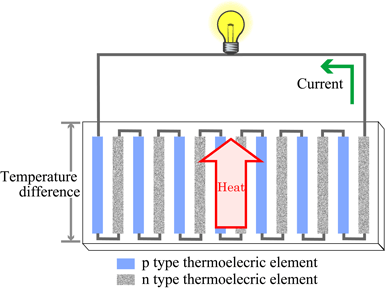 |
Fig. 3 Thick thermoelectric modules consisting of 7 p-n pairs of bismuth telluride.
|
We have developed a revolutionary method termed the centrifugally pressurized solidification for producing high-performance thick-film thermoelectric devices. In the near future, we will develop a practical thermoelectric generation system for the effective utilization of waste heat energy and contribute to solve problems related to energy and the environment.