Advanced Sintering Technology Group of Ceramics Research Institute (CRI), National Institute of Advanced Industrial Science and Technology (AIST), an independent administrative institution, has developed a sintering machine utilizing centrifugal compression (to be designated as centrifugal sintering equipment) in collaboration with Sinto V-Cerax, Ltd., a subsidiary specialized for ceramics business under the Sintokogio, Ltd (Photo 1).
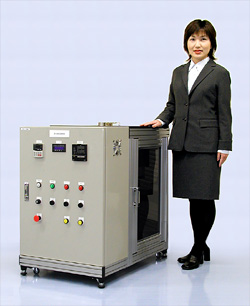 |
Photo 1 |
The centrifugal sintering equipment consists of two parts: rotor unit and heater unit. Sintering proceeds through the following steps: specimen materials are loaded in a high speed rotor (ceramics rotor), the rotor is put to high speed spinning under high temperatures, and the specimen is compressed by centrifugal force to accelerate sintering (Figure). The technique is characterized by nonuse of compressing means such as push rod and gas in comparison to conventional pressure sintering such as hot press or hot isotropic press.
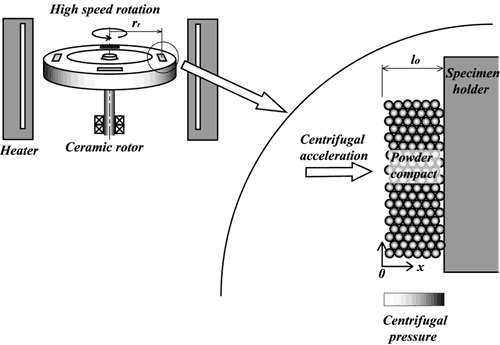 |
Figure |
The further efforts will be concentrated in the application of the new technique to sintering of thin/thick ceramic components on printed circuit board, ceramic-metal laminate, small-sized ceramic device of complicated geometry and so on, to closely examine the competitive edge.
The centrifugal sintering equipment will be exhibited to the “Tokai Manufacturing Cluster Forum 2004” to be held on Monday, February 9, 2004, at the Post-Office Savings Hall (Mielparque Nagoya) under the joint auspices of the Chubu Bureau of Economy, Trade and Industry, and the AIST Chubu.
This study has been entrusted since fiscal year 2001 by the New Energy and Industrial Industry Organization (NEDO), another independent administrative institution.
Currently, more than 80% of fine ceramics industry concerns electronic materials. In particular, rapid progress in dissemination of small-sized mobile phones and down-sizing of electronic devices, it has been urgently requested to miniaturize and integrate condensers, piezoelectric devices, semiconductor devices and circuit board device, and hence, to establish sintering technology suited for this and thick film ceramic components mounted on circuit board, ceramic-metal laminates and small-sized ceramics of complicated geometry.
Sintering often results in cracks and delamination at interfaces between different materials owing to difference in shrinkage behaviors. Up to now, these troubles were effectively avoided by applying pressure vertically to the interface to promote atomic diffusion and plastic flow. With the conventional pressurized sintering using a push rod or other means, specimen surface was contaminated, needing post machining for sintered product. For this reason, crack formation and delamination were to be suppressed by reducing stress at interfaces through slow-down of heating rate, roughening joint faces and compositional control.
In view of imminent needs for miniaturizing electronic devices and market expansion for products, CRI-AIST has been dedicated to the development of innovative pressure sintering process for thin film, thick film and small-sized ceramic components, as well as sintering machine based on this process, in collaboration with Sinto V-Cerax, Ltd.
The basic mechanism of sintering system developed in this study consists in high-speed revolution of rotor at higher temperatures. The rotor and shaft members are made from silicon nitride characterized by light weight, refractoriness and rigidity (Photo 2). The rotor in the present equipment is turned at a speed as fast as 20,000 revolutions per minute (rpm) under temperatures as high as 1,000 ºC. For ensuring shorter sintering cycle, high frequency heating is adopted, to achieve heating and cooling rate faster than 75ºC/min up to 1,000ºC. This makes the sintering process as short as an hour or less, contributing to energy saving.
Available centrifugal force depends upon rotor speed and radius and specific density of specimen. At present, the maximum centrifugal acceleration is 40,000G. For sintering ceramics of specific gravity around 8.0, such as lead titanate, and with rotor speed 20,000rpm, available pressure is 10kPa for 10μm thick film, 100kPa for 100μm, 1MPa for 1mm and 10MPa for 10mm.
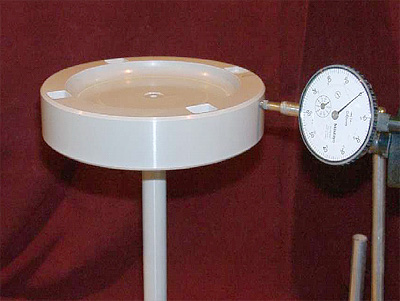 |
Photo 2. Ceramic rotor and shaft |
Further works will include upgrading centrifugal force by increasing rotor speed, developing equipment resistive to temperatures higher than 1,200ºC and applicable to every species of ceramic materials, to open the way to commercialization. Various ceramic materials will be sintered by using the equipment and the products will be characterized.