Update(MM/DD/YYYY):11/25/2014
Efficient Synthesis of Polyurethane Raw Materials from Carbon Dioxide
- Possible to realize an environmentally friendly polyurethane manufacturing process -
Points
-
A new reaction process to synthesize raw materials for polyurethanes from carbon dioxide
-
A high-yield reaction of carbon dioxide, amine, and tin alkoxide to produce aromatic urethane
-
Expectations for achieving an environmentally friendly polyurethane manufacturing process, without the use of highly toxic phosgene
Summary
Jun-Chul Choi (Senior Researcher), Hiroyuki Yasuda (Leader) and others of the Catalyst Design Team, the Interdisciplinary Research Center for Catalytic Chemistry (Director, Kazuhiko Sato), the National Institute of Advanced Industrial Science and Technology (AIST; President: Ryoji Chubachi), have developed a new, high-yield reaction process to obtain aromatic urethane from carbon dioxide (CO2), amine, and tin alkoxide. Aromatic urethane compounds are chemical substances currently used as drugs, agrochemicals, etc., but show high promise as raw materials for polyurethanes.
Currently, highly toxic and corrosive phosgene is used as the raw material for the manufacture of polyurethanes. In addition, a large amount of waste is produced in its manufacturing process and there was a strong demand for conversion to a manufacturing process that was more environmentally friendly.
AIST has been conducting development of an ideal, environmentally friendly urethane synthesis process that theoretically does not produce any waste, by using inexpensive and abundant CO2, amine, and alcohol as its raw materials. However, technology developed until now was limited in the types of urethane it could synthesize, and aromatic urethane, the raw material for polyurethane could not be synthesized. In this study, it was discovered that aromatic urethanes can be synthesized with high yield when amine and tin alkoxide are reacted with high-pressure CO2.
The details of this technology will be presented at the 44th Petroleum-Petrochemical Symposium of JPI to be held at Asahikawa Grand Hotel (Asahikawa, Hokkaido) on October 16 to 18, 2014.
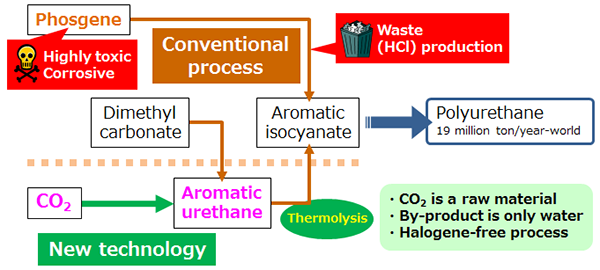 |
Conventional urethane manufacturing process and the developed aromatic urethane synthesis process |
Social Background of Research
With the longing for a safe, secure, and affluent society, the importance of reducing hazardous substances and waste, improving energy efficiency, and converting to the use of recyclable resources as raw materials is increasing. It could be said that the supply of chemical products, materials, and components, based on “green and sustainable chemistry,” is directly linked with sustained development of the chemical industry.
Polyurethane is a material widely used in daily living and building materials, automobile parts, paint, and other uses, and its annual global production reaches 19 million tons (2013). However, currently, a process using phosgene, a highly toxic and corrosive chemical that is a regulated substance under the Act on the Prohibition of Chemical Weapons and the Regulation of Specific Chemicals is used to synthesize raw materials for polyurethane. In addition, it also requires a large amount of chlorine. Because this synthesis process has many problems, there has been a strong demand for alternative synthesis processes that are environmentally friendly.
A process to thermally decompose urethane obtained from a reaction between amine and dimethyl carbonate is known to be a synthesis process that does not use phosgene. However, this requires a separate synthesis of dimethyl carbonate, resulting in a multiple-step reaction process, and the development of a more direct urethane synthesis process was needed. In addition, although there are many types of polyurethane raw material, over 90 % of them contain benzene rings, indicating the importance of aromatic urethane.
History of Research
AIST has been involved in the development of a one-step reaction process to synthesize urethane without any production of waste, using inexpensive and abundant CO2 as the raw material. It has previously found that urethane can be synthesized with a high yield from CO2, amine, and alcohol when a compound containing tin or nickel is used as a catalyst in the presence of acetone dimethyl acetal. The ground-breaking features of this process were that urethane and water produced by the reaction is prevented from reacting again and returning to its raw materials, by acetone dimethyl acetal working as a dehydrating agent, resulting in efficient production of urethane, and that acetone dimethyl acetal can be easily regenerated and recycled. However, with this process, aromatic urethane, the raw material for polyurethane, could not be synthesized.
Details of Research
The developed one-step urethane synthesis process using CO2 as a raw material uses tin alkoxide instead of alcohol. This made it possible to synthesize aromatic urethane with a high yield from CO2 and aromatic amine (a type of amine) without using catalysts (Fig. 1). For example, when CO2 (pressure: 5 MPa, approximately 50 atm), aniline (a type of aromatic amine), and an equivalent amount of dibutyltin dimethoxide (a type of tin alkoxide), were reacted at 150 °C for 20 minutes, corresponding aromatic urethane was obtained at a yield of 41 %. Furthermore, when 5 times dibutyltin dimethoxide was used, the yield reached 82 %. In this instance, the yield of generated byproducts was only 1 %. When 2, 4-diaminotoluene (a type of aromatic amine) actually used in polyurethane manufacturing was used instead of aniline, the yield of the target product was 49 %.
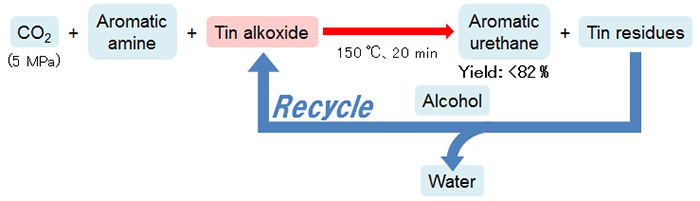 |
Figure 1 : Synthesis of aromatic urethane from CO2, aromatic amine, and tin alkoxide |
Although the developed synthesis process uses tin alkoxide in amounts eqivalent to or greater than amine, the tin residues are recovered after the reaction and tin alkoxide is regenerated when it is reacted with alcohol while removing water. This can be reused in the next reaction. This means that only CO2, aromatic amine, and alcohol are consumed in the entire process, and the only byproduct in the chemical formula is water. In addition, another feature of this process is that it uses no chlorine as a raw material etc.
The developed synthesis process uses recyclable tin alkoxide, and as a total process, it efficiently synthesizes aromatic urethane, a raw material for polyurethane, from CO2, aromatic amine, and alcohol. The reaction process is highly environmentally friendly and economic, and it is expected to lead to innovation in the polyurethane manufacturing process.
Future Plans
Efficiency will be further improved through the optimization of reaction conditions. Furthermore, the adaptability of various types of amine and alcohol will be verified. Optimization of tin alkoxide regeneration conditions and studies for scale-up will also be conducted, with the aim of achieving early practical use.