- Heater output quintupled by high-density packing of high-thermal-conductivity ceramic filler -
Mikinori Hotta (Senior Researcher) and Naoki Kondo (Leader), Ceramic Mechanical Parts Processing Group, the Advanced Manufacturing Research Institute (Director: Masanobu Awano) of the National Institute of Advanced Industrial Science and Technology (AIST; President: Ryoji Chubachi) and Yamato Co., Ltd. (Yamato; Representative Director: Ryuta Tsujii) have developed a high-output immersion heater for heating molten aluminum.
The developed heater uses a ceramic heater tube with excellent corrosion resistance against molten aluminum, packed to high density with high-thermal-conductivity ceramic filler particles. This structure improves the heat transfer from the heater element to the molten aluminum thereby achieving a quintuple increase in heater output in comparison to a conventional heater. This high output will allow reduction in the number of heaters required for heating molten aluminum and is expected to contribute to the reduction of heater equipment and to energy conservation in the metal casting industry.
The results will be exhibited at the “2014 Open Lab of AIST Chubu” to be held at AIST Chubu (Nagoya, Aichi) on June 24 and 25, 2014 and also at the “2014 Japan Die Casting Congress & Exposition” to be held at Pacifico Yokohama (Yokohama, Kanagawa) on November 13 to 15, 2014.
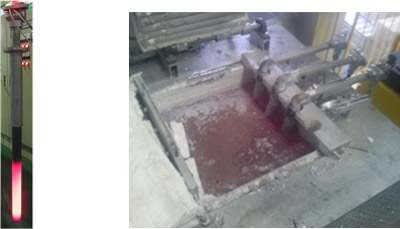 |
The developed immersion heater for molten aluminum heating (Left) and dipping the heater into molten metal (Right)
Conventionally, three heaters are required, but only one developed heater is sufficient for heating. |
In the metal casting industry, metals molten inside a metal melting furnace (molten metals) are heated or have their temperature retained inside a molten metal holding furnace. The main stream in conventional molten metal holding furnaces was radiation heating using oil and gas combustion burners or electrical heaters. However, with radiation heating, the heat is transmitted from the surface of the molten metal, resulting in large radiation loss from the ceiling of the furnace, as well as resulting in the molten metal temperature easily being non-uniform. This being the case, in order to maintain the molten metal at the bottom of the furnace above the melting temperature, the furnace had to be heated to an even higher temperature, resulting in the metal being prone to oxidation, causing problems such as reduction in quality of the molten metal or material loss. To overcome this problem, the use of electric immersion heaters, which are immersed in the molten metal inside the molten metal holding furnace to directly heat and maintain the temperature, is rapidly gaining popularity. The use of this method is expected to result in high temperature controllability and molten metal quality, as well as the reduction in energy consumption and costs.
Conventional immersion heaters were made by inserting a resistance-heating element into a heater tube made of silicon nitride ceramic which has excellent molten metal corrosion resistance. However, heat transfer was insufficient to convey the heat from the heating element to the molten metal through the heater tube, and required the temperature of the heating element to be raised to a temperature (950 °C) that was considerably higher than the molten aluminum temperature (around 700 °C) in the molten aluminum holding furnace. Without improvements in heater output, it was difficult to increase the amount of heat transmitted to the molten metal. Therefore, to provide sufficient heat, the choice was between increasing the number of immersion heaters and to increasing the heating area of the heater by thickening or lengthening the heater tube, which pushed up the heater facility cost. Furthermore, using the heater elements at very high temperatures significantly shortened the heating element life, thereby shortening the heater replacement cycle.
If the heat transfer from the heating element to the molten aluminum can be improved and high output and longer life of immersion heaters achieved, it is expected to reduce heater facilities in the aluminum casting industry and contribute to energy conservation.
AIST has conducted the development of process technology related to the composition of high-thermal-conductivity ceramic filler particles and their filling methods. Yamato has been involved in the manufacture and sale of various electric heaters, such as immersion heaters for casting, and temperature measurement sensors, and the design, manufacture, and sale of industrial furnaces and vacuum facilities. AIST and Yamato conducted a joint research by bringing the strong points of the two together to increase heat transfer by densely packing high-thermal-conductivity ceramic filler particles with the heating element inside a ceramic heater tube and a high-output immersion heater has been developed.
Even in conventional immersion heaters, ceramic filler particles were packed between the heating element and the heater tube, but low filler packing density resulted in insufficient heat transfer. Furthermore, the filler particles were required to be inexpensive and to have electric insulation properties and oxidation resistance at temperatures around 1,000 °C, in addition to high thermal conductivity. In the present study, by optimizing the type, particle-size blending, and packing method of the ceramic filler particles, high-density packing of high-thermal-conductivity ceramic filler particles inside the heater tube inserted with the heating element has been achieved (Fig. 1). As a result, the route for heat transmission through the contact between the filler particles has been secured to achieve a quintuple increase in heat transfer, enabling high heat transfer from the heating element to molten aluminum.
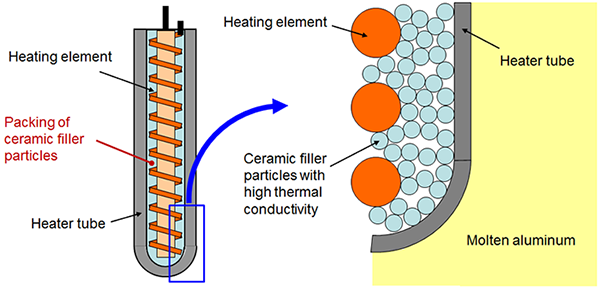 |
Figure 1 : Schematic diagram of the high-density packed high-thermal-conductivity ceramic filler particles |
Figure 2 shows the output of a conventional product and the developed immersion heater using the same heating element. The chart indicates the heat transferred to the molten aluminum as the heater output in relation to the heating element temperature (heater internal temperature) when current is applied to the immersion heater immersed in 700 °C molten aluminum. With conventional immersion heaters, heat transfer from the heating element to the molten aluminum was insufficient, requiring the heating element temperature to be controlled to prevent excessive temperature increase and heating element burnout, making it difficult to obtain high heater output even when the heating element temperature was raised. On the other hand, with the developed immersion heater, heat transfer from the heating element to the molten aluminum is good and high output can be obtained at an even lower heating element temperature.
For example, when 2 kW heater output (blue broken line in Fig. 2) is required, the conventional immersion heater required the heating element temperature to be raised to its operating limit of around 950 °C, but with the developed immersion heater having good thermal conductivity, the heating element temperature could be suppressed to 800 °C or lower. Furthermore, the heating element temperature for prolonged use of the heater is around 850 °C, and when heater output with the heater temperature of 850 °C is compared between the conventional and developed heaters, it can be noted that the developed immersion heater has achieved a quintuple improvement in high output over the conventional heater.
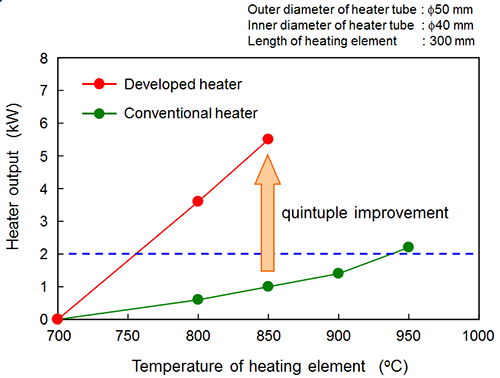 |
Figure 2 : Results of heater output test |
Figure 3 shows an example of the use of the developed immersion heater and its effects. About 5 kWh of heat is required to raise the temperature of 500 kg of molten aluminum from 700 °C to 710 °C in 1 hour using a standard-sized molten metal holding furnace. To achieve this with conventional immersion heaters, it was necessary to use at least three heaters raised to the operational-use limit of heating element temperature, i.e. around 950 °C. On the other hand, only one developed immersion heater, raised to 850 °C, a safe heating element temperature lower than the conventional, was able to raise the molten aluminum temperature. The reduction of the number of heaters is expected to contribute to effects such as (1) approximately 1/3 reduction in the size of heater and its ancillary facilities, (2) an approximately 1/3 reduction in radiant heat loss through reduction of the size of the furnace opening required for the insertion of the heaters, and (3) the reduction of radiant heat loss from the furnace body as a result of reduction of the furnace body outer surface area through the reduction of the size of the furnace body. In addition, since the heating element temperature of the immersion heater can be suppressed, a longer service life of heaters can also be expected. With these, cost reduction in heater facilities and energy conservation of the metal casting industry can be anticipated.
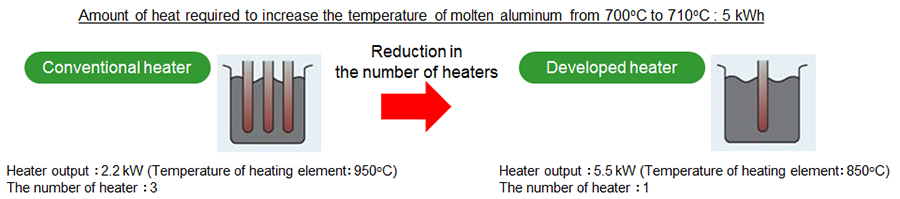 |
Figure 3 : Example of use and effects of the developed immersion heater |
Application of the immersion heater for metal melting furnace by further increasing its output, and the development of a compact and energy-conserving furnace are planned.