- Easy fabrication by bonding substrates together that can be easily scaled up -
Kazuki Tajima (Senior Researcher), Energy Control Thin Film Group (Leader: Kazuki Yoshimura), the Materials Research Institute for Sustainable Development (Director: Mamoru Nakamura) of the National Institute of Advanced Industrial Science and Technology (AIST; President: Tamotsu Nomakuchi), has developed a new fabrication technology that can lead to low-cost, large-scale, low-voltage driven switchable mirror devices.
A switchable mirror device is an electrochromic device that can switch between the mirror state and the transparent state when a voltage of a few volts is applied. The developed technology is a technology for the fabrication of switchable mirror devices; first, functional layers, including a switchable mirror layer and an ion storage layer, are formed on transparent substrates, and then these substrates are bonded together with an adhesive electrolyte. The technology has advantages in productivity, cost reduction, stability, and scale-up over the conventional device fabrication process, in which functional layers are formed one after another on a single transparent substrate. It provides a feasible option for fabricating switchable mirror devices, which will dramatically expand the uses and applications of switchable mirror devices.
Details of this technology will be presented at the 11th International Nanotechnology Exhibition & Conference (nano tech 2012) to be held at Tokyo Big Sight in Koto, Tokyo on February 15-17, 2012.
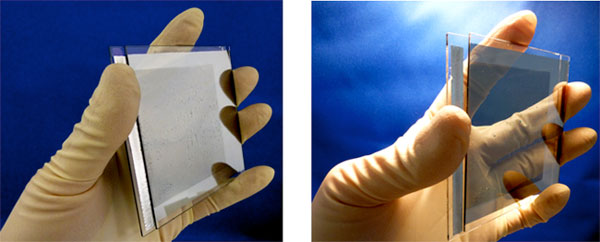 |
Figure 1 : Change in the appearance of the developed switchable mirror device (left: mirror state; right: transparent state) |
Window glass of houses, office buildings, vehicles, and trains functions to bring in sunlight. It also brings in much of the heat energy (infrared light) of sunlight and increases the cooling load in summer. In recent years, the use of insulating windows such as double glazing has been promoted to reduce the cooling load. For further energy savings, it is necessary to control the amount of sunlight brought in freely according to the season, weather, and time. Glass that allows users to control the amount of sunlight passing through is called smart window. Some such products are commercially available. However, in many cases, the amount of light passing through the glass is controlled by electrically coloring the thin film coating on the glass and thereby absorbing excess light. As a result, such products have the drawback that the absorbed light increases the glass temperature and the radiated heat from the glass is released into the room. The developed switchable mirror controls the amount of light by reflecting the light instead of absorbing it, and the glass temperature is not increased. It can effectively block sunlight by switching between the mirror state and the transparent state and is thus expected to significantly reduce cooling load.
AIST is conducting research and development of the application of switchable mirror thin film materials to smart window. There are two types of switchable mirror based on their working principles: gasochromic type that control light with diluted hydrogen gas and electrochromic type that control light by electrically transporting hydrogen ions (protons). AIST has discovered an original gasochromic material for a switchable mirror thin film (AIST press release on August 4, 2010) and has fabricated a solid-state electrochromic switchable mirror film (AIST press release on November 21, 2007). The electrochromic switchable mirror has a multilayer structure. In order to increase the size of the mirror according to its use, the process time needs to be reduced to achieve high productivity and low cost, and high hydrogen ion conductivity in the layer needs to be provided to stabilize switching performance. AIST has conducted research and development to make improvements in these areas.
The developed technology enables the fabrication of a switchable mirror device by bonding together transparent substrates with functional layers using an adhesive electrolyte. The adhesive electrolyte plays two roles: as an adhesive to bond the substrates together and as an electrolyte with high hydrogen ion conductivity. This technology can significantly reduce process time compared to the conventional technology, in which functional layers are formed one by one on a single transparent substrate by magnetron sputtering. For example, the conventional technology utilizes vacuum processes requiring time to stabilize the vacuum state. Further, it employs reactive magnetron sputtering to form a solid electrolyte layer (oxide) which requires a process time of several tens of minutes. In addition, the functional layers are exposed to the air and a protective layer needs to be formed to mitigate the environmental degradation of the layers. In the developed technology, a device can be easily fabricated by forming an adhesive electrolyte by the coating process in a few minutes and then bonding the substrates together (Fig. 2). In addition, conventional electrolyte solutions are liquids and require a sealing structure for leakage prevention. In the developed technology, the electrolyte solidifies at room temperature in the air and acts as an adhesive electrolyte and a packaging material of the device. Therefore, a sealing structure is not required and high stability of performance is expected.
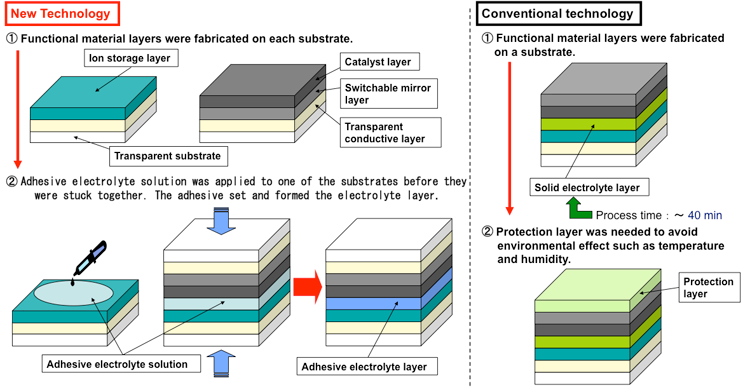 |
Figure 2 : Comparison of switchable mirror device fabrication processes |
The developed switchable mirror device typically consists of a transparent substrate, a transparent electrode, a switchable mirror layer (metal), a catalyst layer (metal), an adhesive electrolyte, an ion storage layer (oxide), a transparent electrode, and a transparent substrate layered in this order. After fabrication, the device has hydrogen ions in the ion storage layer and its state changes when the hydrogen ions move according to the polarity (plus or minus) of the applied voltage. When voltage is applied so that the hydrogen ions move toward the switchable mirror layer, the transported ions react with the switchable mirror layer, forming metal hydride (Fig. 3, right). Since the metal hydride is transparent, the device changes from the mirror state to the transparent state. This change is reversible. When voltage of the opposite polarity is applied, the hydrogen ions move out of the metal hydride in the switchable mirror layer and the layer returns to the original metal, returning the device to the mirror state (Fig. 3, left). The device can be switched between the mirror state and the transparent state by applying voltage. The amounts of transmitted and reflected light can be controlled freely using this switching process.
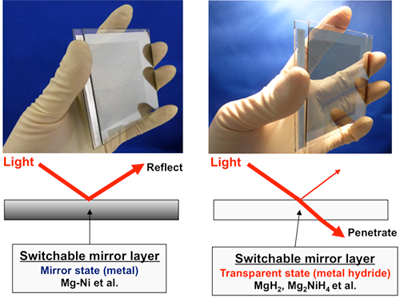 |
Figure 3 : Switching of the states of the switchable mirror device (left: mirror state; right: transparent state) |
Figure 4 shows the photos of switchable mirror devices fabricated using various substrate materials. Since the developed technology can fabricate a switchable mirror device at room temperature, it is possible to use a non-heat resistant resin as the substrate material. Different materials can be bonded together using this technology. For example, glass can be bonded to poly(ethylene naphthalate) (PEN) and PEN can be bonded to poly(ethylene terephthalate) (PET). A large switchable mirror device can be easily fabricated (for example, the 150 mm-square device in Fig. 4 is 25 times as large as those fabricated by the conventional technology.) The switching speed of a device fabricated by the conventional process decreases with increasing size. In contrast, the adhesive electrolyte used in this technology has high hydrogen ion conductivity, allowing smooth transfer of hydrogen ions; and therefore the switching speed does not decrease with increasing size. In addition, while a device fabricated by the conventional technology normally requires a driving voltage of ±5 V, the device fabricated by the developed technology can be driven at a low voltage of ±1 V, due to the above properties of the adhesive electrolyte.
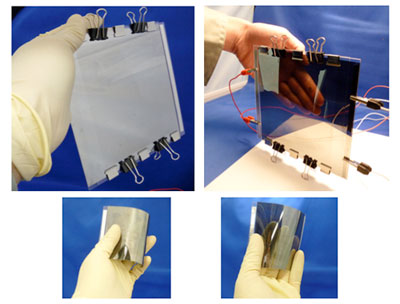 |
Figure 4 : Photos of the switchable mirror devices using various substrate materials (Top left: glass + PEN (mirror state),
substrate size: 150 mm-square; top right: glass + PEN (transparent state), substrate size: 150 mm-square;
bottom left: PEN + PET (mirror state), substrate size: 80 mm-square;
bottom right: PEN + PET (transparent state), substrate size: 80 mm-square) |
Figure 5 shows changes in the optical spectra of the developed switchable mirror device. It shows that the device transmits almost no light in the mirror state (shown in red). The maximum transmittance and reflectance, and amounts of the changes achieved by switching can be freely altered through structural control of the functional thin films in the device.
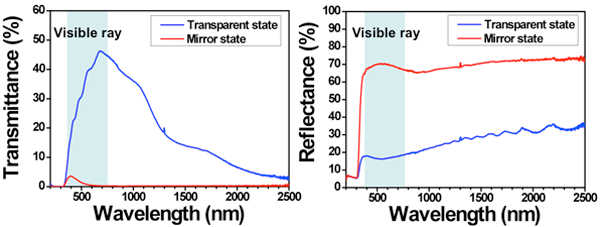 |
Figure 5 : Changes in the optical spectra of the developed switchable mirror device
(Substrate: glass; left: change in transmission spectrum; right: change in reflection spectrum) |
The developed technology that uses the coating process to bond substrates together provides a feasible option for fabricating switchable mirror devices. Either this technology or the conventional technology using magnetron sputtering can be used, depending on the use and size of the switchable mirror device. Most notably, the coating process can use industrial printing techniques. The technology is expected to lead to a basic process for the mass production and scale-up of switchable mirror devices.
Switchable mirror devices are driven only by electricity and expected to be used in a wide variety of applications, including energy-saving windows for houses, office buildings, vehicles, and trains, and electronic and optical devices, toys, and addition to existing products. The researcher will develop a more adaptable fabrication technology to meet various specifications for expected applications of the device. He will also work to develop various switching abilities, including high durability and selectivity of abilities to change optical characteristics.