Takeo Yamada (Senior Researcher), Super Growth CNT Team (Leader: Kenji Hata), the Nanotube Research Center (Director: Sumio Iijima) of the National Institute of Advanced Industrial Science and Technology (AIST; President: Tamotsu Nomakuchi), has developed a strain sensor with oriented single-walled carbon nanotube (single-walled CNT) films bonded to a stretchable polymer substrate. The sensor can measure strains by detecting changes in the electrical resistance of the films.
This CNT strain sensor can detect strains of up to 280%, about 50 times those detected by conventional metal strain sensors. It is durable for more than 10,000 repeated applications of strains less than 150% and has a strain response time of only 14 ms—the shortest for sensors that can measure large strains of more than 100%. In addition, the sensor is less prone to creep than strain sensors made of a composite of an electrically conductive material and a polymer and is more than 20 times faster in creep recovery.
The CNT strain sensor can be easily attached to clothing or the body to monitor knee bending and straightening, finger movement, breathing, and voice production. It is likely to be used in future wearable devices, and it is expected to be used in recreational and medical applications (Figure).
This study was conducted as part of the research project “Functional Integrated CNT Flexible Nano MEMS Devices Fabricated by Self-Assembling Processes” (Research Director: Kenji Hata) in the research area “Creation of Nanosystems with Novel Function through Process Integration” (Research Supervisor: Junichi Sone, Vice President of the National Institute of Materials Science) of the Core Research of Evolutional Science and Technology. This project is funded by the Japan Science and Technology Agency.
Details of the study will be published online on March 28, 2011 (Japan time) in Nature Nanotechnology, a British scientific journal.
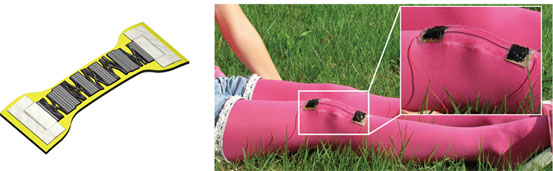 |
Figure : Left: Schematic of the CNT sensor Right: Application as a device to monitor knee movement |
With increasing attention being given to the development of wearable and ubiquitous devices, soft devices, rather than the hard and brittle conventional silicon devices, are becoming increasingly important, while various devices are being miniaturized and made lighter. Strain sensors are used to measure and evaluate the deformation of materials, as well as to detect body movement, for example, as a data glove, which is a wearable device. Conventional metal strain sensors can detect only small strains of up to 5% and therefore limit body movement.
Sensors made of a composite of an electrically conductive material and a polymer can detect strains of up to 100% but undergo creep deformation at high strain rates. It takes more than 100 s before the deformation becomes stable and strain measurements can be made. The device durability of such strain sensors has barely been studied.
The Nanotube Research Center of AIST has developed the super growth method to synthesize single-walled CNTs with high carbon purity, and it is now developing applications for these types of CNTs. We have succeeded in producing a high-density oriented CNT wafer by densification of long, vertically oriented single-walled CNT films in which the CNT films were laid horizontally on a silicon wafer. Mass fabrication of three-dimensional CNT devices was achieved by using this CNT wafer. We have developed a technique to bond this high-density oriented CNT wafer to a soft substrate at any position and in any direction, making it possible to fabricate soft devices combining CNTs and a stretchable polymer substrate. We have attempted to apply this technique to strain sensors.
Figure 1 illustrates the method used to fabricate the CNT strain sensor. Vertically oriented single-walled CNT films synthesized by linearly patterning the catalyst on a silicon substrate are removed from the substrate, placed on a stretchable polydimethylsiloxane (PDMS, a type of silicone rubber) substrate, and immersed in isopropyl alcohol. Through this process, the oriented single-walled CNTs are densified, laid horizontally, and attached to the substrate by van der Waals forces. The orientation of the CNTs is perpendicular to the direction of strains.
We have also developed a bonding technique of a soft electrode, the properties of which remain unchanged after deformation, using an adhesive made of PDMS and conductive rubber with dispersed CNTs synthesized by the super growth method. One electrode is bonded to each end of the CNT strain sensor. Use of this electrode has made it possible to fabricate a strain sensor in which all of the components are stretchable, including the electrodes. Strain sensors of various sizes can be fabricated. The largest of the sensors fabricated has been 15 x 5 cm.
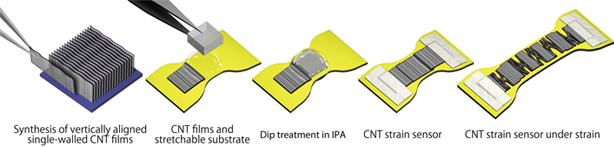 |
Figure 1 : Fabrication method of the CNT strain sensor |
Figure 2 shows the properties of the CNT sensor. All measurements were conducted at room temperature. While a conventional metal strain sensor was able to measure only small strains of up to 5%, the CNT strain sensor was able to measure strains of up to 280% (Fig. 2a). Strain sensors using random-oriented CNTs cannot measure such large strains. On the first application of the strain, the electrical resistance changed with the strain as shown by the red line in Fig. 2b. On the second and subsequent applications, the electrical resistance changed differently as shown by the blue line in Fig. 2b. This curve has two linear sections with different slopes. The sensor was durable for more than 10,000 repeated applications of strains of up to 150% and showed a creep of only about 3% for the rapid application of a 100% strain. The creep became stable in 5 s. This strain sensor is less prone to creep and faster in creep recovery than sensors made of a composite of an electrically conductive material and a polymer; such sensors can measure strains of up to only 100% (literature data: 8.8% creep, creep recovery time of more than 100 s). It responds very quickly to strain with a delay of only 14 ms.
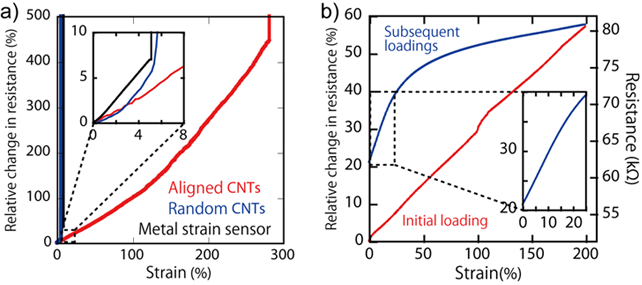 |
Figure 2 : Properties of the CNT strain sensor |
The surface of the CNT sensor was observed under a scanning electron microscope to elucidate the mechanism of the sensor. Before strain was applied, no surface irregularities were observed (Fig. 3a). On the initial application of 100% strain, buckling occurred on the CNT surface, causing cracks in the direction perpendicular to the direction of the strain (i.e. in the direction of the CNTs) (Fig. 3b and e). On the second and subsequent applications of the strain, the cracks closed when the strain was removed (Fig. 3c). When the strain was applied again, the cracks that were initially generated opened again (Fig. 3d). The opening and closing of the cracks indicates that the CNTs follow the movement of the stretchable substrate. Detailed scanning electron microscopy (Fig. 3d) of the crack surface of the CNTs showed that the cracks were bridged by CNTs (Fig. 3f) and conductive paths were provided by the bridges.
We introduced a CNT-bridge model (Fig. 3g) for this mechanism and calculated the change in electrical resistance. The calculated results agreed well with the measured data shown by the blue line in Fig. 2b.
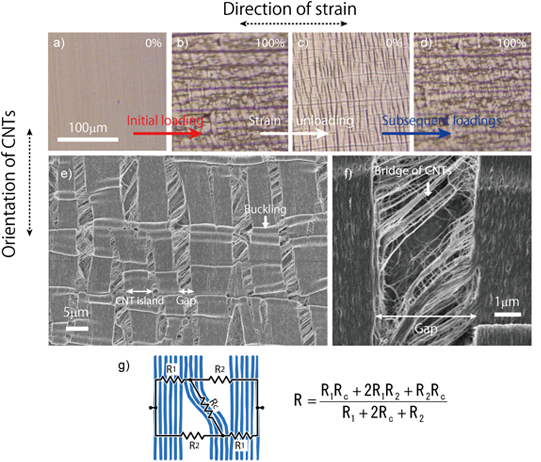 |
Figure 3 : Stretching mechanism of the CNT strain sensor and a model of the change in electrical resistance |
As an application of the CNT strain sensor, we fabricated prototypes to monitor breathing, voice production, and hand and foot movement. Figure 4 shows the measurement results. In a measurement using tights to monitor knee movement (Fig. 4a), strain was applied to the sensor when the knee was bent, and the electrical resistance increased. When the knee was straightened, the strain was removed and the electrical resistance decreased. The sensor detected the change in electrical resistance with the change in knee movement (Fig. 4b). It also detected quick bending and straightening movement of the knees in jumping off the ground and knee movement in absorbing shock on landing. CNT sensors were attached to each finger of a glove (Fig. 4c). When each finger was moved, its shape was identified by the sensor signal, demonstrating that the sensor can be applied to a data glove (Fig. 4d). As the CNT strain sensor is a highly durable device, the tights and the glove can be used repeatedly by multiple users.
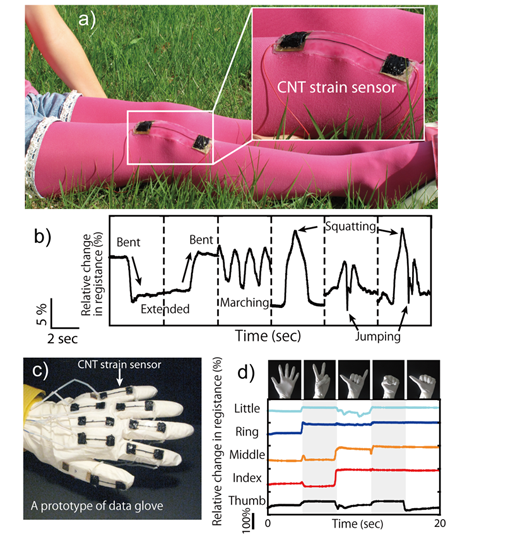 |
Figure 4 : Monitoring knee and finger movement by using the CNT strain sensors |
The developed CNT strain sensor can be used to measure quick, large movement of human bodies and can be applied to wearable devices. For example, it can be used for medical applications, such as monitoring of rehabilitation activities without interfering with patient movement, monitoring of patient breathing, and data gloves for telesurgery. The sensor can also be used for recreational applications, for example as an input device for computer games.
We will seek to collaborate with businesses to develop devices for commercial applications.