- The performance of semiconductor manufacturing equipment will be improved and environmental loads and running costs will be reduced -
Harumichi Sato (Senior Researcher) of the Integration Process Technology Group (Leader: Jun Akedo), the Advanced Manufacturing Research Institute (AMRI; Director: Norimitsu Murayama) of the National Institute of Advanced Industrial Science and Technology (AIST; President: Tamotsu Nomakuchi), and Jun Akedo (Prime Senior Researcher) of AMRI, AIST, in collaboration with Atsuden Co., Ltd. (Atsuden; President: Eiichi Murakami) and Tokyo Keiso Co., Ltd. (Tokyo Keiso; President: Tokio Sugi), have developed an ultrasonic flowmeter that can accurately measure micro-flow rates of less than 10 mL/min (error: ±0.1 mL/min).
In developing the flowmeter, we examined the fundamental theory of ultrasonic wave (guided wave) propagation, increased the frequency of ultrasonic waves, and optimized the design of the ultrasonic flowmeter. This ultrasonic flowmeter can measure flow rates in the micro-flow rate range; this has not been possible with conventional ultrasonic flowmeters. It allows highly accurate control of the liquid chemicals used in semiconductor manufacturing equipment and is expected to contribute to the increased performance, reduced environmental load, and reduced running costs of semiconductor manufacturing equipment.
Details of this technology will be presented at INTERMEASURE 2010 (the 24th International Measurement, Test and Control Technology Show) from November 24 to 26, 2010, at Tokyo Big Sight and at SEMICON Japan 2010 from December 1 to 3, 2010, at Makuhari Messe, Chiba.
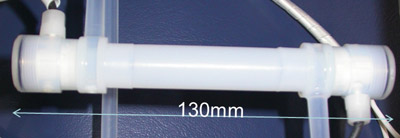 |
(Photo) Prototype micro-flow ultrasonic flowmeter |
PFA ultrasonic flowmeters, which have good chemical resistance, allow non-contact measurement of the flow rates of liquids, and transmit measured rates as electrical signals, are used in semiconductor manufacturing equipment. In recent years, ultrasonic flowmeters that can measure low flow rates are required because semiconductor circuits are miniaturized and reduced resource consumption is demanded. There is demand for flowmeters for non-contact measurement of micro-flow rates, not only in the semiconductor industry but also in the pharmaceutical industry. There is therefore a social need for these devices.
Ultrasonic flowmeters have been developed to measure the flow rates of liquids in hard pipes with large inner diameters, such as pipelines. Ultrasonic flowmeters for the measurement of micro-flow rates have been developed as an extension of this application, but they have not been able to meet the market needs for increased accuracy and stability.
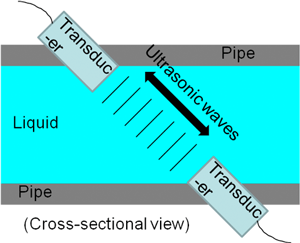 |
Figure 1 : Example of an ultrasonic flowmeter |
AIST has been engaged in the theoretical analysis and device development of ultrasonic measurement technology and ultrasonic actuators. To realize minimal manufacturing, AIST is also working to help the manufacturing industry and small-to-medium-sized manufacturers supporting the industry to solve problems responding to their requests. Atsuden and Tokyo Keiso develop, manufacture, market, and maintain ultrasonic flowmeters. In FY2005, AIST, Atsuden, and Tokyo Keiso began research and development of a micro-flow ultrasonic flowmeter.
Existing ultrasonic flowmeters have been designed on the basis of the assumption that longitudinal waves travel mainly through the fluid in a pipe, without much consideration for the frequency of the waves. However, the propagation characteristics of ultrasonic waves traveling through a medium with boundaries should be analyzed under the given boundary conditions. We planned to perform a detailed theoretical analysis of ultrasonic wave propagation in an ultrasonic flowmeter including a pipe and to design an ultrasonic flowmeter based on the results of the analysis.
A part of this study was supported by a FY2009 Industrial Technology Development Grant (Research & development project for supporting small and medium enterprises) from the Ministry of Economy, Trade, and Industry, Japan.
Figure 2 is a schematic of the ultrasonic flowmeter and the principle of flow rate measurement. Ultrasonic waves are generated and received by the ultrasonic transducer (transmitter/receiver). The flow rate is determined by measuring the difference in propagation time. More specifically, the flow velocity of the fluid (ν) is calculated from the difference in propagation time (Δν) between a downstream wave and an upstream wave, and from the propagation velocity at a flow velocity of 0 m/s (νg) and distance (L) traveled by the wave. Then, the flow rate (Q = Sν) is calculated from the flow velocity and the cross-sectional area (S) of the flow path (inside the pipe). In theory, with decreasing inner diameter of the pipe, the pipe's cross-sectional area decreases and, as a result, the flow velocity (ν = Q/S) increases, enabling measurement of lower flow rates. For example, if the inner diameter is reduced to a half, the cross-sectional area decreases to a quarter and the flow velocity increases by four times, increasing the sensitivity of flow velocity measurement by four times. However, with a smaller cross-sectional area, the amount of ultrasonic waves traveling through the liquid decreases, resulting in a decrease in the intensity of the received signal. Pipe diameter has been reduced to measure micro-flow rates. However, the pipe size reduction has reached its limit because of a decrease in signal intensity.
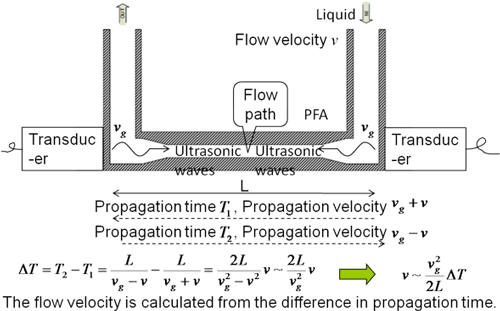 |
Figure 2 : Schematic of the ultrasonic flowmeter and the principle of flow velocity measurement |
A more accurate analysis of ultrasonic waves traveling through a flow path was performed by using a realistic device structure to investigate the cause of the limit of pipe size reduction and to find a solution. Figure 3 shows a model for the analysis of the ultrasonic flowmeter. While traveling through the pipe and the liquid, the ultrasonic waves generated by the ultrasonic transducers are affected by the boundaries. We have developed a program to calculate propagation velocities and displacement distribution by solving wave equations that describe the ultrasonic wave propagation in a way that meets the appropriate boundary conditions. The propagation velocities of guided waves traveling through a 16-mm (outer diameter) x 2.5-mm (inner diameter) PFA pipe filled with water were analyzed with this program (Figs. 4 and 5).
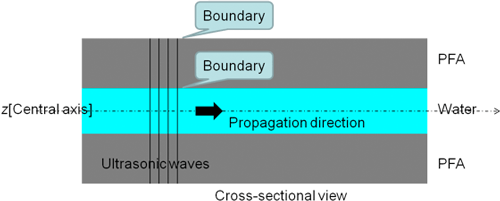 |
Figure 3 : Model for the analysis of an ultrasonic flowmeter |
With 2-MHz ultrasonic waves, only waves of modes with propagation velocities slower than the sound velocity of the longitudinal wave in PFA (1230 m/s) exist (Fig. 4). This result shows that waves of modes by which the change in flow velocity of the fluid can be measured travel slower than the sound velocity of the longitudinal wave in PFA. In addition (Fig. 4, right), waves of various modes exist in a narrow velocity range, causing the overlap of waves and making it difficult to separate waves (the S/N ratio decreases). Therefore, we have concluded that 2-MHz ultrasonic waves cannot be used to measure flow rate in a flow path of this shape.
On the other hand, with 3.8-MHz ultrasonic waves, there is a mode with propagation velocity higher than the sound velocity of the longitudinal wave in PFA and the displacement of this mode in the direction of water flow (the longitudinal component) is dominant (Fig. 5). This mode is close to a longitudinal wave traveling through the fluid, allowing measurement of the flow velocity. In addition, as the sound velocity of this mode is different from those of other modes, the other modes hardly interfere, and thus the mode is advantageous in achieving a high S/N ratio. From the above, we concluded that the use of high-frequency ultrasonic waves (frequency optimization) improves the accuracy of flowmeters. This conclusion defies the belief that high-frequency waves are attenuated quickly and cannot be used for practical applications.
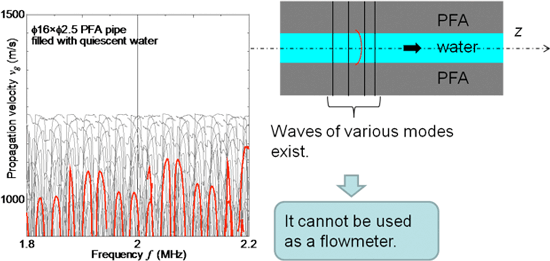 |
Figure 4 : Propagation velocities of ultrasonic waves near 2 MHz |
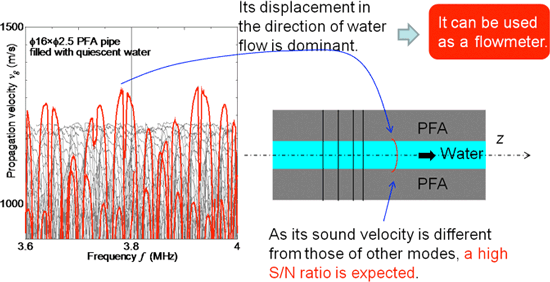 |
Figure 5 : Propagation velocities of ultrasonic waves near 3.8 MHz |
On the basis of these analyses, we designed, test-produced, and tested an ultrasonic flowmeter. Figure 6 shows the measurement accuracies of the new flowmeter and two types of conventional flowmeter. The dashed and dotted line above the target area shows the target accuracy of the new flowmeter.
The accuracy of conventional flowmeter A (Model A) is ±1% at 100 mL/min but drops rapidly at lower flow rates. Conventional flowmeter B (Model B) is less accurate than flowmeter A at 100 mL/min but can measure lower flow rates. However, its accuracy is ±4.5% at 10 mL/min and drops rapidly at lower flow rates.
The prototype flowmeter was confirmed to have an accuracy of ±1% in a wide range from 10 to 800 mL/min and was able to measure a micro-flow rate of 1 mL/min with an accuracy of ±10%. This means that the new ultrasonic flowmeter is applicable to micro-flow rate measurement, which is not possible with conventional ultrasonic flowmeters for semiconductor manufacturing equipment.
The reduction of a pipe inner diameter 0.625 times that of conventional flowmeters, i.e. 0.4 times in the cross-sectional area of the flow path, and the frequency increased by a factor of 1.9 made such a measurement of micro-flow rate possible (the performance is expected to be improved by about 500%). Another possible factor is that the stability of the flowmeter was improved because of optimization of the frequency of the ultrasonic waves.
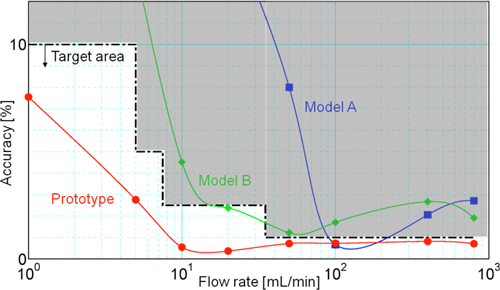 |
Figure 6 : Accuracy of flow rate measurement |
The new ultrasonic flowmeter is expected to contribute to minimal manufacturing by improving the accuracy of feedstock control. We plan to apply this technology to pharmaceutical and biochemical manufacturing. Atsuden founded Ryu SOK Co., Ltd. on October 29, 2010, at the free trade area in Uruma City, Okinawa Prefecture, to mass-produce the flowmeter. Tokyo Keiso plans to commercialize the flowmeter next year.