- Realized by using high-pressure and high-temperature water in a microreaction system -
Hajime Kawanami (Senior Research Scientist), the Compact System Engineering Team (Leader: Akira Suzuki), the Research Center for Compact Chemical Process (Director: Fujio Mizukami) of National Institute of Advanced Industrial Science and Technology (AIST) (President: Tamotsu Nomakuchi) and Keiichiro Matsushima (Researcher), Environmental Systems Section, Environment and Energy Department of Hokkaido Industrial Research Institute (Director: Masaru Otani) jointly developed a new facile and continuous production method of 5-hydroxymethylfurfural (HMF) from inexpensive saccharides such as glucose, in high-pressure and high-temperature water medium. The process is very fast; within 10 seconds of reaction time, high yield and high selectivity of HMF synthesis were achieved. HMF is expected to be effective in preventing diseases like metabolic syndrome, hypertension and diabetes.
This method was achieved by using the newly developed high-pressure and high-temperature microreaction system. The system enables rapid heating from room temperature to 400°C within a very short time (less than 0.01s) by mixing high-pressure and high-temperature water and an aqueous solution of saccharide in a microreactor (micromixer). The system can also cool the solution to 25°C within a very short time.
HMF is a promising compound as a food additive and a pharmaceutical for improving blood pressure on metabolic syndrome, hypertension and diabetes as life-style related diseases. However, conventional production methods are inefficient for mass synthesis of HMF from glucose or other saccharides. As the production methods are also complex, HMF cannot be provided in an industrial scale, and is always expensive.
The newly developed method is promising to produce the highly valuable HMF cost-effectively in large scale, leading to the decrease in the product cost in comparison with other conventional methods. So, this method can offer the affordable price for HMF, prevent life-style related diseases, and contribute to the healthy life.
Details of this technique will be presented in CPhI JAPAN 2009, held at Tokyo BIG SIGHT on April 21 to 23, 2009.
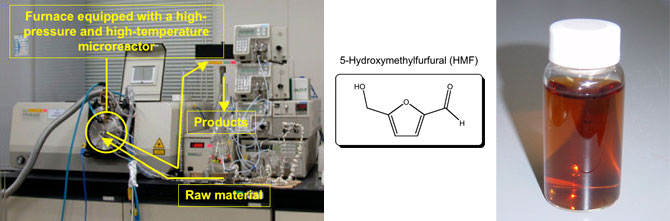 |
Photo (left) : Production equipment for HMF. Photo (right) : HMF aqueous solution (not purified) |
HMF has long been known as a substance contained in foods such as honey, but it has been regarded as an impurity and has not attracted attention. After publishing of recent reports about the effects of HMF on life-style related diseases such as metabolic syndrome, hypertension and diabetes, it suddenly began attracting more attention. And now, it is used as a silver bullet for sickle cell anemia in the U.S.A., (approved by the FDA in February 2007). Furthermore, if HMF can be economically synthesized from glucose and other saccharides derived from biomass, HMF would be used in a wide range of application such as raw materials for plastics and various organic compounds as an alternative to petroleum.
However, the application of HMF is limited because of high production cost. Low efficiency in synthesis and high solubility in water cause complexity and difficulties in HMF mass production processes including purification. Therefore, HMF currently is too expensive to be used as a pharmaceutical or a food additive for daily ingestion in spite of the fact that it is expected to have good bioactivity and an improving/preventing effect on life-style related diseases.
AIST has been conducting research and development of compact, environment-friendly chemical processes for organic compound syntheses and various material productions using water at wide-ranging temperature (room temperature to 600 °C) and pressure (atmospheric pressure to 300 MPa) including organic syntheses in supercritical water. At the Research Center for Compact Chemical Process, chemical processes under wide-ranging temperature and pressure and in situ spectroscopic measurements of basic properties of materials in high temperature and pressure water have been developed over the years. We have also accumulated expertise in production methods for various materials based on these high-pressure and high-temperature water technologies. By using these technologies, we have developed the new effective technology for conversion of many kinds of saccharides derived from botanical biomass into the alternative materials to petroleum. In this research, we focused on HMF, which is a by-product from the production of substitutes for petroleum, but may have various bioactive properties, and we have been developing an environment-friendly production method, using water as a solvent, in which HMF is synthesized at high yield and high selectivity.
Using a high-temperature, high-pressure microreactors, we achieved quick heating from room temperature (25°C) to high temperature (400°C) within 0.01s by mixing of high-temperature, high-pressure water and aqueous solution of saccharides, and also quick cooling by a similar method. Figure 1 shows a schematic diagram of the high-pressure and high-temperature microreactor.
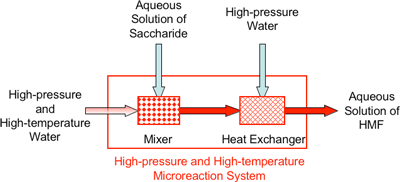 |
Figure 1 Schematic diagram of high-pressure and high-temperature microreactor (actual size is approximately 10 cm × 15 cm) |
By using this high-pressure and high-temperature microreactor, the rapid heating and cooling within 0.01s can be achieved and the precise control of the reaction time at mille second level are realized under high-pressure and high-temperature conditions. This development leads great reduction in side reactions, over reactions, product decompositions, etc. As a result, it became possible for the first time to continuously produce HMF with a higher yield than 70% (calculated based on the raw material) and with a high selectivity exceeding 80%. Moreover, reaction time was 10 seconds, and thermal decomposition was not significant because the products were immediately cooled in the continuous reaction.
In the conventional batch processes, heating or cooling between room temperature and the desired high temperature (e.g. 400 °C) takes at least 30 seconds, resulting in the occurrence of side reactions during heating or cooling (the blue curve in Fig. 2 indicates the change in the reaction temperature with time in the conventional batch method). In a previously reported method, HMF synthesis from glucose needs two or more reaction steps; its yield and selectivity were as low as several tens of percent. To improve these yields of HMF syntheses, specific organic solvents such as ionic liquid or harmful organometallic complex catalyst such as chromium one were developed. However, the sophisticated purification of HMF is necessary. Therefore, it has been extremely difficult to develop a industrial production process of HMF.
We have developed an environment-friendly production process, using water without any organic solvents, in which HMF is easily and simply synthesized in a one-step process at high yield and high selectivity and the obtained HMF can be used in food and beverage as it is without further purification, although it is slightly colored due to impurities.
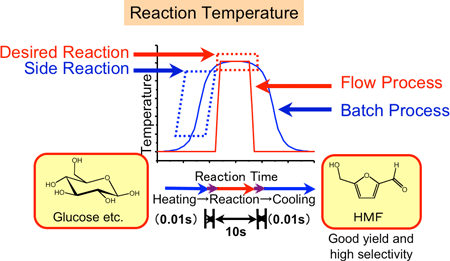 |
Figure 2 Time dependence of reaction temperatures in the high-pressure and high-temperature microreaction system (red) and in the conventional reaction system (blue)
|
By achieving this rapid heating and cooling technology, it is possible to avoid side reactions. In the batch processes many side reactions can be occurred during slow heating and cooling. Our new method is a continuous reaction process using the microreactor, and products are cooled immediately after the reaction and are not significantly decomposed by the heat.
For the utilization of the newly developed reaction system for HMF synthesis at various factories even at small ones, we intend to develop a compact bench scale reaction system with further energy- and cost-saving. For that, we are going to invite businesses to collaborate with us in the development.