- Contributing to the compact, high-performance, and long-lived electronics products -
Kazuhiko Sato, Group leader, of the Organic Reaction Control Group of the Research Institute for Innovation in Sustainable Chemistry (Hiromichi Shimada, Director) of the National Institute for Advanced Industrial Science and Technology (AIST; Hiroyuki Yoshikawa, President), jointly with Showa Denko Group (Kyohei Takahashi, President and CEO) have developed an innovative insulating coating resin which can contribute to the production of compact, high insulation performing, and long-lived electronic parts.
Insulating coating resin has been used as a coating material for various electronic parts and wirings of large liquid crystal displays, mobile phones, etc. Conventional production technologies for resin need chlorine compounds. However, long-term use of resin generates hydrogen chloride which causes short-circuit, leading to a reduction in electric insulation performance of fine wirings. However, when the heat-resistance of the resin is enhanced to overcome this problem, its flexibility is reduced, which has been the bottleneck for the production of devices with arbitrary shapes.
In this work, we have established a technique for the production of insulating coating resin with a clean oxidation method which uses hydrogen peroxide and does not use chlorine compounds. We have thereby succeeded in the development of an innovative insulating coating resin with both insulation stability over a term which is twice a long as the conventional one and high flexibility by combining with a newly developed hardner. Our technique does not discharge contaminants, and thus is environment-friendly.
This resin can respond to printed circuit boards becoming more flexible and wirings becoming thinner in the future, and thus we expect that the resin will be a fundamental material supporting the next-generation electronics society. Prior to the mass-production of this resin, we will begin to supply samples to users from 2007.
Part of the details of this work will be presented at the 39th Symposium on Chemical and Biochemical Oxidation held at AIST in November 6-7, 2007, and at the 15th Polymeric Materials Forum held at the Senri Life Science Center in November 16-17, 2007.
 |
Photograph: An example of the application of the insulating coating resin we have developed.
Copper wirings on a polyimide film are covered with our insulating coating resin (green color). The film is curled to stress the flexibility of the resin. |
Because of the wide use of the internet, highly functional enhancement of mobile phones and the beginning of ground-based digital broadcasting, functional upgrade and weight-saving of electronic parts have been greatly required. In practice, enhancement of the flexibility of printed circuit boards and the fabrication of thinner wirings have advanced. As a result, high performance for the insulating coating resin to protect the electric circuits has also been desired. Epoxy resin is usually used as starting material for insulating coating resin, and chlorine compounds remaining in the epoxy resin have caused a serious problem from the viewpoint of long-term insulation characteristics. Until now, chlorine compounds from hydrolysis, which remains as impurities, has been of the problem, but besides that another problem has occurred whereby chlorine from organic chloride in the resin causes dehydrochlorination after long-term use of the resin, and thereby short circuits occur. Enhancement of heat-resistance performance of the resin is one method to overcome the problem, but it reduces the flexibility of the material, resulting in an obstacle to the fabrication of small and light electronic parts. Thus, it has been difficult for resin to satisfy requirements for both flexibility and long-term insulation stability.
Furthermore, epoxy resin is usually produced using epichlorohydrin as the starting material. In the process of epoxy synthesis, a large amount of sodium chloride and calcium chloride are produced as byproducts, and their treatment as waste becomes troublesome. In addition, the removal of residual chlorine for the improvement of their electric insulation characteristics requires a very high purification cost.
From these circumstances, AIST, jointly with Showa Denko Group, has advanced the development of high-performance materials on the basis of the epoxidation developed by AIST, which is able to respond to the needs of leading-edge electronics, and has also carried out an investigation into the reduction in the environment load without harmful chemical materials and by the minimization of waste products.
This research work was carried out in support of the "Basic Technology Research for Risk Reduction in Harmful Chemical Substances (in FY 2004-2006)" contract project of the New Energy and Industrial Technology Development Organization (NEDO).
We have investigated the production method of bifunctional epoxy monomers with selective epoxidation by hydrogen peroxide using diolefin compounds designed for electronic materials as starting materials. Hydrogen peroxide is a clean oxidizing agent which does not produce any byproducts except for water, but its oxidative power is weak, and thus to use it for reactions, activation with a catalyst is essential. In this work, we have developed a new catalyst system with high activity and high selectivity, and thereby succeeded in selective epoxidation (Figure 1).
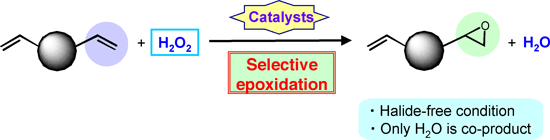 |
Figure 1. Selective epoxidation using hydrogen peroxide |
As shown in Figure 2, the bifunctional epoxy monomers were oligomerized, and additionally developed a hardner which is most suitable to react with the epoxy groups, leading to the successful development of a high performance resin.
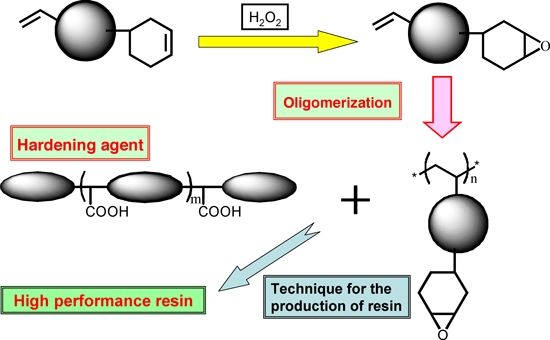 |
Figure 2. Outline of the technique we have developed
|
As shown in Figure 3, we have confirmed that our insulating coating resin exhibits high insulation performance when used in practice.
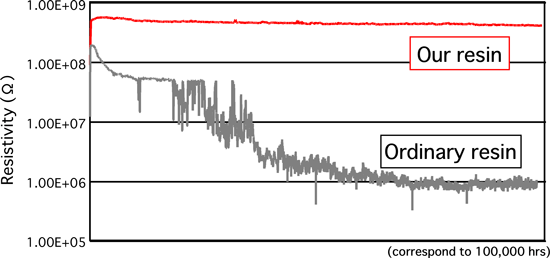 |
Figure 3. Result of a long-term insulation performance test |
Our technique has high degree of variety for the molecular design of the epoxy compounds and hardners, and can thus respond to the various needs of users by balancing insulating performance and flexibility. Also, as the hardner developed has high optical-performance, thermosetting optical films can be formed by combining with flexibility or our fundamental concept for the development of resin, which is also expected to apply to liquid crystal display films.
We plan to first apply the high-performance insulating coating resin developed in this work to specific electronics fields where advanced fine wirings are needed, and after obtaining sufficient successful results, go through other electronic- and optical-material markets. We thus plan to supply resin samples from 2007, with researching user's demand.