- Toward the realization of small-scale fuel cells enabling quick startup and shutdown operation -
Toshiaki Yamaguchi (Researcher) of the Functional Assembly Technology Group, the Advanced Manufacturing Research Institute (Hideto Midome, Director), the National Institute of Advanced Industrial Science and Technology (AIST; Hiroyuki Yoshikawa, President) jointly with the Fine Ceramics Research Association and NGK Insulators, Ltd. (Shun Matsushita, CEO), have succeeded in the establishment of fabrication techniques of honeycomb-type micro solid oxide fuel cells (SOFCs) which realize high power output even at low temperatures around 600°C.
SOFCs have features of high efficiency, high reliability, and easy handling, but they have until now been used only for applications which need continuous operation at temperatures higher than 800°C. Thus, to expand their applications, the addition of functions such as low temperature operation and quick start and stop, and the small-scale fabrication of power-generation modules have been desired.
The honeycomb-type micro solid oxide fuel cells (SOFCs) developed in this work can respond to quick start operation within a few minutes from room temperature, and thus it is expected to realize small SOFC system which is applicable to auxiliary batteries for cars, small cogenerators, and portable power sources.
Our research work was carried out in the "The Advanced Ceramic Reactor" project supported by the New Energy and Industrial Technology Development Organization (NEDO), and the results will be presented at the "Cocoa beach Conference" held in Florida, U.S.A on January 22, 2007.
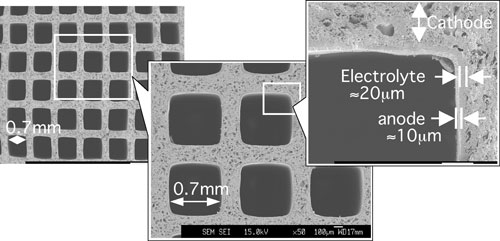 |
Photograph: Overview of a honeycomb-type cathode supported SOFC (cathode: perovskite-type manganate (LSM)) and its magnified view of 3-layered structure region |
Fuel cells have attracted attention for high energy conversion efficiency applicable to on-demand power generation systems. However, until now, SOFCs have been applied only to heavy power systems which need to be continuously operated at high temperatures of 800-1000°C due to the properties of materials used for cells, components and stacking structures. For applications to home and automobile use, it is necessary to develop small and highly-efficient SOFCs with a power level of several kW with quick start and stop performance. Thus, it has been expected to establish fabrication technologies for miniaturizing power generation modules with high output energy density.
Honeycomb structured ceramics have been used support substrates of catalysts for the clean-up of exhaust-gas from cars etc., because they have larger area for gaseous reactions, and are structurally stable. If layered structure of fuel cell is constructed on the wall of each regularly arranged channel in the ceramic honeycombs, high cell-packing density SOFC modules can be realized. It is significant to utilize such a ceramic honeycomb as an electrode support for cells-accumulation by developing coating processes of dense electrolyte layer on the inner wall of porous honeycomb substrate.
To solve these technical problems, we have developed precise slurry injection techniques for forming layers of various electrolytes and electrodes on the inner surface (wall) of the channels in the porous honeycomb substrates that are made of perovskite-type manganate (LSM).
We have produced a honeycomb support with a size of 15 x 15 mm of a perovskite-type manganate material (LSM) using extrusion molding, as shown on the left of Figure 1. Using a slurry of scandia-stabilized zirconia (ScSZ) or ceria based oxides (GDC, etc.), we have coated on the surface of 256 sub-millimeter square channels all together using a special jig, and heated at 1300°C after drying. Then, we have coated again with a nickel slurry including ceria based oxide (50 vol % Ni-GDC), followed by heating process at a temperature higher than 1100°C. As a result, a dense electrolyte thin layer of 20 µm thick and a NiO-GDC layer as an electrode were formed on the surface of each channel in the LSM honeycomb support. Quick few-minute cooling tests were carried out with the honeycomb SOFCs, and no destruction in the cell structure was observed.
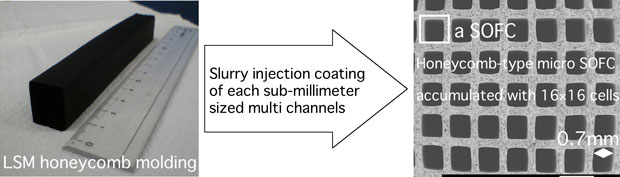 |
Figure 1. As-extruded LSM honeycomb molding (left) and a magnified view of honeycomb type micro SOFC (right) |
Next, we have carried out a power generation test of cells produced using the same coating techniques. Using humidified hydrogen gas, we thereby verified a power generation performance of 0.23 W/cm2 (700°C) which corresponds to the world's highest level in the middle temperature range for cathode supported SOFC, thus it was indicated that our method is useful for the fabrication of small and high-density SOFCs.
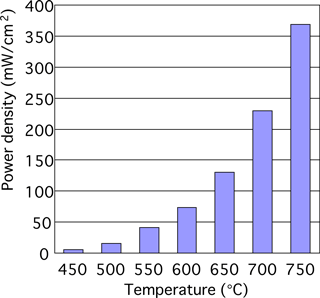 |
Figure 2. Temperature dependence of cell output power density
|
Currently, we plan to investigate the fabrication processes for the enhancement of power-generation performance of the cell-accumulating unit, and also investigate the fluid diffusion and thermal distribution of the honeycomb-type SOFC.