Update(MM/DD/YYYY):08/01/2006
Development of a Pipe-type Module for a Power Generating Heat Exchanger
- Thermoelectric module for simultaneous generation of superheated steam and electricity -
Key Points
-
A thermoelectric-power-generating module allows simultaneous generation of electricity and superheated steam, which results in efficient use of thermal energy.
-
The module contributes to the improvement of the durability of heat exchange systems and to the cleanliness of the exhaust gases.
-
The module guarantees the safety of home appliances using superheated steam at temperatures over 100 ºC, such as cooking stoves.
Synopsis
Ryoji Funahashi et al. of the Synthetic Nano-Function Materials Group (Yo Shimizu, Group Leader) of the Nanotechnology Research Institute (Director, Hiroshi Yokohama), the National Institute of Advanced Industrial Science and Technology (AIST; Hiroyuki Yoshikawa, President), have developed a pipe-type thermoelectric module for use in heat exchangers that can simultaneously generate steam superheated above 100ºC and electricity from the combustion of fuel gas in water heaters and cooking stoves.
Thermoelectric ceramics, which are stable even in extremely hot air, are used to cover stainless steel tubes in electricity generating modules. This cover prevents the contact between the stainless steel tube that acts as a heat exchanger and the flame, protecting the metal tube and extending the useful life of the heat exchanger. In addition, control of the flame temperature may help suppress the formation of harmful substances, such as nitrogen oxide (NOx) or carbon monoxide (CO), which are products of incomplete combustion. On top of that, electric power can be obtained from the module. In other words, the pipe-type module developed in the present research makes it possible to utilize the high temperature energy generated by the flame, which had not been used.
So far, one module with a length of 30 cm has been installed in a water heater of main-stop type. Gas combustion simultaneously generated, 1.3 to 1.5 V, 0.28 W of electric power and steam.
By using this thermoelectric module for direct heat conversion in gas equipment, it is possible not only to improve the safety of gas equipment but also to achieve efficient use of superheated steam in domestic appliances, such as cooking stoves or mist saunas. Details of the present research will be discussed at the 11th Symposium on Power and Energy Technologies of the Japan Society of Mechanical Engineers, to be held at Tokyo University of Marine Science and Technology from June 29th.
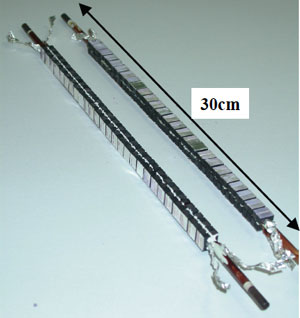 |
Photo: Appearance of the pipe-type module developed
|
Background of the Research
Recently the use of superheated steam at home has been increasing. Development of small-sized steam generators leads the development of electrical equipment, but when energy efficiency and instantaneous power generation are considered, it is evident that fuel gas has a quicker response and produces larger amounts of steam, which makes gas based systems more attractive. However, in fuel gas systems, the deterioration of the surface of the stainless steel tubes that act as heat exchangers by continuous exposure to heat, as well as the decrease of the flame temperature translates into an increase in the production of carbon monoxide (CO) (Figure 1 (a)). It then becomes necessary to develop a safe and secure fuel gas system that solves this problem.
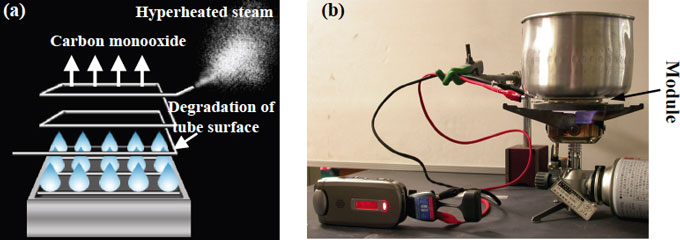 |
Figure 1 Problems during generation of superheated steam produced by fuel gas (a), and thermoelectric generator using a small-size gas burner (b)
|
History of the Research
Working towards the establishment of a sustainable developing society, AIST has devoted resources to research on ceramic thermoelectric generators, which are expected to contribute to the recovery of energy from waste heat, and to the solution of environmental problems. To the present, AIST has succeeded in the independent development of thermoelectric ceramic materials (metal oxides) that allow generation of electricity from combustion of gas, as well as of electricity generating modules that use these materials (Figure 1 (b)).
Research on thermoelectric systems made of ceramic materials started in 1998 at AIST. Among the achieved results there is the discovery of p-type layered cobalt-based thermoelectric oxide with 10% conversion efficiency at temperatures higher than 600°C and 500°C of operational temperature difference, and the establishment of technologies for synthesis and characterization of 2,000 different thermoelectric materials per day. Now, looking for practical applications for the developed technologies, AIST has joined forces with the Energy Technology Research Institute of the Osaka Gas Co., Ltd., which has a high level of technology in combustion and transmission of heat, to evaluate the possibility of solving the problems related to steam generating equipment through the use of thermoelectric ceramics, resulting in the development of the present module.
Until now, the modules produced at AIST were all plate shaped modules (Figure 2), but it became apparent that this shape is not always easy to use. For example, the surface of the heat source is not always flat, or a large-scale cooling system is necessary. The purpose of the present research was to develop a module that can generate electricity and superheated steam simultaneously inside the flame of the fuel gas. Because of this, it was necessary to start the research from the design of a new module shape.
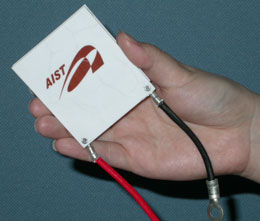 |
Figure 2 Conventional plate-type thermoelectric modules developed by AIST
|
Description of the Research
The objective of the present research was to develop a power-generating module that can transform directly it cooling water into superheated steam during introduction into the system with temperature difference purposes, and which uses the flame of natural fuel gas as a heat source. The material must present not only excellent power generating properties, but also have high resistance to flames as well as heat exchange properties. To this end, we tackled the construction of a module made of pipes to be installed directly to the heat exchange section.
To solve new and challenging problems, technologies incorporated into the development of the plate shaped module were applied for manufacturing of the ceramic elements (Figure 3(a)), electrode conformation to the curved surface (Figure 3(b)), electric insulation between the stainless steel pipes and the thermoelectric element, as well as preservation of the high heat exchange properties, resulting in the development of a pipe-type module. This module measures 30 cm in length (length of the thermoelectric element, 21 cm), and it is composed of half-timber bars with a cross section of 8 mm square; one pipe-type module consists of 54 pairs of p-n elements.
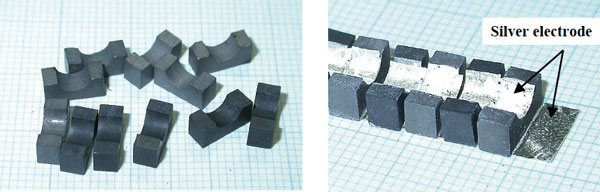 |
Figure 3 Formed thermoelectric elements (a) and elements attached with Ag electrodes (b)
|
This pipe-type module was installed to a main-stop type water heater (Figure 4(a)) for supply of hot water. The surface of the module was exposed to a natural fuel gas flame, and a part of the water from the water heater was flowed into the pipes to produce a temperature difference. The temperature reached 1000ºC in the vicinity of the module, and steam was obtained from the end tip of the pipe steam (Figure 4(b)). The heat exchange generated 1.3 to 1.5 V, 0.28 W of electric power (Figure 5).
This time, electricity was generated using a main-stop type water heater, but 16.8 W (90 V) of electric power could be generated under conditions similar to the ones in the present work using an outdoors hot water supply vessel of the type commonly seen in homes (No. 24, with a hot water output of 41.8 kW, and rated power consumption of 46 W) with space to install 60 modules. Development of structures that reduce the internal resistance and improve the transmission capabilities of modules made of thermoelectric ceramics is expected to achieve an output of 800 W.
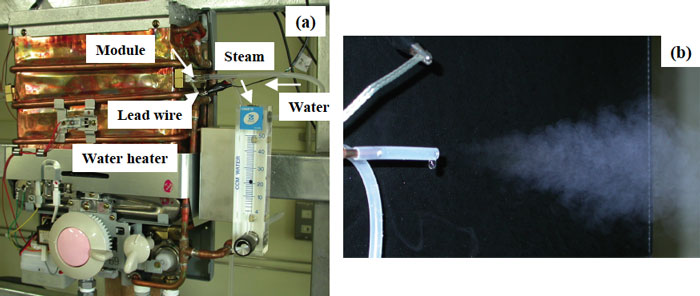 |
Figure 4 Pipe-type thermoelectric module installed onto a main-stop type water heater (a), and steam generation (b)
|
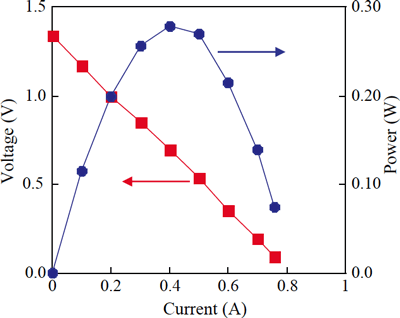 |
Figure 5 Electricity generation characteristics of a one-pipe-type module
|
If such a large amount of electricity can be generated, it will mean the realization of a completely independent steam generator, which does not require connection to an electrical outlet. As the metal tube surface is protected by the ceramic element, the life of the heat exchanger will be lengthened. Also, the electricity generated by the module enables an accurate control of the flame temperature, which will help to suppress the production of harmful substances such as carbon monoxide (CO) and nitrogen oxide (NOx). In this way, not only is the safety of the equipment raised, but effective use of the flame contributes to making our lives more comfortable (Figure 6).
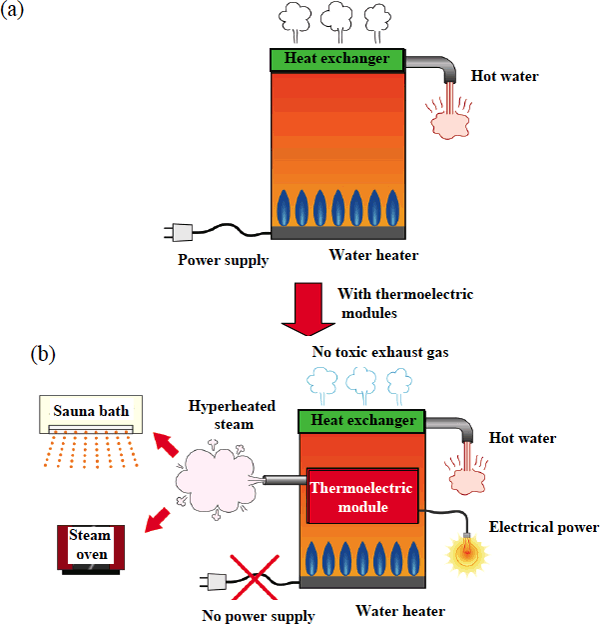 |
Figure 6 An example of energy saving, safe, and comfortable life. Water supply equipment currently in use (a), and water supply equipment with thermoelectric module incorporated (b).
|
Future Prospects
In the future, AIST will join forces with element manufactures. Also, through research under the New Energy and Industrial Technology Development Organization (NEDO) program, we will continue working to increase reliability, electricity generation capabilities, and heat exchange capabilities of pipe-type modules, as well as to develop low cost technologies for applications to fabrication of increasingly practical heat exchangers, and extending their applications beyond gas equipment. In this way we expect to be able to contribute to solving energy related and environmental issues through thermoelectric exchangers.