The National Institute of Advanced Industrial Science and Technology (AIST: Hiroyuki Yoshikawa, President) has succeeded in the continuous synthesis at the laboratory scale of diesel fuel from woody biomass through gasification, purification using activated carbon, and Fischer-Tropsch synthesis.
This new process removes the need for a cooling process, heat recovery, and compression of gas, which makes it attractive for application in compact and portable plants making use of widely available woody biomass.
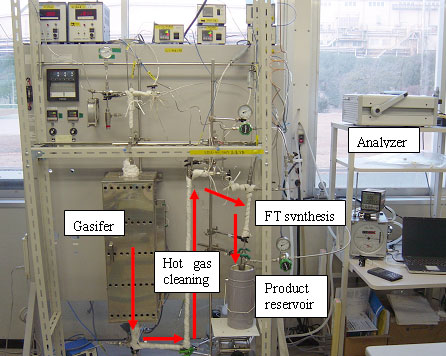 |
Figure: Laboratory scale continuous equipment (bench experimental scale of 1/100, in process amount of 10 g wood/h for 3 hour-operation)
|
To reduce the emission of carbon dioxide, it is imperative to actively promote the use of renewable energy sources such as biomass. The level of carbon fixation by solar energy is especially high in the case of woody biomass, so it is important to find economically sound technologies that allow the use of the highly available biomass composed of unused wood, timber cuts, construction waste, etc.
In addition, liquid fuel from biomass is useful for reduction of SPM (suspended particulate matters) and sulfur oxide, contributing to environmental conservation.
Concerning the synthesis of liquid fuel by way of gasification, liquid fuel production from natural gas containing methane as the main component (GTL) has developed into a promising fuel manufacturing technology. However, it is necessary to further develop the technology in order to match the costs to those for diesel production from petroleum.
In addition, biomass resources such as wood materials are usually found dispersed in mountainous regions and are difficult to collect, raising the production costs. Accordingly, it becomes necessary to design a system for application in compact and portable plants which is available on-site.
The Biomass Technology Research Center (BTRC) was established in October 2005 as a base for biomass research in the AIST. The two main research topics at the BTRC are developments of bio-ethanol production technology centered on saccharification of woody biomass, and of technology for liquid fuel synthesis through gasification. In pursuing these two central research topics, the BTRC aims at developing practical biomass conversion processes that are sufficiently cost efficient to promote the substitution of fossil resources centered around petroleum and to contribute to the establishment of an energy recycling society.
Concerning diesel fuel, the BTRC has tackled research on topics with high potential such as the utilization of clean gas conversion technologies and catalysis technologies.
align="left">The following simple structure has been designed for compact and portable equipment.
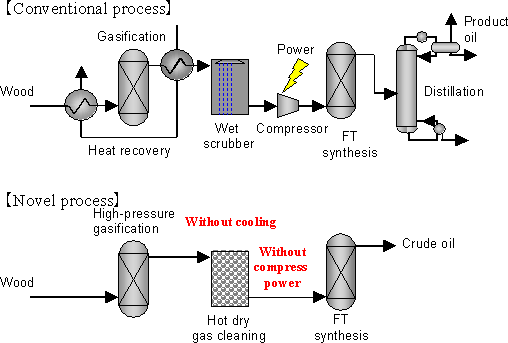
1) Production of synthetic gas (carbon monoxide/hydrogen) by biomass gasification at high temperature (800- 900ºC) and high pressure (several MPa).
2) Hot gas cleaning for removal of tar, sulfur and other minute impurities.
3) Synthesis of liquid fuel from synthetic gas using FT synthesis catalysts.
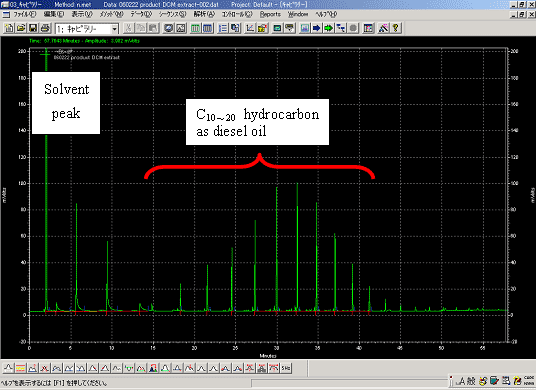 |
Gas chromatography analysis of synthetic hydrocarbon fuel
|
The gasification process is carried out at high temperature (800-900 ºC) and high pressure (several MPa), removing the need for use of compressors or compression power. Gas cleaning is carried out through a dry refining process that uses active carbon, instead of the traditional wet method that utilizes water, increasing the gasification heat efficiency. As a result, it was possible to produce equipment with compact dimensions.
The main features of the equipment are the efficient use of heat which increases the energy efficiency, and the removal of the compression process which reduces the power requirements.