The Advanced Manufacturing Research Institute (AMRI), the National Institute of Advanced Industrial Science and Technology (AIST), an independent administrative institution, has developed new manufacturing process technology for ceramic molding reducing the addition of organic binder by a half from the consumption in the conventional methods, in collaboration with NGK Insulators, Ltd. (to be designated as NGK, hereafter).
The new process is characterized by direct chemical bonding of monomolecular layer of organic binder on the surface of ceramics raw materials particle, and binding together of binder layers through external stimulation (Figure). Fastening raw material particles together through stronger chemical bonding by organic binder is an effective means to reduce the binder consumption in the ceramic manufacturing process.
The results of this study will be presented at the International Ceramics Exhibition to be held at the Tokyo Big-Site from April 5 to 8, 2005.
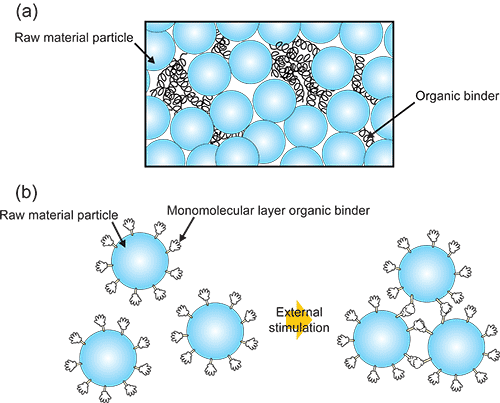 |
Figure (a) Conventional organic binder is to be used as mixed with ceramics raw material particles. Because of weak bond and easy phase separation, a greater amount of organic binder is needed.
(b) Monomolecular layer organic binder is directly fastened to the surface of ceramics raw material particles, which are combined by external stimulation.
|
In order to shape ceramics, it is inevitable to use organic polymer as binder. Organic binder is baked in the sintering process to emit carbon dioxide as decomposition product. For reducing the burden to the environment, it is desired to reduce the consumption of organic binder.
Recently, it has been described that certain calcium aluminate materials can release active oxygen radical under electrical field. These materials are expected to oxidize solid carbon with active oxygen radical, though the decomposition of PM by use of these materials has not yet been reported. The present study has demonstrated that solid carbon can be decomposed continuously by combining an electrochemical ceramic reactor based on oxygen ion conduction by electrical field with oxidizing agent in electrical reaction field.
The AMRI-AIST has been engaged in a grant-providing joint research project with NGK for implementing eco-friendly ceramics manufacturing process. Under this project, efforts have been made for the development of technologies for reducing or eliminating use of organic binder, sintering at lower temperatures, and manufacturing without sintering.
The conventional organic polymer binder has been adsorbed on the surface of raw material particles, with inadequately fastening force between each other. Moreover, because of poor affinity between organic polymer binder and particle surface, phase separation and partial aggregation hamper effective working of binder. For this reason, it has been necessary to add a great amount of organic binder for ensuring good molding and shape-keeping.
In the present study, binding particles together through direct chemical reaction by fastening reactive organic molecules at the surface of ceramic raw material particles in the state of monomolecular layer, and by chemically combining organic binders together in response to outside stimulation, first in the world. Fastening of monomolecular layer organic binder at the surface of raw material particle also prevents phase separation between raw material particles and organic binder. This technology has been realized by upgrading chemical reactivity of particle surface through the improvement of surface processing technology for ceramics raw materials. Photo shows a ceramic specimen prepared by the present process technology and kept in water at the normal temperature for 50 days. The ceramic molding using 0.5 wt % organic binder holds its shape after a long term immersion in water. The technology seems to have contributed to reducing the consumption of organic binder needed for securing good molding and shape-keeping.
(a) Without organic binder
|
(b) With monomolecular layer organic binder (0.5 wt %)
|
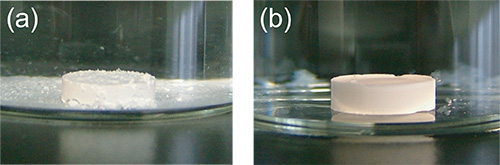 |
Photo. Ceramic specimen kept in water for 50 days. (a) is collapsed in water, while (b) is in good shape. |