Point
We have developed a new heat treatment method for a wrought flame-retardant magnesium alloy. As a result, the alloy processed by the developed method exhibits a higher ductility by approximately 50 % than that of a flame-retardant magnesium alloy processed by the current method, while exhibiting substantially the same tensile strength. In other words, superior balance between strength and ductility has been achieved.
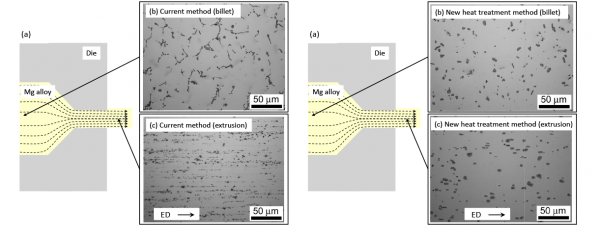
Current method (373 MPa, 11.2 %) New heat treatment method (366 MPa, 16.8%)
Schematic diagrams of extrusion process (a) and micrographs before extrusion (b) and after extrusion (c) |
Background
A flame-retardant magnesium alloy prepared by adding calcium to a general-purpose magnesium alloy (Mg-Al-based alloy) exhibits superior flame-retardant properties, and therefore has started to be used for small cast products mainly for a railway vehicle, which require high flame retardance. Nevertheless, as for wrought magnesium alloys never be applied to structural components in which good balance between strength and ductility is needed, because precipitates in flame-retardant magnesium alloys often become crack nucleation sites.
Outcomes and Methods
The newly-developed method is a new heat treatment method by which shape and hardness of precipitates in flame retardant magnesium alloys become spheroidized and hardened. By using the newly-developed method, we have succeeded in improving the shape and hardness of precipitates, which often become fracture initiation sites. As a result, balance between strength and ductility of wrought (extruded) flame-retardant magnesium alloys has been significantly improved. The flame-retardant magnesium alloy processed by the newly-developed method exhibits 50% higher elongation-to-failure (16.8%) compared with that of the flame-retardant magnesium alloy processed by the current method (11.2%), while it exhibits substantially the same tensile strength of 366 MPa as that of the flame-retardant magnesium alloy processed by the current method. These values are substantially comparable to those of an aluminum alloy (A7N01 alloy, 350 MPa, 15 %) used for products of a high-speed railway vehicle such as the bullet train.
Future Plan
The newly-developed method contributes to significant improvement of the balance between strength and ductility of a wrought flame-retardant magnesium alloy. Utilization of the newly-proposed methods will expand application fields of flame-retardant magnesium alloys to railway vehicle components and architectural components requiring high flame-retardance.