Update(MM/DD/YYYY):12/21/2011
An Oxygen Gas Barrier Film That Self-repairs Minor Damage
- Development of a food packaging film using clay -
Points
-
A transparent film applied with a gas barrier layer composed of clay and plastic
-
Due to flexible and self-repairing properties, it sustains oxygen gas barrier property longer then conventional products in case of being crushed.
-
Promising as a food packaging film because it is easy to make it into a bag and to print letters on its surface
Summary
Takeo Ebina (Leader) and others, Advanced Functional Materials Team, the Research Center for Compact Chemical System (Director: Takamasa Hanaoka) of the National Institute of Advanced Industrial Science and Technology (AIST; President: Tamotsu Nomakuchi), have developed a transparent film with a high oxygen gas barrier property in collaboration with Daiwa Can Company (Daiwa Can; President: Hisakazu Yamaguchi).
AIST has been developing “Claist®,” a film material with clay as the principal constituent, and working to put it to practical use. In the present research, the researchers fabricated a transparent film with a high gas barrier property by applying a mixed paste of a type of hydrophilic clay and a water soluble plastic on a polyethylene telephthalate (PET) film. In addition to the flexibility of the gas barrier layer, this film self-repairs pin holes caused by deformation because it absorbs water vapor in air and swells. Accordingly, the oxygen gas barrier property of the film deteriorates less easily than conventional products when it is damaged.
Moreover, AIST has established the technology to apply the paste quickly onto a film by printing and succeeded in the production of rolls 50 cm in width. The developed film is promising as a food packaging film since forming polypropylene layer on the film made it easy to make the film into a bag and to print the letters on its surface.
The details of this technology will be presented at AIST Open Lab held in Tsukuba, Ibaraki, on October 13 and 14, 2011.
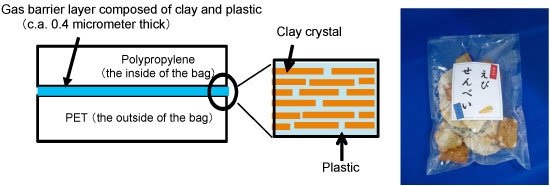 |
Figure 1: A cross section of the developed oxygen gas barrier film (left),
an enlarged view of the gas barrier layer (middle), and a prototype food package (right) |
Social Background of Research
A food package film is required to have a gas barrier property that hinders the permeation of oxygen and water vapor in order to prevent food from deterioration. Currently, the use of the films containing chlorine is avoided due to the dioxin concerns, and the films on which inorganic layer such as silica or alumina are vapor deposited are widely used. The problem is that while these films have oxygen gas barrier and water vapor barrier properties sufficient for food package materials, the gas barrier layer is damaged and their oxygen gas barrier property deteriorates, if they are roughly handled or folded. In addition, the deteriorated oxygen gas barrier property cannot be recovered.
Claist®, a clay film developed by AIST, is expected to be used as a packaging material for food and medicine due to high oxygen gas barrier and water vapor barrier properties and transparency as well as flexibility. However, there have been problems, namely the difficulty in manufacturing it successively as a roll product and the difficulty in handling due to its fragility. In addition, drying after film forming takes a long period of time resulting in a high manufacturing cost. Therefore, it has been difficult to put it to practical use as a food packaging material.
History of Research
AIST has been working to put Claist® to practical use through collaborative research with research institutions such as universities and private enterprises since its development (AIST press release on August 11, 2004). In May, 2010, an AIST consortium, Clayteam, was established to promote industry-academia-government cooperation and accelerate the development of Claist® (AIST press release on September 13, 2010). Daiwa Can aimed at the business of flexible package materials in addition to its container product business. It focused on the clay film technology of AIST and began collaborative research.
In the research, varieties of clay and plastic used for a gas barrier layer, their mixing ratio, coating thickness, coating method and conditions were investigated, a new phenomena, self-repairing of the gas barrier layer, was discovered, and a film for food packaging has been developed.
Details of Research
Combinations of various types of clay and plastics were examined, since the clay films have no particular restrictions on the types of clay and plastic they use. As a result, mixing a type of hydrophilic clay and a water-soluble plastic in certain formula and coating it on a PET film, it was discovered that the PET film and the gas barrier layer adhere very well to each other. This did not change the transparency of the film at all. An oxygen gas barrier property improves by the increase of the thickness of the coated gas barrier layer, however, when it is folded in two, the gas barrier layer is damaged and the oxygen gas barrier property deteriorates. Meantime, when making the gas barrier layer thin, no damage is found by folding it in two but the oxygen barrier property is not enough. Investigating these contradictory characteristics carefully, the researchers determined the appropriate thickness of the gas barrier layer that has enough oxygen gas barrier property and is not damaged when it is folded in two.
In general, the oxygen barrier property of conventional gas barrier films deteriorates when they are roughly handled. However, the developed film has been verified by Gelbo Flex test that its oxygen gas barrier property does not deteriorate easily even if it is compared with not only vacuum-deposited films but also with commercial gas barrier layer coated films (Table 1). It is conceivable that the film swells by absorbing water vapor in air to fill the pin holes produced by deformation. In addition, the flexibility of the coated gas barrier layer contributes to the durability of the film. In fact, it was observed that an intentionally scratched film recovered itself as it was placed in high humidity (Fig. 2). The scratch was still missing when the film was dried again.
Table 1 : Oxygen permeability after Gelbo Flex test (cc/m2·day·atm) |
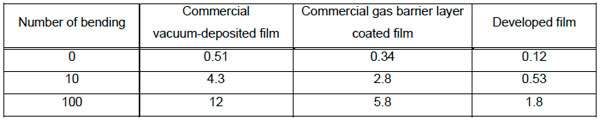 |
Laminates of the film and a 25 µm-thick polypropylene film were measured.
Gelbo Flex test was implemented at 23 °C in relative humidity of 65 %.
Oxygen permeability was measured using gas chromatography at 23 °C in relative humidity of 0 %. |
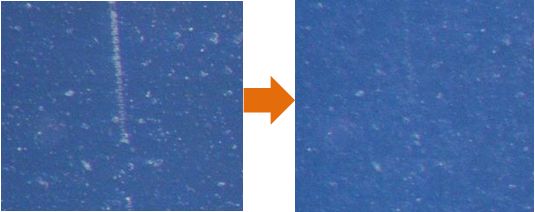 |
Figure 2 : Optical microscope images (height 0.50 mm, width 0.62mm) of the self-repairing process of the gas barrier layer scratched
(left: just after being scratched, right: after being left for 60 minutes in humidity) |
Furthermore, the researchers investigated the coating process of the gas barrier layer by printing to realize the high-speed production necessary to practical application. They have developed the paste that can be printed uniformly, established printing conditions, and succeeded in producing rolls 50 cm in width. The oxygen gas barrier property of this film in dry condition was about 0.1 cc/m2·day·atm and it was sufficient for food package materials. The film shows total light transmittance of about 90 % and excellent resistance to folding. Letters and figures can be printed clearly on the gas barrier layer. Preparing a polypropylene layer on the gas barrier layer, bags can be easily manufactured (Fig. 1).
Future Plans
Regarding the developed film, Daiwa Can is aiming at commercializing it within six months. In addition, the researchers will work on the improvement in the water vapor barrier property in collaboration with Clayteam, and are planning to develop gas barrier films which can be used for a wide range of applications. Moreover, they are aiming to product not just films but also the coating solution for plastic films.