- Butanol of 80 wt% or higher concentration can be recovered from 1 wt% aqueous solution -
Keiji Sakaki (Leader), Hideyuki Negishi (Senior Researcher), and Toru Ikegami (Senior Researcher) of the Bio-chemical Processes Group, the Research Institute for Innovation in Sustainable Chemistry (Director: Masaru Nakaiwa) of the National Institute of Advanced Industrial Science and Technology (AIST; President: Tamotsu Nomakuchi), have developed an energy-saving technology for purifying biobutanol. It uses a zeolite-based membrane and can recover concentrated 1-butanol (hereinafter referred to as butanol) of at least 80 wt% (weight percent) from dilute aqueous butanol solution of about 1 wt%.
Butanol has a larger calorific value than ethanol. It is expected to ba a post-bioethanol fuel, namely a renewable liquid biofuel that is useful in mitigating global warming. A silicalite membrane that has high selective permeability for alcohol was synthesized through the optimization of synthesis conditions. The membrane enables the recovery of highly concentrated butanol from low-concentration aqueous solutions of butanol by membrane separation (pervaporation) (Fig. 1). Its use is expected to reduce the energy required to recover butanol by 50% to 70% of that required with conventional separation membrane methods.
The results of this study will be published online on November 13, 2010, in Chemistry Letters, the English journal of the Chemical Society of Japan.
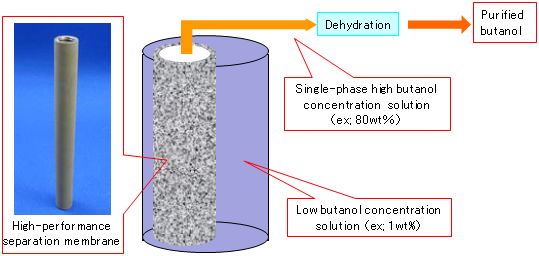 |
Figure 1 : Purification of butanol from a dilute aqueous solution of butanol by using the novel high-performance separation membrane |
The development of technologies for using bioalcohols, which are produced from biomass, as alternatives to fossil fuels is anticipated. Use of such technologies will not only reduce our dependency on petroleum but will also mitigate global warming, because biofuels are carbon neutral. Bioalcohols, such as bioethanol and biobutanol, can be produced from cellulose-type biomass including wood, the cultivation of which does not compete with food production. Butanol has a larger calorific value, 34 MJ/kg, than that of ethanol (27 MJ/kg), and is a highly usable liquid fuel. The main saccharides that constitute cellulose-type biomass are C6 and C5 sugars. In ethanol fermentation by yeasts, C5 sugars cannot be used. On the other hand, both types of sugar can be used by butanol producing microorganisms. Therefore, the development of butanol producing technologies for the effective use of biomass is eagerly awaited.
AIST has been engaged in the development of membrane separation technologies that are energy-saving for the condensation of alcohols (bioalcohols). A membrane that has high alcohol selectivity is indispensable for selectively separating and collecting ethanol or butanol from low-concentration aqueous solutions. Focusing on highly hydrophobic silicalite membranes, technologies have been developed to improve the performance of membrane separation and enable its application to butanol produced by fermentation.
A part of this R&D was supported by a project, “Development of Technology for High-efficiency Conversion of Biomass and Other Energy (Development of Preparatory Basic Bioenergy Technologies and Accelerated Advanced Technologies) (FY2006-2010),” commissioned by the New Energy and Industrial Technology Development Organization.
Usually, the concentration of butanol that is produced by fermentation is only 0.5 to 1.5 wt%, so the produced butanol needs to be condensed and dehydrated for use as liquid fuel. A large amount of energy is required to purify butanol by distillation from a dilute solution. For example, to concentrate a 1 wt% aqueous solution of butanol to 99.9 wt% by distillation, 37 MJ is needed per 1 kg of butanol. This means that, if butanol is condensed by distilling a dilute solution, the energy consumed for purification exceeds the calorific value of butanol (34 MJ/kg).
It has been reported that a silicone rubber separation membrane is effective in condensing a 1 wt% butanol solution (50 °C) to a maximum of 37 wt% and a separation membrane of silicone rubber containing silicalite powder can concentrate the dilute solution to a maximum of 53 wt%. Aqueous solutions of butanol with concentrations of 8 to 80 wt% separate into an upper phase where a small amount of water is dissolved in butanol and a lower phase where a small amount of butanol is dissolved in water (biphasic separation, Fig. 2). Therefore, a complicated system is required to recover and dehydrate all butanol from the liquid that has passed through the separation membrane, because dehydration has to be conducted separately for each phase (Fig. 3).
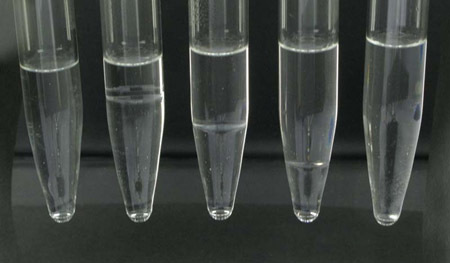 |
Figure 2 : Phase separation of butanol solutions
From left to right: 6.9 wt% butanol solution (homogenous phase), gross butanol concentration of 29.7 wt% (biphasic separation), 50.2 wt% (biphasic separation), 69.8 wt% (biphasic separation), 79.8 wt% (homogenous phase)
|
AIST has investigated conditions for preparing silicalite membranes coated with silicone rubber and has succeeded in preparing a separation membrane that has high selective permeability for butanol and can produce a homogenous 82 wt% butanol solution from a 1 wt% aqueous solution of butanol by pervaporation (Table 1).
Because the solution that passes through the membrane has a concentration of at least 80%, the solution does not separate into phases. Therefore, anhydrous butanol can be obtained just by dehydrating a single concentrated homogeneous phase, and the system for separation and purification of butanol is markedly simplified (Fig. 4). The total energy required to produce anhydrous butanol by recovering an 82 wt% butanol solution from a 1 wt% aqueous solution of butanol is calculated to be 4.3 MJ per 1 kg of butanol, even if the process of membrane separation before the dehydration is considered. Thus, butanol can be produced by consuming only about 13% of the energy of butanol. This is an approximately 70% reduction in the energy consumed when a silicone rubber separation membrane is used, and a reduction of about 50% of that used with a silicone rubber separation membrane containing silicalite powder. The newly developed high-performance separation membrane is expected to markedly reduce the amount of energy needed for purification of butanol.
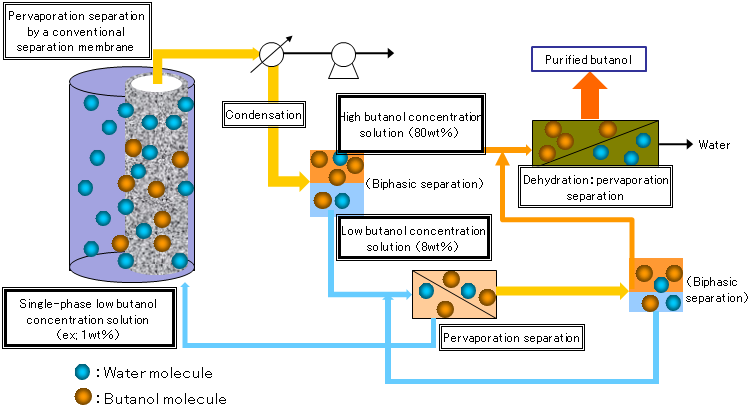 |
Figure 3 : Preparation system of anhydrous butanol from low-concentration aqueous solutions of butanol using a conventional separation membrane |
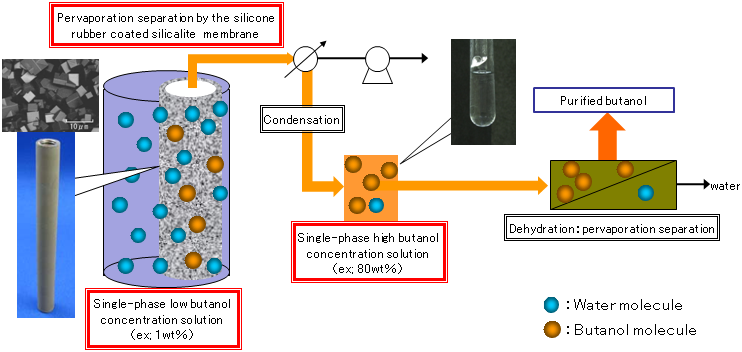 |
Figure 4 : Preparation system of anhydrous butanol from low-concentration aqueous solutions of butanol using the novel separation membrane |
Table 1 : Performance of the newly developed separation membrane (45°C)
|
Concentration of fed butanol
|
1.0 wt%
|
Concentration of permeated butanol
|
81.8 wt%
|
Flux
|
29.0 gm-2h-1
|
|
With the aim of early implementation of (bio)butanol production by using the newly developed high-performance separation membrane, a method for producing membranes of industrially applicable sizes by making them longer and modularization will be established jointly with the industrial sector. Research will then be conducted to further improve the performance of the membrane. The factors in fermentation media that could affect the performance of the system using the silicalite separation membrane will be clarified.