– A key device for automating conveyance and manufacturing processes in production plants –
Researchers) KURITA Tsuneo, Group Leader, Additive Processes and Systems Group, Advanced Manufacturing Research Institute
- Development of high-precision position and orientation measurement markers that can be used at manufacturing sites such as processing and assembly
- Easy and low-cost measurement simply by imaging self-creatable simple-shaped markers with a single dedicated camera
- Easy and high-speed setting of the position and orientation of workpieces, jigs, tools, robots, and other objects in the coordinate systems of machine tools, etc.
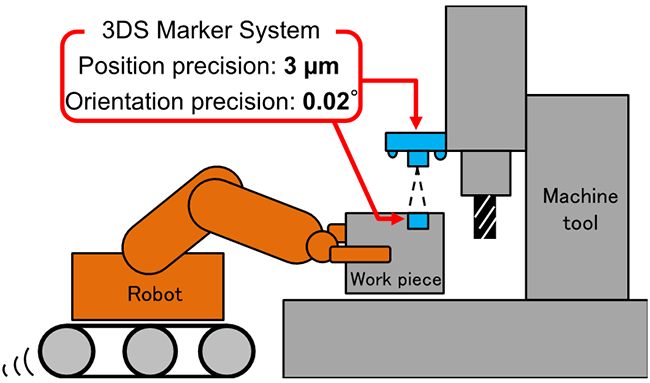
Image of 3DS Marker System utilization
In sites such as manufacturing plants, many and diverse types of work in progress, finished products, and other parts are present in various locations such as stockyards, conveying equipment, trays, and manufacturing equipment. To promote factory automation, it is necessary to sequentially understand the position and orientation of these parts and the process progress, and to convey the parts at high speed according to the order status and the equipment operating status. In addition, manufacturing sites have a setup process for picking, placing, and fixing parts with high accuracy on machine tools, or for reorienting and fixing parts again. This setup process is mainly performed by skilled technicians, but if it can be automated together with the conveyance process, this can become a fundamental technology for next-generation factories capable of stable variable-type, variable volume production with high efficiency.
However, processing accuracy of 0.01 mm or less is demanded for core parts in fields such as medicine, automobiles, and aircraft, so the setup process requires equivalent or higher accuracy. In addition, features such as low cost, simplicity, and robustness for easy introduction to factories are desirable, so development of unprecedented position and orientation measurement technology and devices is demanded.
Researchers in AIST developed a new measurement device, the 3DS Marker System, for position and orientation measurement of workpieces and other objects at manufacturing sites. This system is capable of high-precision position and orientation measurement with positional accuracy of 3 µm and orientation accuracy of 0.02°, and has features such as low cost, simplicity, robustness for easy introduction to factories compared to conventional systems.
This system uses arbitrarily shaped 3D markers with known steps and measures the position and orientation of the markers by imaging the shadow produced by the upper surface edges and lighting with a camera. A feature of the system is that shadows are used to measure position and orientation, so measurement is less affected by the surface roughness, color, and other characteristics of the marker material. Use of this marker system will enable to easily and quickly set the position and orientation of workpieces, jigs, tools, end effectors, and other objects in the coordinate systems of manufacturing equipment such as machine tools and robots as well as conveyance equipment. This system will contribute to automation of the conveyance and workpiece positioning processes in variable-type, variable volume production systems, etc.