Update(MM/DD/YYYY):09/26/2013
An Industrial Gasket with Excellent Sealing Properties and Electrical Insulation
- Uses a layered structure comprising clay films and expanded graphite sheets to enable a wide range of applications -
Points
-
A multilayered structure comprising clay-polyimide composite films and expanded graphite sheets
-
Excellent sealing properties in a wide temperature range, from ultralow temperatures to high temperatures
-
Excellent electrical insulation which prevents electric corrosion of the gasket and flanges
Summary
Takeo Ebina (Prime Senior Researcher) and his group, the Research Center for Compact Chemical System (Director: Takaaki Hanaoka) of the National Institute of Advanced Industrial Science and Technology (AIST; President: Ryoji Chubachi), Japan Matex Co., Ltd. (Japan Matex; President: Katsuro Tsukamoto), and Sumitomo Seika Chemicals Co., Ltd. (Sumitomo Seika; President: Yusuke Ueda) have developed an industrial-use sheet gasket by alternately laminating composite films of clay and polyimide and expanded graphite sheets (Fig. 1). The gasket boasts excellent sealing performance at from ultralow temperatures to high temperatures, and prevents flange corrosion because it is an insulator.
An integrated structure of the newly developed gasket, in which composite films fill the small spaces in expanded graphic sheets, substantially improves sealing properties without using metal. At an ultralow temperature (-196℃), the sealing properties of the new gasket surpass those of gaskets with multilayered structure of stainless steel sheets and expanded graphite ones—traditionally viewed as producing the best sealing properties—and represent the world’s premier sealing levels for a sheet gasket. The researchers have established a manufacturing method for the new multilayered sheet gasket and performed laboratory-based leak tests to confirm the gasket’s sealing performance. In addition, they have also conducted performance evaluations using high-temperature steam piping at an actual plant to confirm the gasket’s excellent sealing properties and durability.
The developed gasket is expected to be used as a sealing material for piping under a wide range of temperature conditions in a wide array of industrial applications, including geothermal plants, auto gaskets, oil refineries, petrochemical, power generation, steel, and paper manufacturing plants.
The results will be presented at the Renewable Energy 2013 Exhibition to be held from July 24 to 26, 2013, at Tokyo Big Sight (Koto-ku, Tokyo).
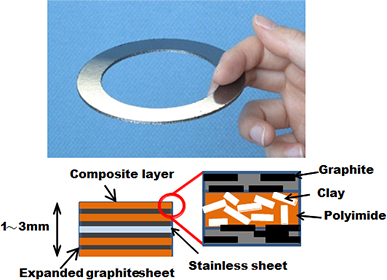 |
Figure 1 : Structure of the developed gasket |
Social Background of Research
Plants in many chemical industries use gaskets to prevent fluid and gas leakage from piping connections etc. Although asbestos gaskets were once used in high-temperature locations, strict controls and regulations on the use of asbestos opened the door for alternatives like expanded graphite products. However, conventional expanded graphite products suffer from problems, including graphite powder loss, burn-in, and poor sealing performance. Another type of gasket for high-temperature conditions combines vermiculite, a clay mineral, with organic compounds formed into a sheet. This gasket type poses a problem in that it lacks the sufficient density to provide satisfactory sealing. Thus, there was a need for a gasket capable of functioning properly in a wide range of temperatures.
History of Research
In 2004, AIST developed “Claist®,” a clay film made with small amounts of resin and has a uniform thickness without pinholes. Claist is a flexible and heat-resistant gas barrier material.
Having manufactured and marketed expanded graphite gasket products, Japan Matex proposed a composite of expanded graphite and Claist and teamed with AIST in FY2005 to launch basic research into the proposal. Based on the results, the researchers developed a new expanded graphite gasket coated with Claist. The gaskets have been used at approximately 50 sites throughout Japan, including nuclear power plants, and have driven the establishment of completely asbestos-free sites. The researchers won the Excellent Prize, the 2nd Monodzukuri Nippon Grand Award. They continued to develop manufacturing technologies and conducted product evaluation testing on sealing materials that could be used under high-temperature conditions (AIST press release on September 13, 2010).
However, these gaskets needed to be fitted with a metal frame or covered with a metal sheet to reach even higher sealing performance levels. This prevented electrical insulation being established, causing rust to form on the gasket and flange due to electric corrosion. Sumitomo Seika, which had been expanding into the development of highly functional materials, focused on AIST’s clay film technology and began joint research. From among the many possible combinations of clay and plastic, this research effort discovered a composite film with dramatically improved handling compared to the conventional clay films. Combined with Associate Professor (Tokyo University of Science) Takashi Yamashita’s knowledge of polyimide, this discovery led to further improvements in handling, a deeper understanding of excellent film characteristics, and the establishment of a production process for the raw material paste (AIST press release on August 30, 2011).
AIST, Japan Matex, and Sumitomo Seika thus worked together to develop an electrical-insulating gasket with a multilayered structure comprising composite films and expanded graphite sheets to enable applications in a wide range of temperature conditions.
Details of Research
Achieving sufficient adhesion is crucial when layering clay-polyimide composite films and expanded graphite sheets. To do so, the researchers selected the suitable clay and polyimide from a variety of candidate materials and determined the appropriate blend ratio and mixing method. By also optimizing the multilayering process conditions and making other adjustments, they manufactured a large (1 m × 1 m) multilayered sheet with a microstructure in which composite films penetrate the expanded graphite sheets. The crystals of the clay used for the sheet are flat and, unlike the needle-shaped crystals of asbestos, thus pose no threat to human safety.
Next, the researchers performed laboratory-based evaluation tests to confirm the gasket’s sealing properties and other basic characteristics. The tests involved punching out a piece of the multilayered sheet, using the piece to make a gasket prototype, and evaluating the prototype’s performance. The results showed that the gasket demonstrated good performance in all the tests, including strength and consolidation evaluations. The gasket also showed high levels of sealing performance in temperatures ranging from -196 ℃ to 350 ℃ and produced 30–50 % less leakage than previously developed gaskets. At low temperatures, in particular, the gasket demonstrates excellent sealing performance that transcends that of existing clay film-coated expanded graphite products and layered stainless steel-expanded graphite products (Fig. 2).
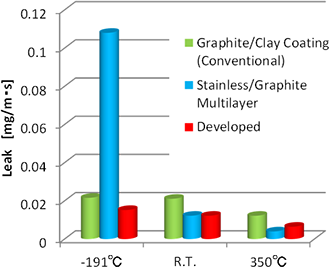 |
Figure 2 : Sealing properties of various gaskets |
The developed multilayered sheet uses hydrophobic clay with superb electrical insulation and is expected to exhibit good electrical insulation and prevent electric corrosion of the flange. Corrosion tests using sulfur-infused, simulated acidic geothermal water to assess viability at geothermal power plants showed that while conventional gaskets using metal sheets showed signs of corrosion on their flange surfaces, no corrosion was observed when the newly developed multilayered gasket was used.
Based on these results, the researchers conducted verification tests with the newly developed gaskets on a high-temperature piping of a plant at Befu Works of Sumitomo Seika. The fluid of the plant was steam with a temperature of 200 ℃ and a pressure of 25 atmospheres. The gaskets demonstrated excellent sealing capabilities over the two-month test period, showed no signs of deterioration, burn-in on the flange surface, or rust after removal, and exhibited high exchangeability (Fig. 3).
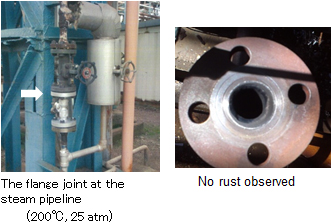 |
Figure 3 : The location of the pipeline where the test was conducted (left) and flange surface after gasket removal (right)
(at Befu Works of Sumitomo Seika) |
Future Plans
The researchers aim to conduct a wider range of performance evaluation of the gasket, evaluate long-term durability, establish a mass-production technology, and have commercial products available from Japan Matex within six months.