Update(MM/DD/YYYY):06/17/2008
Development of a Clay-Plastic Composite Material with Good Hydrogen Gas Barrier Property
- Applicable to hydrogen tanks for aircraft, rockets, and cars -
Points
-
A composite material was created by laminating a clay film, which shows good hydrogen gas barrier property, with carbon fiber reinforced plastic sheets.
-
The material has higher durability and more than 100 times higher hydrogen gas barrier performance than those of carbon fiber reinforced plastic.
-
It is expected to contribute the hydrogen storage technology necessary for realizing a hydrogen energy society.
Summary
Takeo Ebina (Leader), Material Processing Team, Research Center for Compact Chemical Process (Director: Fujio Mizukami) of National Institute of Advanced Industrial Science and Technology (AIST) (President: Hiroyuki Yoshikawa), Professor Koichi Yonemoto of Space Engineering Section, Department of Mechanical and Control Engineering, Faculty of Engineering, Kyushu Institute of Technology (KIT) (President: Teruo Shimomura) and Associate Professor Keiichi Okuyama of Department of Electronics and Control Engineering, Tsuyama National College of Technology (Tsuyama NCT) (President: Hideo Inaba), Institute of National Colleges of Technology, Japan have developed a new composite material for hydrogen tanks. The material has high hydrogen gas barrier performance and high durability.
The material is fabricated by laminating Claist®, a clay-based film, with carbon fiber reinforced plastic (CFRP) and processed at high temperature and pressure. This newly developed composite material has a simpler structure and higher reliability than the conventional materials using aluminum or high-density plastics as gas barrier liners. The results of preliminary tests such as durability tests have been accumulating, and at present, the outcomes have been favorable. This composite material is an excellent hydrogen gas barrier material, and is applicable to lightweight hydrogen tanks for use in aircrafts, spacecrafts and vehicles.
The details of this research were presented at SAMPE'08, held from May 18 in Long Beach, CA, U.S.A.
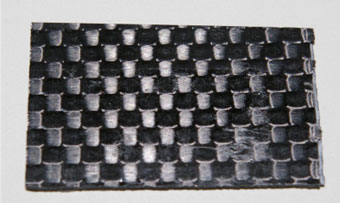 |
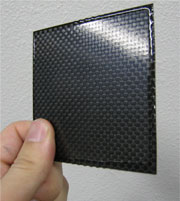 |
Developed clay film“Claist®”-carbon fiber reinforced plastic composite
(The cross stripe shows textile weaving pattern)
|
Social Background for Research
Composite materials, including CFRP, are used widely to reduce weight in aircrafts because of their superior strength. They are also expected to replace metals in liquid hydrogen tanks for aircrafts. However, plastics, i.e. organic polymeric materials, are not applicable as materials for hydrogen tanks due to their high hydrogen gas permeability. There have been some attempts to solve this problem: for example, a composite material was covered with a gas barrier layer consisting of aluminum or organic materials. However, it was not put to practical use because an aluminum gas barrier layer, though a good gas barrier, does not adhere to the composite material and is also heavy, while the organic materials are not good gas barriers. Nevertheless, there is an urgent need for lightweight on-board hydrogen tanks that are crucial in practical use of fuel-cell vehicles. Moreover, from the aspect of hydrogen energy use, a technology for reducing the leakage of hydrogen gas during transportation is desired.
The large cost of space transportation is a challenge for the further advancement of space development. To address this challenge, a reusable space transportation system similar to an aircraft is preferable to the conventional expendable ones. Realizing a reusable system will require further reductions in the weight of spacecrafts, and in particular, in the weight of the liquid hydrogen fuel tanks, which occupy most of the volume of the spacecraft.
History of Research
In August 2004, AIST announced the development of the Claist®, a clay-based film, which is made from clay with small amounts of resin and has a uniform thickness without pinholes. Claist is a flexible and heat-resistant gas barrier material, consisting of dense lamination of clay crystals with thicknesses of around 1 nm each (nm is one billionth of a meter). Excellent hydrogen gas barrier property of Claist was verified by testing it as a sealant for a high-temperature microreactor using hydrogen gas, which was developed by AIST.
At the same time, researchers at KIT and Tsuyama NCT, who had been working on development of CFRP hydrogen tanks, noticed this hydrogen gas barrier material, and began joint research with AIST on combining CFRP and Claist to develop liquid hydrogen tanks for reusable space transportation systems. From these joint efforts, processing methods for composite of CFRP and Claist were developed and, at the same time, measurement of properties of the composite, including a hydrogen permeability test and a durability test, was conducted.
This research was supported in part by JAXA as part of the project “Preliminary Composite Material Tests for Development of Liquid Hydrogen Tank (FY2007).”
Details of Research
The newly developed composite material was prepared by sandwiching Claist film between prepregs of CFRP, and then heat pressing them (Fig. 1). A sheet of Claist and three sheets of CFRP prepregs on each side were made into a sample piece of around 1 mm in thickness. The hydrogen gas barrier property of this sample was measured by gas chromatography using hydrogen gas at 7 atm. The results showed that it was over 100 times higher than that of materials previously reported. This corresponds to leakage of 0.01% of gas per year from a 50-atm hydrogen tank that is 5 m in length and 1 m in diameter.
Observation of a cross section of the composite material showed that the epoxy resin contained in the CFRP embedded itself in the surface roughness of both the CFRP and clay film layers, bonding them mechanically and attaching them firmly to each other (Fig. 2).
It was confirmed that the hydrogen gas barrier property was not lowered even after repeated distortion (10,000 times) or exposure to cryogenic temperatures of –196 °C in durability tests. This result proves that this composite material is a potential material for hydrogen tanks that will be used under cryogenic temperatures and high pressures.
This composite material is widely applicable to various hydrogen storage containers that require further weight reduction, including hydrogen gas tanks for cars, fuel cell containers, and transportable liquid hydrogen storage facilities. Loss of hydrogen gas can be lowered by actively using this composite material, which reduced the leakage of hydrogen gas from long-term storage units. This is expected to lead to energy savings and contribute to the development of low-environmental-load processes.
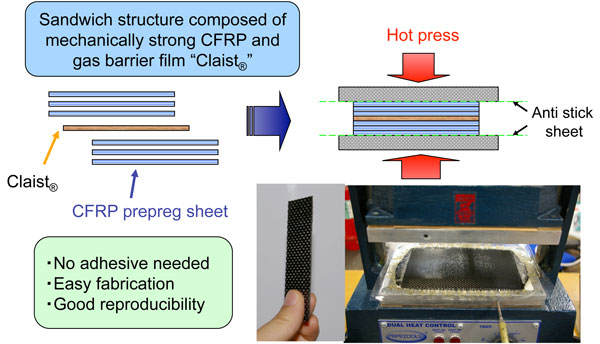 |
Fig.1 Fabrication of the composite
|
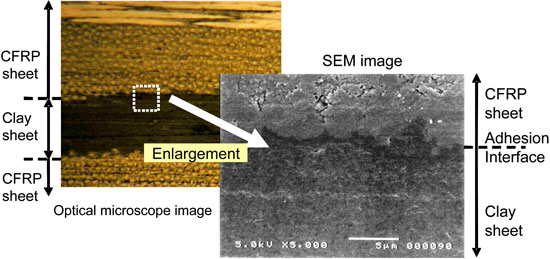 |
Fig. 2 Microscopic photographs of the composite
|
Future Schedule
We will examine the applicability of this composite material for various purposes after conducting extensive performance evaluations on tanks made of this material. The main challenges for practical use are the prevention of hydrogen gas leakage, which is directly associated with safety, and the establishment of low-cost manufacturing methods that can achieve uniform quality.