Update(MM/DD/YYYY):11/25/2016
Development of an Electro-conductive Transparent Plastic Wrap
– Will lead to sensors on fresh food packaging –
Points
-
Technology was developed that incorporates wave-shaped ultra-fine metal wires between two sheets of flexible film.
-
The technology simultaneously achieves high elasticity, transparency, electrical stability, and strength.
-
The results will contribute to the popularization of free-form sensors by allowing sensors to be mounted on curved surfaces.
Summary
Manabu Yoshida (Leader), Sei Uemura (Senior Researcher), and Taiki Nobeshima (AIST Postdoctoral Researcher), the Printed Electronics Device Team, the Flexible Electronics Research Center (Director: Toshihide Kamata), the National Institute of Advanced Industrial Science and Technology (AIST; President: Ryoji Chubachi), in collaboration with Tokusen Kogyo Co., Ltd. (Tokusen Kogyo; President: Hiroaki Kanai), have developed electro-conductive transparent plastic wrap.
Using the high-strength, high-elasticity metal wire with the world’s smallest diameter developed by Tokusen Kogyo, the researchers have developed a process for incorporating the wire in the shape of waves between two sheets of flexible film. This process makes it possible to fabricate electro-conductive plastic wrap that is simultaneously highly elastic, transparent, electrically stable, and strong. This transparent plastic wrap has applications including sensor-equipped packaging for perishable food and sensors mounted on curved surfaces, and is expected to contribute to the popularization of free-form sensors.
Details of the technology will be presented at the Printable Electronics 2016 to be held on January 27-29, 2016 at Tokyo Big Sight in Koto ward, Tokyo.
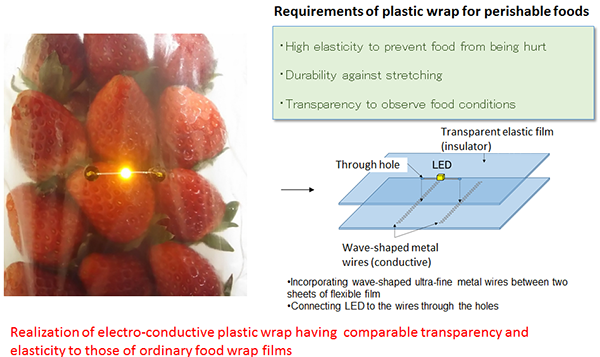 |
Example of uses of the developed conductive transparent plastic wrap as packaging for strawberries, with an LED connected to the surface |
Social Background of Research
Concern for food safety has been growing rapidly in recent years. For perishable food in particular, there has been an increasing need for simple and easy freshness management during transportation and in-store display. Various sensors are currently examined for freshness management. However, how to incorporate the sensors has become an important issue, because food products are often soft and come in a wide variety of shapes.
Meanwhile, the recent growth of interest in wearable devices has led to growing demand for, and active research and development in flexible electronic materials. These flexible electronic materials have shown great promise for use as components in sensor systems for perishable food. However, connecting the sensors requires conductive wiring that is flexible and stretchable. Because until now there has been no wiring material that is simultaneously highly elastic, transparent, electrically stable, and strong, development of an electro-conductive film with all of these properties has been desired.
History of Research
AIST has been actively pursuing research and development on flexible large-area electronic devices and electronic devices adaptable to various shapes. With the goal of developing electronic device manufacturing technologies using printing manufacturing processes mainly, AIST has developed memory arrays, RF tags, transpiration rate sensors, large-area pressure sensors, etc. manufactured using printing processes. Recently, AIST has focused on the development of flexible large-area devices to fit curved surfaces such as the human body and food products, and has been exploring flexible, electro-conductive film materials that are simultaneously highly elastic, transparent, electrically stable, and strong.
Meanwhile, Tokusen Kogyo, which has the world's premier wire drawing technology, had succeeded in developing a high-strength wire with a high elastic modulus and the world's smallest diameter.
The researchers therefore decided to combine AIST's flexible device development technology with Tokusen Kogyo's ultra-fine wire in order to achieve their goal of a flexible, electro-conductive film with a combination of high elasticity, transparency, electrical stability, and strength that had not existed before.
Details of Research
The structure of the developed transparent, highly elastic electro-conductive plastic wrap consists of wave-shaped ultra-fine metal wires incorporated between two sheets of flexible film. The invention of a process to achieve this structure is what led to the development of this electro-conductive plastic wrap. In addition, it was discovered that the Young's modulus (modulus of elasticity) of the ultra-fine metal wire strongly influenced the wave shape of the ultra-fine metal wire when it was incorporated between the sheets of flexible film (Fig. 1). Figure 2 shows micrographs of the actual wave shapes of ultra-fine metal wires between the two sheets of flexible film. A 9 μm-diameter piano wire was used as the high-elasticity wire, and a 30 μm-diameter copper wire as the low-elasticity wire. The high-elasticity wire shows a relatively large radius of curvature at the top of the wave, while the low-elasticity wire has a smaller radius of curvature, making it more susceptible to metal fatigue and breakage with repeated stretching. Consequently, using high-elasticity piano wires as the ultra-fine metal wires allowed a larger radius of curvature of the top of the wave-shaped wires, making it possible to fabricate a disconnection-resistant but highly elastic electro-conductive plastic wrap that resists metal fatigue even when stretched.
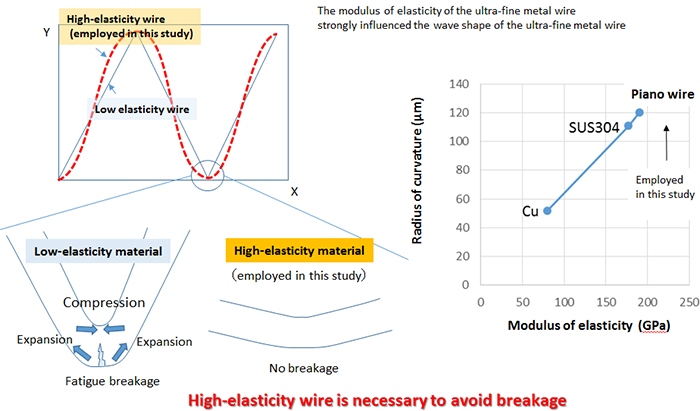 |
Figure 1: Relationship between the modulus of elasticity of the wire and its wave shape |
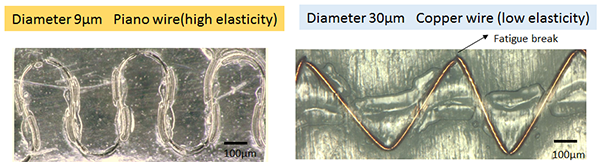 |
Figure 2: Micrographs of the wave shapes when using a high-elasticity wire (piano wire: left) and a low-elasticity wire (copper wire: right) |
In general, the smallest objects that can be seen by a person with 20/20 vision from a distance of 30 cm are in the range 50 μm to 100 μm. The 9 μm-diameter piano wires used in the developed electro-conductive plastic wrap is difficult to see with the naked eye, ensuring sufficient transparency of the wrap (Fig. 3, top). The wrap also exhibits electro-conductivity due to the wave-shaped ultra-fine metal wires. Because the wiring is done in a wave-shaped pattern, the length of the wire itself remains unchanged even when stretched, which means that in principle, the electrical resistance (which is proportional to the length of the wire) does not change. Consequently, when the wave-shaped wire is used as wiring for an LED (bottom left of Fig. 3), the LED's brightness does not waver even when the wrap is stretched. In addition, because the ultra-fine metal wire used here is a piano wire, it is extremely strong and does not break even when the electro-conductive plastic wrap is folded and struck with a hammer (bottom right of Fig. 3).
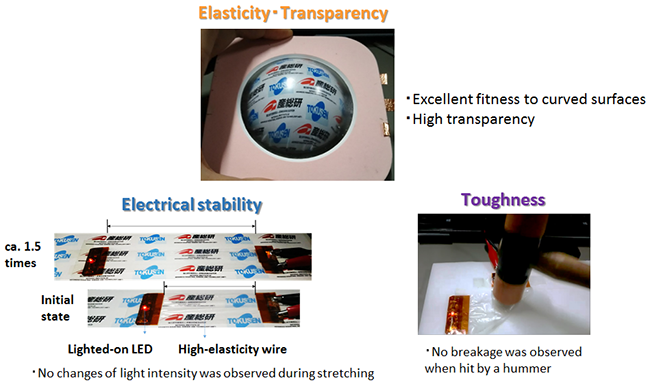 |
Figure 3: Features of the newly developed conductive transparent plastic wrap |
As shown in Fig. 4, the researchers were able to create a transparent and flexible touch sensor from the developed conductive transparent plastic wrap by connecting it to circuitry for detecting changes in capacitance. The sensor works by detecting the change in capacitance when an area of the ultra-fine metal wiring is touched.
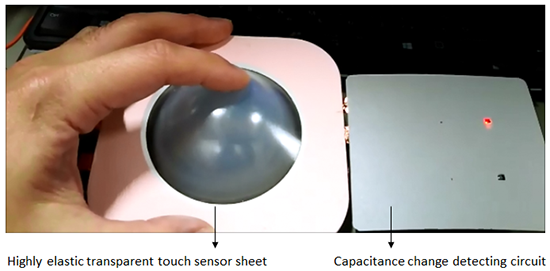 |
Figure 4: Touch sensor created by connecting circuitry for detecting changes in capacitance to the developed electro-conductive transparent plastic wrap |
Future Plans
Future plans include improving the efficiency of the manufacturing process in order to establish a mass-production system for the conductive transparent plastic wrap and pursuing various applications that use the developed wrap such as curved-surface touch panels and wearable sensors.