Update(MM/DD/YYYY):01/10/2014
Dramatic Improvement in the Heat Resistance of Transparent Oil-repelling Coatings
- Environmentally friendly surface treatment technology that uses non-fluorinated organic compounds -
Points
-
The development of an oil-repelling surface treatment with excellent heat resistance (over 24 hours in 350 ℃ air or in a 250 ℃ oil bath)
-
Low cost and low environmental impact without the use of fluorinated organic compounds or special equipment
-
Expected as an oil-repelling treatment for high temperature components, such as distillation towers, engines, oil pumps, and oil ducts
Summary
Atsushi Hozumi (Leader) and Chihiro Urata (Researcher) of the Durable Materials Group, the Materials Research Institute for Sustainable Development (Director: Mamoru Nakamura) of the National Institute of Advanced Industrial Science and Technology (AIST; President: Ryoji Chubachi), have developed a transparent oil-repelling coating with excellent heat resistance (performance retained for more than 24 hours in air of 350 ℃ or in an oil bath of 250 ℃) that avoids the use of fluorinated organic compounds.
Currently, many oil-repelling treatments rely on fluorinated organic compounds or micro-machined surfaces. However, fluorinated compounds affect the human body and the environment, while micro-machining requires special equipment and conditions. Therefore, there is a demand for surface treatment technologies which do not rely on fluorinated compounds or micro-machining.
By focusing on the heat resistance of the methylsiloxane skeleton and using methylsilane as the main component, a transparent film coating with excellent heat resistance and oil-repelling properties was developed. Furthermore, no special equipment is needed to apply this heat-resistant transparent coating. It can be used in the treatment of various surfaces that are exposed to high temperatures during use, such as distillation towers, engines, oil pumps, and oil ducts. The coating, as an alternative to oil-repelling treatments that use fluorinated compounds, is expected to contribute to cost reductions and improvements in safety and reliability.
The details of this technology will be presented at the 128th Meeting of the Surface Finishing Society of Japan to be held at Fukuoka Institute of Technology (Fukuoka City, Fukuoka Prefecture) on September 24 and 25, 2013.
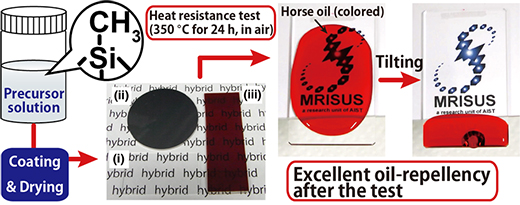 |
Manufacturing method of the developed coating (i: Glass plate, ii: Stainless steel plate, iii: Polyimide film), and how oil is repelled even after the heat resistance test (shown using colored horse oil) |
Social Background of Research
Fluorinated organic compounds have many excellent features including weather resistance, chemical resistance, and heat resistance, and are used in various industrial applications as the main raw material for oil-repelling agents. In recent years, further improvements in oil-repelling properties have been achieved by coating substrate surfaces, which have micrometer- to nanometer-scale structures, with fluorinated compounds. On such treated surfaces, even tilting the substrate slightly makes an oil droplet slide off like a water droplet from the surface of a lotus leaf.
However, fluorite required for the manufacture of organic fluorine compounds is unevenly distributed on earth, which makes its price volatile and its supply unstable. In addition, the high residual and bioaccumulation properties of fluorinated compounds in both organisms and the environment have been pointed out, and restrictions are getting stricter year-by-year. In addition, when fluorinated compounds are exposed to temperatures exceeding their heat-resistant temperatures, highly-corrosive toxic gas is generated, creating safety issues under high temperature use. Furthermore, in many cases, micro-machining used to fabricate substrates with micrometer- and nanometer-scale structures requires special equipment and processing conditions, imposing limitations on the substrate materials and their shapes which create problems in terms of productivity and processability. Also, microstructures tend to scatter light, meaning that securing the transparency of coated surfaces is difficult.
The development of materials and process technologies that do not rely on fluorinated compounds are desirable, as it not only makes the technologies more friendly to both living organisms and to the environment, but also from the viewpoint of energy and resource conservation, low environmental impact, and safety.
History of Research
AIST started R&D for an oil-repelling treatment that does not rely on fluorinated organic compounds or micro-machining in 2011, and discovered that a transparent coating produced from alkyltrialkoxysilane (organic silane), a widely used water repelling agent, and tetraalkoxysilane (spacer silane), which is used as a raw material for glass, showed excellent oil-repelling properties (AIST press release on March 13, 2012). No special equipment or conditions are required to use the coating, which can be applied to a wide variety of substrates (glass, metals, plastics, etc.). Furthermore, its oil-repelling properties exceed those of surfaces treated with fluorinated compounds (perfluoroalkyltrialkoxysilane (organic fluorine silane)) and surfaces of fluorinated resin. However, the previously developed transparent oil-repelling films are inferior in heat resistance, and when heated in air at temperatures higher than 150 ℃ for prolonged periods, the films would disintegrate bringing about failure of its oil-repelling properties, making it unsuitable to surfaces exposed to high temperatures for prolonged periods. This is because the C-C bonds in organic silane slowly deteriorate and decompose in a high temperature environment.
To address this problem, research was carried out to find surface treatment technology that maintains long-term oil-repelling properties, even in high temperature environments, but without the use of fluorinated organic compounds.
Details of Research
In this study, focus was placed on the heat resistance of the methylsiloxane skeleton and it was discovered that methylsilane is effective as a raw material of the heat-resistant oil-repelling coating. The heat-resistant oil-repelling coating film is manufactured under a process similar to that detailed in the previous release (AIST press release on March 13, 2012). The coating liquid is prepared using organic silane that includes the methylsilyl group as a raw material. This liquid is then applied onto substrates made of glass, stainless steel, or polyimide films, etc., and a transparent coating of approximately 1 μm thickness is obtained after drying. Observations conducted using a scanning electron microscope and an atomic force microscope confirmed that the surface of the coating film is very smooth (root mean square roughness <1 nm). Measurement of the dynamic contact angle for n-hexadecane, a representative of an oil droplet, revealed that contact hysteresis (Δθ = 6 degrees) is very small as the previously developed oil-repelling coating, and that the oil droplet will slip smoothly off the surface even when the substrate is tilted only very slightly. Next, the heat resistance of both the previously developed coating film and the newly developed coating film was tested in air. With the previously developed coating film, the oil-repelling properties disappeared after heating over 150 ℃. Whereas, the newly developed, heat-resistant coating film showed no deterioration in its oil-repelling properties even after being heated continuously for more than 24 hours at 350 ℃, demonstrating excellent heat resistance (Fig. 1). The reason this excellent oil-repelling characteristic is maintained is believed to be that the methylsiloxane skeleton, the oil-repelling component, does not change even after being exposed to heating, since no C-C bonds are included in this coating film.
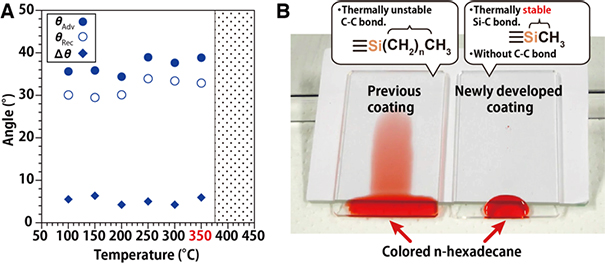 |
Figure 1 : (A) Dynamic contact angle changes of n-hexadecane and (B) oil-repelling properties after heating at 350 ℃ (Test piece inclined at 5 degrees) of the previously developed oil-repellent coating and the newly developed oil-repellent coating |
Next, the heat resistance of the newly developed coating film was investigated in an oil bath. The newly developed coating film and the previously developed coating film together with an uncoated stainless steel plate and an uncoated polyimide film were immersed in an oil bath (filled with heat-resistant oil) heated to 250 ℃ in air (this is the highest-revel temperature that liquids can be heated in air) and then left for 5 minutes. Adhesion of oil droplets was observed on all surfaces, except for the newly developed coating film (Fig. 2A). To investigate the durability of this coating film, a stainless steel disc coated with the newly developed coating film was half-immersed and rotated in heat-resistant oil heated to 250 ℃. No adhesion of heat-resistant oil was observed even after 30 hours of heating (Fig. 2B). (The test was terminated due to changes in the oil color.)
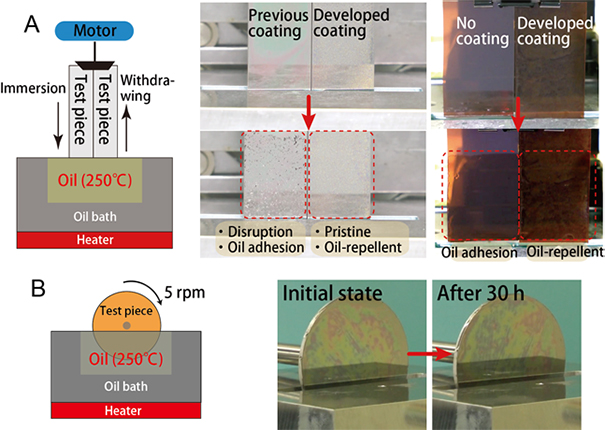 |
Figure 2 : (A) Left: Heat resistance test method. Center: The previously developed and the newly developed oil-repellent coatings on stainless steel plates. Right: Uncoated polyimide film and polyimide film coated with the newly developed coating.
(B) Left: Heat resistance and durability test method for the newly developed oil-repelling coating. Center: Immediately after the start of the test. Right: After 30 hours. |
When resin flux-cored solder was heated (220 ℃) on the surface of a stainless steel plate coated with this film, the melted solder and flux slipped off without soiling the surface (Fig. 3B). However, the distinct remains of the flux are evident on an uncoated stainless steel plate (Fig. 3A). By using the newly developed coating, it has been proven that the heat resistance and oil repellency can be maintained, regardless of the substrate material. With this drastic improvement in heat resistance, various uses of the safer, more stable, and environmentally friendly heat-resistant oil-repelling treatment are expected in wider fields and applications.
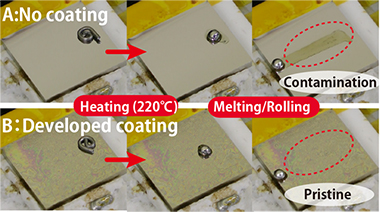 |
Figure 3 : Heated flux-cored solder
((A) Uncoated stainless steel plate and (B) stainless steel plate with the newly developed surface treatment) (Test piece tilted by 5 degrees) |
Furthermore, a phenomenon was observed on the newly developed oil-repelling surface where the static contact angle of the droplet increased with the increase in film surface temperature (Fig. 4). This phenomenon remained even after more than 10 cycles of heating-cooling. This indicates that the response is not a transitory reaction but a reversible temperature response (Fig. 4B and 4C). It has been discovered that by using this characteristic, a droplet will move across a horizontally placed coated film spontaneously, being driven by a temperature gradient (heated on one side only) (Fig. 4D). In addition, it has been clarified that this characteristic relies significantly on the type of the droplet. By understanding the details of these characteristics, the forecast of the movements of droplets in high temperature environments and the development of oil transport systems using temperature gradients can be expected.
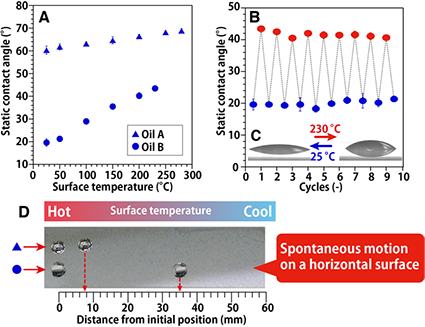 |
Figure 4 : A stainless steel substrate with the newly developed coating
(A) Temperature dependence of static contact angles, (B) cyclic characteristics of static contact angle of silicone oil on the substrate, (C) change in appearance of the oil, and (D) spontaneous movement phenomena of droplet driven by a temperature gradient. |
Future Plans
The newly developed coating film can be applied to a wide variety of solid surfaces, and the researchers plan to customize the coating method to match needs of different applications. Research will continue for further improvement in heat resistance to enable the oil-repelling properties to be maintained over an extended period, for use on various surfaces exposed to high temperatures during use, such as distillation towers, engines, oil pumps, and oil ducts.