- Measurement technology for thermal expansion even at ultra-high temperatures that simultaneously utilizes a contact method and a non-contact method -
Hiroshi Tsuda (Leader) and Norio Iwashita (Chief Senior Researcher), Structure Image Diagnosis Group, the Research Institute of Instrumentation Frontier (Director: Yukihiko Yamauchi) of the National Institute of Advanced Industrial Science and Technology (AIST; President: Ryoji Chubachi), have developed a device capable of measuring the thermal expansion of industrial carbon materials, such as artificial graphite, in the ultra-high temperature region up to 2400 ℃.
This device simultaneously measures the dimension change of a test piece due to thermal expansion by two methods—a contact method and a non-contact method. The former uses high-density isotropic graphite as a reference and the latter uses a laser microgauge (LMG). The complementary use of these methods enables the device to accurately measure the linear thermal expansion and the coefficient of thermal expansion (CTE) in the high temperature region of 2400℃. This device is expected to contribute to the sophistication of technologies such as steel manufacturing, refining, and semiconductor manufacturing, which use artificial graphite for heaters, etc. The details of this technology will be presented at the 40th Annual Meeting of the Carbon Society of Japan, to be held from December 3 to 5, 2013, at the Kyoto Education and Culture Center (Kyoto).
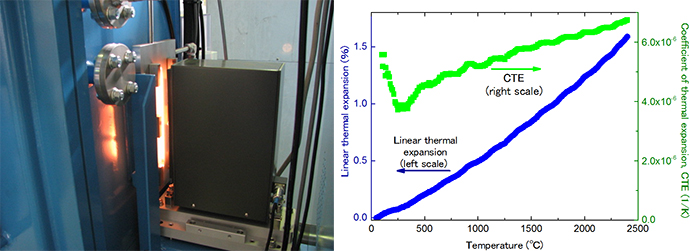 |
(Left) Element of measurement at 2400 ℃ (optical receiver of LMG)
(Right) Temperature dependence of the linear thermal expansion and CTE of an isotropic graphite material that was obtained by the developed device. |
Artificial graphite materials are critical for manufacturing industries requiring materials that are resistant to high temperatures and are electrically conductive. Such industries include silicon semiconductor manufacturing, electric furnace steel manufacturing, and aluminum refining. In recent years, the manufacturing processes of these manufacturing industries have been enlarged, and the importance of temperature control using artificial graphite materials is increasing. In addition, because the crystal growth process at temperatures higher than 2000 ℃ is required in the manufacture of power semiconductor materials, such as SiC single crystals, it is now necessary to evaluate physical properties in the ultra-high temperature region. However, because the properties of artificial graphite materials, such as electrical resistance, thermal conductivity, and mechanical strength, at high temperatures are strongly affected by raw materials and manufacturing methods, these properties are different among artificial graphite materials, and temperature dependence of the properties must be measured for each material.
Previously, AIST developed a device that could measure physical properties, such as mechanical strength and electrical resistance, at higher temperatures than 2000 ℃. The temperature dependence of various artificial graphite materials was evaluated at high temperatures. In the present research, the researchers have strived to develop a device that could simultaneously use the contact and non-contact methods for measuring thermal expansion at high temperatures.
A part of the present results is obtained through the "Research of Manufacturing/Product Advancement by Evaluating the Measurement of the High-temperature Properties of Industrial Carbon" of the project to support the advancement of strategic core technologies.
In order to use materials in high-temperature processes, the materials themselves must have thermal shock resistance, such as fire and thermal resistance. Generally, the volume of a material changes depending on temperatures, so the dimension change per 1 ℃, i.e. CTE, is an indicator for evaluating thermal shock resistance. The test methods for thermal expansion of refractory products at high temperatures have been standardized as JIS R2207 "Test Methods for Thermal Expansion of Refractory Products." However, the sintered high-purity alumina that was conventionally used as the reference material for measuring linear thermal expansion by the contact method cannot be used at temperatures higher than 2000 ℃. Only graphite, which has higher thermal resistance, can be used at such temperatures. In addition, when measuring the thermal expansion using a non-contact method that uses a laser scanning dimension measurement device, such as LMG, radiant light from the electrical furnace at ultra-high temperatures is very intense, causing scattered light to enter the light receiving part. Therefore, the maximum temperature under which these methods could be used was approximately 1800 ℃.
In the present research, the researchers developed a thermal expansion measurement device for ultra-high temperatures by using high-density isotropic graphite for the reference material, as well as for the heaters and measurement jigs. Using the contact method, measurements are possible up to about 3000 ℃, which is the heat-resistance temperature of high-density isotropic graphite. In the ultra high-temperature region, however, there is a large difference between the temperature inside the furnace and the temperature of the differential transformer (extensometer) installed outside the furnace, resulting in large measurement errors. To address this, the researchers introduced LMG to make it possible to compare measurements made by the contact method and non-contact method. In relation to measurements with the non-contact method, they made it difficult for scattered light from the electric furnace to enter the LMG light receiving part. As a result, the linear thermal expansion coefficient can be measured up to 2400 ℃ by both methods simultaneously. Figure 1 shows schematic illustrations of the developed device. Heaters made of high-density isotropic graphite are placed on the front and back sides of the electric furnace in order to set the test piece and measurement jigs. The heater on the front side is attached to the inside of the electric furnace door. Optical paths are secured on the right and left sides, so LMG measurement can be performed. The test piece, detection rod, and differential transformer for contact method measurements are installed in the vertical direction. As for the size of test pieces of this device, a round rod 20mm in diameter and 100mm long was adopted. This is the size that conforms to JIS standards (JIS R7222) for methods of measuring the physical properties of industrial carbon materials.
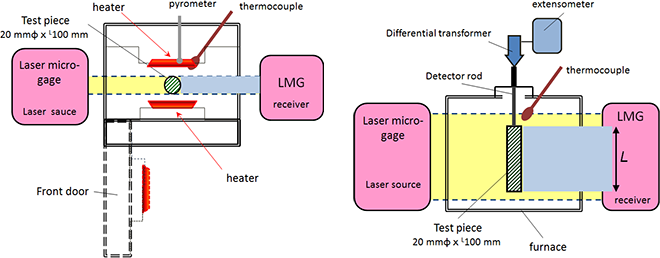 |
Figure 1 : Schematic illustrations of the ultra high-temperature thermal expansion measurement device
(Left) Projection illustration from above and (right) projection illustration from the front
L is the length of test piece. Measure the linear thermal expansion by changing the temperature and measuring the change in L. |
Figure 2 shows the measurement results of the developed device. Figure 2 (left) depicts the results using LMG to measure the changes in length of the reference material, high-density isotropic graphite, due to thermal expansion. In the results up to 1400 ℃, the amount of change matched well with that calculated using the thermal expansion obtained by a conventional method. Also, the data in the temperature region higher than 1400 ℃ are the measurement results obtained for the first time and will serve as new reference data. There was almost no difference in the data for the heating process and cooling process.
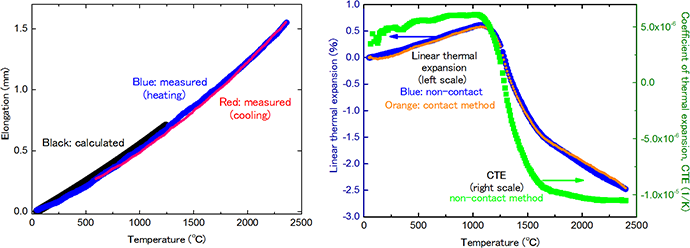 |
Figure 2 : Measurement results by the developed device
(Left) LMG measurement results of the change caused by the thermal expansion of high-density, isotropic graphite (reference substance) and comparison with calculated values
(Right) Measurement results of the linear thermal expansion (contact method and non-contact method) and CTE during the graphitization of raw graphite material |
Ultra-high temperature heat treatment called "graphitization" is one of artificial graphite production processes, and during this process, the phenomenon of thermal shrinkage occurs. This thermal shrinkage could be observed in situ, when the changes in length of a test piece up to the ultra high-temperature region of 2400 ℃ were measured using the developed device. Figure 2 (right) shows the evaluation results of the test piece of raw graphite material that underwent primary firing. Thermal expansion is observed up to 1000 ℃, but sudden thermal shrinkage accompanied by crystallization began when temperatures exceeded 1000 ℃. Also, it was discovered for the first time that the thermal shrinkage behavior changes at approximately 1600 ℃. These will be fundamental data for the improvement in yield reduction caused by thermal shrinkage. In addition, there was hardly any difference in the values of CTE measured by the LMG non-contact method and the contact method. Both methods complemented each other and were confirmed to have made accurate measurements.
In the manufacture of power semiconductor materials such as SiC, the graphite material having a small value of coefficient of thermal expansion in the ultra high-temperature region is preferable in order to create large single crystals. In the LMG non-contact method using the developed device, precise measurements are possible on the order of micrometers, so this method is expected to contribute to the advancement of power semiconductor manufacturing.
The researchers will measure the linear thermal expansion and CTE of various types of industrial carbon and accumulate the data. they will research how starting materials, production conditions, and crystal structures affect CTE. After several years, the researchers will look into transferring this measurement technology to outside organizations.