実験化学で新たなリサイクル技術を開発
実験化学で新たなリサイクル技術を開発
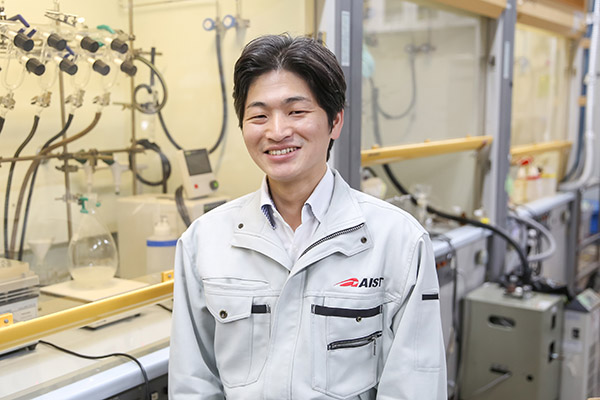
2023/06/14
実験化学で新たなリサイクル技術を開発 「ボトル to ボトル」、「繊維 to 繊維」のケミカルリサイクル
日本では年間約58万トンのPETボトルが使われており、そのリサイクル率は約86 %と高い水準にある。現在、主にPETボトルリサイクルに使われているマテリアルリサイクル法は、PETボトルを材料として、PETボトル以外のプラスチック製品の材料を再生する手法だ。だが、この方法ではリサイクルを繰り返すうちに不純物が増え、最終的に焼却処分せざるを得なくなってしまう。そこで、欧米や日本を中心にPETボトルからPETボトルを作る「ボトル to ボトル」を実現するケミカルリサイクル法と呼ばれる技術が開発されてきたが、従来のケミカルリサイクル法は、エネルギーを大量に使って高温高圧で反応させる必要があり、リサイクル技術としては大きな課題があった。
産総研は触媒反応を使った新たな分解手法を発見し、低いエネルギー消費で「ボトル to ボトル」を効率的に実現するケミカルリサイクル法を開発した。(2021/11/8 プレスリリース記事) この方法を衣類のリサイクルに応用した「繊維 to 繊維」の可能性も見えてきており、実現すれば石油由来の繊維製品のリサイクルも促進され、環境負荷軽減に大きく貢献できることになる。研究を進めた触媒化学融合研究センターケイ素化学チームの田中真司に聞いた。
常温で実現! PETボトルの原料化
日本社会ではさまざまな製品のリサイクルが進んでいる。国内で年間約58万トン使われているPETボトルの約86 %はリサイクルされており、リサイクルの優等生だといえる。しかし、PETボトルの低コストでのリサイクル法として知られるマテリアルリサイクル法は、回収したPETボトルを分別、粉砕、洗浄することでPETの原料フレークを再生する。この方法では、何度もリサイクルを繰り返すうちに、不純物の影響でポリマーが劣化し性能が低下するため、元のPETボトルには再生できなくなってしまう。
そこで、日本や欧米を中心にPETボトルを材料としてPETボトルに作り替える「ボトル to ボトル」を実現するケミカルリサイクル法が開発された。化学的にPETを分解して再生するケミカルリサイクル法の一種として、PETにメタノールを加えてポリマー状態のPETを分解する手法が知られている。しかしこの反応は、副生成物のエチレングリコールが化学平衡に従って再びモノマーと反応してしまうため、大量のメタノールを使用し、さらに200 ℃~300 ℃程度の高温・高圧条件で反応させて化学平衡をモノマーに傾ける必要があった。このようにケミカルリサイクル法は最終的な廃棄量を減らすことができるが、分解のプロセスのエネルギー効率が悪いことに問題があった。常温で分解する反応方法で、このエネルギー効率の悪さを解決したのが、触媒化学融合研究センターの田中真司だ。
「常温でPETが分解できた結果を最初にみたときは、ほんまかいな?って思いました。慎重にもう一度自分で実験してみて、やっぱり正しいんだと確認しました」と、昨日のことのように話す。PETを分解する時に、メタノールとともに炭酸ジメチルを使うことで、PET分解反応の邪魔をする副生成物のエチレングリコールを化学的に安定な炭酸エチレンに変換するのがポイントだ。
PETにメタノールを加えてPETを分解しエチレングリコールを生成する、従来の高温高圧条件が必要な反応と、
エチレングリコールと炭酸ジメチルが反応し、メタノールと炭酸エチレンを生成する反応。
この2つの反応をうまく組み合わせて常温・常圧で反応が進むようにしたのが、田中の画期的なアイデアだ。
「さっそく試してみたくて、自販機でコーヒーを買ってきてPETボトルを粉砕機にかけてパウダー状にして実験を始めました。PETのパウダーに溶液を加えると、最初は溶けないんですが、うまく反応するとだんだん溶けていき、白く見える撹拌子(かくはんし)だけが残ったんです」
続いて触媒を色々と試した結果、リチウムメトキシドを触媒に使うことで、9割ほどのPET原料を回収できることがわかった。結果は想像以上だった。
田中は今回の成果の鍵となったエチレングリコールのようなアルコールと、さまざまなエステル化合物を反応させる「エステル交換反応」を以前から研究していたことが、今回のアイデアにつながったと振り返る。
常温・常圧の反応容器でPETの粉末を分解させる
スケールアップと低コスト化には企業の力が不可欠
次の目標は実用化だ。この反応が実際にPETボトルのリサイクルに使われるためには、スケールアップが必要だ。実験室ではせいぜい1 kgを扱うのが限界だが、この反応を数万トンのPETを扱える化学プラントで実現しなければならない。プラントスケールともなると、反応容器の設計や反応液を混ぜる羽根の微細な形状、投入する溶液量の調整など企業が持つさまざまなノウハウがあってこそ実用化が見えてくる。また、コスト面での工夫も重要だ。炭酸ジメチルの価格は高いので、反応プロセスに必要な量を可能な限り減らしたり反応後に回収したりできるような仕組みも必要となるだろう。
「1 kgのスケールを越えたところからは企業に主体を担ってもらい、実用化まで一緒にすすめていきたいと考えています。浮かび上がってくるさまざまな課題を企業と一緒に解決しながら、自分が見つけた反応がどうやって社会で使われるようになるかを追いたいんです」
現在のPETボトルリサイクルの主流は不純物の混入やポリマーの劣化が起きてしまうマテリアルリサイクルだが、ケミカルリサイクルのコストが抑えられエネルギー効率が向上すれば、将来的にはより持続可能な手法としてケミカルリサイクルが選ばれる可能性が高まる。
化学反応で社会を変える!「繊維 to 繊維」の実現に向けて
今回の成果でケミカルリサイクル法による「ボトル to ボトル」の大幅なエネルギー削減の実現が近づいたが、田中はあらたなターゲットを既に見据えている。それが、PETなどを原料として作られ、多くの衣類に使われているポリエステル繊維の分解だ。
衣類は大量に生産され、その多くが短期間で廃棄される。衣類の多くに使われるのがポリエステル繊維だ。PETを主な原料として作られるポリエステル繊維は、世界でおよそ6000万トン製造されている。繊維業界においても炭素の排出量を実質ゼロにする目標「カーボンニュートラル」が求められるなか、衣服のリサイクルは重要な課題だ。今回PETボトルで開発したケミカルリサイクルの技術は衣服のリサイクルにも貢献できると見込んでいる。
ポリエステル繊維は、PETだけを原料とする無色透明なPETボトルとは異なり、衣類としての機能性やデザイン性を高めるために、染料を用いたり他の繊維と複合させたりして使われていることがほとんどだ。着色された複合繊維からPETの成分を選別して分解するにはPETボトル以上に高度なケミカルリサイクル技術の確立が求められる。
例えば、触媒のリチウムメトキシドは水と反応すると分解してしまう。衣類は乾燥している状態でも少量の水を含んでいるため、水分がリチウムメトキシド触媒と反応しないように事前に衣類の水分を完全に乾燥させる必要がある。このように多くのエネルギーが必要な工程があると、リサイクル技術としてはまだ不十分だ。だが、この挑戦的な課題に田中は前向きだ。
「触媒の基礎研究はきれいな試薬からスタートして、だんだん混ざったもの複雑なものになっていくのですが、PETボトルや繊維のリサイクルはそれとは逆で、混ざったものからスタートし、きれいなものを取り出す。実用的な研究の面白さを感じています」
着色された複合繊維からPET成分を選別して分解するのが次の課題の一つだ
実験化学の成果を社会で実際に役立つものにするには、化学プラントなどの大型設備投資が必要で、スタートアップ企業などの新規参入が難しいのが現実だ。最近のデジタル関連分野の人気から、化学の道を志す学生も減っているというが、次の世代も見据えて田中はこう語る。
「化学実験系は辛い、きついというイメージが強いのかもしれません。そうだとすると私自身、現役の研究者として責任の一端があります。自分がリアルに実験をして見つけた『化学反応』で社会を変えていける、そんな夢のある分野だということを伝えていきたい。そのためにも、いつか自分の見つけた化学反応で起業することも視野に入れ、社会課題を解決するような挑戦をしたいです」
触媒化学融合研究センター
ケイ素化学チーム
主任研究員
田中 真司
Tanaka Shinji