常識外れの技術シーズが産業競争力の源泉となるニーズと結びついた!
常識外れの技術シーズが産業競争力の源泉となるニーズと結びついた!
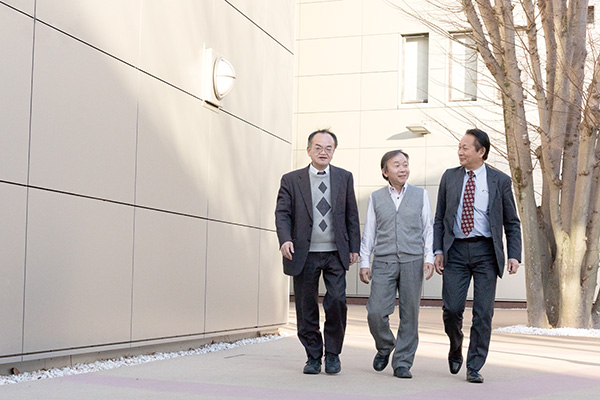
2018/03/31
常識外れの技術シーズが産業競争力の源泉となるニーズと結びついた! 産総研の技術が半導体チップの生産効率向上にマッチング
産総研が開発した、焼かないで緻密なセラミックス膜をつくる技術「AD法」をTOTOがニーズを探してマッチングさせ、事業化に成功した。
セラミックスといえば焼き固めてつくるものだと考えられていたが、1994年に産総研が室温でセラミックス膜ができる現象を発見して以来、常識は覆った。そこから焼かずにセラミックス膜をつくる技術「エアロゾルデポジション法(AD法)」が生まれ、この技法は2011年、TOTO株式会社によって半導体製造装置のコーティング技術として実用化された。高機能なコーティング技術は半導体の生産効率を劇的に向上させ、現在、世界シェアのトップを占めるに至っている。共同研究から事業化、そしてアライアンス発足までの歩みを追った。
セラミックスが常温で固化する常識外の技術
明渡最初にエアロゾルデポジション法(AD法)について簡単に紹介しておきましょう。AD法とは乾いたセラミックスの粉を空気と混ぜて攪拌し、ガスとともにノズルで吹き付けることで、基材の表面に緻密なセラミックス膜をコーティングする技術です。セラミックスといえば普通は焼き固めてつくるのですが、AD法では一切焼くことなく、室温で厚さ500 μmのツルツルで堅牢な膜をつくることができます。
AD法によるセラミックス膜の断面写真。緻密なナノ結晶構造を形成し、基材に食い込むアンカー部があるため、高い密着力がある。
1994年ごろ、私はセラミックス微粒子を基板上に堆積させ、厚さ1 μm以上の圧電膜の実用的な製膜法を実現しようとしていました。セラミックスの粉を基板に吹き付けて加熱したり、プラズマなどで溶かして融着させたりなど、いろいろな方法を試していましたが、なかなかうまくいきませんでした。そんなあるとき、誤って微粒子を加熱せずにそのまま基盤に吹きかけてしまいました。すると基板に黒い汚れのようなものがカチカチに固まって付着していたのです。尖ったピンセットの先で強くこすってもまったく剥がれません。それが何なのか気になって調べてみたところ、有機物の汚れなどではなく、セラミックスの粒子が常温で固化したものだということがわかったのです。そんなことがあるのかと衝撃を受けました。後にこの現象を「常温衝撃固化現象(Room Temperature Impact Consolidation:RITC)」と名付けました。
そこから、その現象を利用して堅牢なセラミックス膜をつくるコーティング技術の開発をスタートさせました。97年に論文発表、学会発表をしたのですが、それを聞いて、すぐに訪ねて来られたのがTOTO株式会社の清原さんでした。実は、この出会いのきっかけは、当時、同じ工業技術院・九州工業技術研究所(現 産総研・九州センター)に在籍していた野中一洋さん(現 イノベーションコーディネータ)が、98年にスイスで開かれた強誘電体応用の国際会議(ISAF-11th)で、私の発表を見て面白いと思っていただき、同じ大学出身で以前から知り合いだったTOTOの清原さんに、AD法のことを紹介してくれたことに端を発しています。私自身はセラミックスの専門家ではなかったので、セラミックスのプロが見て何と言うのか、とても興味があったことを覚えています。
清原私は大学以来35年間、ずっとセラミックスを研究してきました。TOTOではトイレなどの水回り製品のきれいな状態が長持ちするように、表面を焼いて滑らかにしたセラミックスを用いていますが、1990年代には表面をコーティングする技術が重要になると考え、新しいコーティング技術の開発を始めていました。99年にはトイレの新しい防汚技術、セフィオンテクト技術(新釉薬技術)を開発しましたが、AD法を知ったのはちょうどそのころでした。
明渡さんのところに伺って、実際にAD法を見せていただいて驚きました。通常の低温でつくるセラミックスと膜質がまったく違う、これはすごい、と。また、セラミックスの場合、低温でつくるといっても普通は100 ℃以下という程度のことで、常温で固化するなど考えられません。そんなことができるなど思ってもいませんでした。
明渡低温でセラミックス膜をつくる場合、樹脂とセラミックスを混ぜて塗る方法がありますが、それだと樹脂が混ざるので、ツルツル、カチカチしたセラミックスらしい表面にはならないのです。しかしAD法を用いれば、焼結する場合と遜色のない表面がつくれます。清原さんはその点にも驚かれていました。
清原新しいコーティング技術を探していたところだったので、すぐに、一緒にやりましょうとお話ししました。実質的には翌週からもう動き出していましたね。
明渡やはり専門家でも聞いたことのない常識外れの技術だったわけです。その後TOTOの基礎研究所で講演をさせていただき、共同研究する価値があると判断していただきました。
佐伯私は現在、産総研に所属していますが、もとはTOTOの基礎研究所で、光触媒技術の研究者と共同研究をして事業化につなげるなど、基礎から応用に至る一連の研究を担当していました。清原さんがAD法に注目した当時は基礎研究所の所長を務めており、AD法の実用化プロジェクトもTOTO側で進めていました。そのキャリアを評価していただき、退職後は、産総研で先進コーティングのアライアンスを担当しています。
私はこの技術に、膜の緻密さの他にも魅力を感じたのです。当時は企業にも地球環境問題への対策が求められるようになってきた時代でした。セラミックスは1500~1600 ℃という高温で焼いてつくるため、窯業のエネルギー消費量は多く、企業として肩身の狭い思いをしているところもあったのです。AD法は常温ででき、非常にエネルギー消費量が少ない製法なので環境効率が20倍にも上ります。私たちとしてはその点でも願ってもいない技術といえました。
実用化には原理の解明も重要だった
清原新しい表面改質技術の開発を目指して共同研究がスタートしましたが、私たちは基礎的な技術ではなく、量産化のための技術や装置をつくらなくてはなりません。産総研の装置では小さい膜しかつくれていませんでしたので、まずは大面積化する技術を開発する必要がありました。
それに、セラミックスが常温で固化する現象に再現性があることはわかっていましたが、なぜそれが起こるのか、他のセラミックス膜とはどのように性質が異なるのかなどということについては、まだ明らかにされていませんでした。企業としては、膜の生成メカニズムやAD法の膜ならではの性質がわからないままでは実用化に踏み切ることはできません。量産化技術は私たちがつくるので、明渡さんには原理の解明をしていただきたいとお願いをしました。
明渡現象を見つけた私自身の興味とTOTOさんの要請もあり、研究資金の乏しい中、メカニズム解明のための研究を進めたところ、セラミックスの微粒子が高速で基板に衝突することで結晶の粒子が壊れ、壊れたことで粒子が活性化されて再び結合しようとする働きが起こり、その結果、より細かい粒子同士が再結合して膜となる、という現象が起こっていることが明らかになりました。
加熱して固化させる従来の方法では、もともとのセラミックス粒子表面の原子が熱拡散によって移動し、くっつきあって粒子間の隙間を埋め、大きな結晶に成長するので、結晶サイズは数μm以上になります。しかし、AD法によってできた結晶は、一度破砕した粒子がくっつき合ってできるので、5~500 nmと、非常に小さくなることが特徴です。結晶が小さいので、より緻密で堅牢な膜となるということがわかりました。後に、これらの研究は2つの国家プロジェクトで進められましたが、原理が完全にクリアになるまでに5年ほどかかってしまいました。
佐伯技術をつくることと製品をつくることは別物で、技術ができたというのは「製品がつくれる可能性がある」という段階にすぎません。実用化までの長い開発期間のなかで、研究がこのレベルまで進んだら次はこのようなトライアルをするという、指標のような段階がいくつかあるわけですが、その中で特に難しいのは、よいものをいかに均質につくるかという品質管理の部分です。AD法を世の中に出していく上では、どの工場でつくっても同じ品質の製品になることが大切です。だからこそAD法のメカニズムの解明をしていただき、なぜこの技術に価値があるのかを明らかにしていただく必要がありました。
明渡原理や性質・価値を掘り下げて研究し、それらをクリアにした上で応用展開していく。企業との共同研究により実用化までの一連の流れを知ることができ、その中で技術開発のベンチマークを積み重ねることができたのは、私としても刺激的で貴重な体験でした。
出口を模索し半導体分野に行き着いた
明渡国家プロジェクトとして進めていく上では、常温でセラミックス膜をつくる技術をどのような製品として展開していけるかという、出口の提案が必要になります。当初は数多くの企業から、低温プロセスという点と成膜コストの点で競争力のありそうな電子デバイス応用の提案があり、さまざまな出口製品に向け開発を進めました。「世界初」や「世界最高性能」の試作デバイス開発にも成功したのですが、プロジェクトが終わった後、企業の方でさらに製品化に向け検討を進めていくと、具体的なビジネスとして競合する製品との比較や顧客価値評価の面で、実用化につなげることは、なかなか難しいということがわかってきました。
清原基礎研究が商品化されるまでには「魔の川」や「死の谷」があるといわれますね。技術ができても「Quality(品質)」「Cost(費用)」「Delivery(引渡し)」という「QCD」が満たせないと商品にはならず、この関門を超えていくのが難しいわけです。
もともと私たちはトイレなどに用いるコーティング技術を探していたわけですが、AD法をトイレや洗面台などの水まわり製品に用いるのは、やはりコストに見合うとはいえませんでした。ではどこに応用していけばよいかと有効な出口を探し、見つけたのが半導体分野でした。もともと当社には半導体製造装置用のキーデバイスを扱うセラミック事業部があり、半導体製造装置のコーティング技術として製品化していくことでビジネスとしても成り立たせることができるのではないかと考えました。
また、焼き物であるセラミックスは材料の組成や構造で特性が変わることが知られていますが、セラミック材料をコーティングする溶射法などは構造まで制御している技術ではありませんでした。 AD法は微細な構造を制御して高品質な膜質をつくる技術であるという点が、半導体業界のトレンドに合っていると考えられました。
佐伯新しいものをつくって世に出していく場合、ニーズが先か、シーズが先かという問題がありますが、重要なのはニーズとシーズのマッチングであり、シーズ側がいかに数多くニーズ側と接点をもてるかどうかが勝負になると思います。そのため私はTOTOでセラミック事業部長になったときに、お客様の困っていることに対して技術を用いてソリューション提案をしていく方針を打ち出しました。
そのような中でニーズとして上がってきたのが、半導体製造装置で発生する塵の問題でした。半導体チップというのはシリコンウェハの上に薄膜を形成し、それを装置内で発生させたプラズマで削って微細なパターンをつくっていくものなのですが、プラズマによって、チップだけではなく装置の内壁まで削れてしまい、削りカスが発生して困っているというのです。
半導体チップのパターンは非常に微細なため、発生したカスが半導体チップに付着すると製品として成り立たなくなるわけですね。これまでも装置の内壁は削れないようにセラミックコーティングしてありましたが、決して万全ではなく、装置メーカーも、さらにはその先のユーザーである半導体メーカーも歩留まりを向上させるため、もっと削れにくくカスの出ないコーティング材を探していたのです。そこで2006年、AD法をこのターゲットに適用させるための研究開発が始まりました。
明渡具体的にどのぐらいの低発塵性能が求められるのか、また、AD法の膜でどこまでの結果が出せるのかは、その時点では明らかになっていませんでした。TOTOさんは辛抱強くメーカーとやりとりを重ねて、必要な仕様を見出していきました。
清原実はその当時の半導体チップのパターンの幅は70~80 nmで、その時点では削りカスの方がずっと小さかったので、発塵の影響はそれほど出ていませんでした。しかし、半導体の技術ロードマップでは、それまでの10年間でその線幅は4分の1のピッチまでパターンの微細化が進んできたことから、今後削りカスによって生じる生産性の低下が深刻な問題になることは明らかでした。そこで、私たちは2011年に照準を合わせ、AD法によるセラミックス膜の製品化に取り組むことにしました。
明渡新しい技術を製品に使うことにはリスクがありますが、そこに踏み切られたことが素晴らしいと思います。
佐伯お客様の課題を解決する技術を先取りし、オンリーワンの製品をお客様に届けることを重視していたためにできたことだと思います。ソリューション提案の過程で、どの程度のスペックが必要なのかを、装置メーカーから具体的に教えていただけたことも大きかったですね。
AD法の実用化に向けて
佐伯AD法はまったく新しい技術なので、お客様に使っていただくには、この技術の価値をわかりやすく伝える必要があります。そのためには価値の定量化、数値化をすることが不可欠であり、私たちはAD法による大面積の成膜技術の開発に加えて、製品の機能性評価技術の開発にも取り組んでいきました。
明渡TOTOさんが評価のために使ったのはイットリア*1という材料ですが、イットリアの緻密体をつくる技術は従来もありました。そこで、従来の手法でつくった膜とAD法でつくった膜を比較するために顕微鏡で拡大してみたところ、従来の膜にはポア(穴)が見えたのに対し、AD法にはまったくポアがなく、非常に緻密な膜であることがはっきりわかりました。
清原同時に、半導体製造装置の中でどのように削りカスが出てくるのか発塵のメカニズムも探ったところ、コーティング材はポアを起点として脱落を始めていたことが明らかになりました。ということは、ポアのないAD法はこの用途に非常に向いていることになります。これなら従来品に勝てるのではないかと思いました。
装置メーカーのお客様にこの方法を提案したところ、「こんな答えがあるなんて想像していなかった」と驚かれました。この時点ではお客様の装置で発塵がどの程度発生するのかわかっていなかったのですが、評価データを示したことでお客様に測定していただけることになり、測定結果が出てから、開発は一気に進み始めました。
佐伯自分たちの技術をオープンにしたがらない企業も多いのですが、オープンにしないとお客様に信頼していただくことはできません。ここではオープンにしたことで私たちの提案が理にかなっていることをご理解いただき、信頼していただくことができました。
AD法による半導体製造装置向けのコーティング部材は2011年に実用化できましたが、さらに私たちは装置メーカーの先にあるニーズをキャッチアップしたいと、半導体デバイスメーカーにもこの技術の価値を伝えました。そもそも半導体製造装置の発塵で困るのは、装置メーカーというより、装置を使う半導体デバイスメーカーなのです。半導体デバイスメーカーはご存知の通り日本の企業ではありませんが、当社の九州工場まで視察にこられました。半導体メーカーとの協業が始まったことで、いよいよビジネスとしても本格的に動き出しました。
明渡新しい技術の導入は、従来技術の改善とは違ってリスクが高いことなので、当然、企業は慎重になります。そのときにはこのように、サプライヤーとカスタマーが一緒になって開発していくプロセスが重要になると思います。これは産総研と企業との共同研究でも同じことですね。
清原半導体チップの進化とのタイミングに合致したこともあって、この製品は広く求められ、現在は世界トップのシェアを獲得しています。
AD法でコーティングされた半導体製造装置部材(写真 : TOTO株式会社提供)
アライアンスの設立で、さまざまな用途開発を
清原ロードマップでは2020年に7~8 nmピッチのパターンになるとされていましたが、実際はもっと進化は加速しています。この先も、これまで以上に低発塵コーティング材のニーズが増えることは間違いないでしょう。
現在はすでに産総研との共同開発は終わり、私たちは将来的なニーズに向けてAD法を独自に進化させているところです。しかし、AD法の成功を知った他の企業も、新たな技術開発を進めてきています。私たちも今後のニーズをキャッチアップしていく中で、再び産総研と連携することもあるだろうと思っています。
明渡技術は直線的にではなくスパイラル状に進化していくので、基礎研究に立ち戻る必要も出てくるでしょう。基礎研究と応用研究を行き来することで、基礎研究を実用化に結びつけていきやすくなると思います。
お客様が欲しいと思う機能に対して、なぜその機能を求めるのか、その機能をどのような工程で実現することが必要なのかについて原理から考え、さらにその先にいる顧客まで視野に入れてトータルに開発に取り組まれたTOTOさんの姿をそばで見ていて、私自身、非常に勉強になりました。
また、TOTOさんの成功により、これまでこの技術に無関心だった企業にも、使える技術だと広く認識してもらえるようになりました。現在はAD法を実用化につなげたい企業が集まる先進コーティング・アライアンスを発足させ、共同開発を進めていくための体制づくりを行っています。
佐伯産総研発の先進コーティング技術に対してさまざまな要望をもった企業が集まるアライアンスでは、さまざまな仮説を立ててニーズとシーズをマッチングさせ、それぞれの企業が仮説を持ち帰って個々に開発を行うというかたちで進めています。その中からさまざまな製品が生まれてくるでしょう。
明渡現在、積水化学工業株式会社でフィルム型色素増感太陽電池の事業化が始まっていますが、それもこのような流れの中から出てきたものです。そのほかに、スマートフォンの筐体や液晶カバーへの応用も進められています。知財面など難しい点もありますが、将来の技術課題を見据えながらAD法の価値を向上させ、使い尽くしていけるようにと考えています。この技術の本当の価値が見えてくるのは、これからだと思っています。
これからの共同開発に必要なこと
清原当社では半導体事業が成功し、私もその仕事によって2017年秋に当社初のフェローに就任しました。ここまでの成功のベースには、私たちと明渡さんとの信頼関係がありました。興味をもった技術シーズを気軽に試させていただけたことは、技術開発の上でとても重要なことでした。技術は常に進歩していますから、企業は研究者と常にコミュニケーションをとって情報をキャッチアップしていくことが必要です。自分のモノサシを持って、それを常に磨いていくことで、新しい技術が素晴らしいものかどうかがわかるわけです。
明渡自分のシーズにどれだけの価値があるのか、企業が求める性能がだせるのか、シーズの使い道や可能性を予測して企業とコミュニケーションを取ることが必要だと学びました。私も、清原さんや佐伯さんと事業化を進める中で育ててもらって、このスキルが身についてきたように感じています。
清原研究者にはシーズをオープンにしていただくだけでなく、使い道を提案していただくことが必要だと思います。
明渡そうですね。実は、ここ10年ほどは年間100件以上の連携のお話があるのですが、話を聞いてみると具体的に出口・製品応用のアイデアを持っている企業はそう多くありません。しかし、どのようなことをしたいのか詳しく聞くことができれば、AD法でなくても、そのニーズにふさわしい別の技術を紹介することができます。コミュニケーションをスムーズなものにするためにも、企業の方には出口の情報をお持ちいただけるとうれしいです。企業側の出口と研究者側のシーズの使い道が合わされば、課題設定や実用化までのプランが明確になります。この技術に少しでも興味があれば一度声をかけてください。目指す出口に向かって、ともに努力したいと思います。
*1: イットリア。耐プラズマ性に優れている材料のため、半導体製造装置の内部部材へのコーティングとして利用されている。溶融状態で反応しやすい金属からセラミックスを保護する。[参照元に戻る]
先進コーティング技術研究センター
センター長
明渡 純
Akedo Jun
先進コーティング技術研究センター
実用化支援チーム
プロジェクトマネージャー
(元TOTOファインセラミックス株式会社・代表取締役)
佐伯 義光
Saeki Yoshimitsu
TOTO株式会社 総合研究所
副所長 兼 素材研究部
部長
フェロー
清原 正勝
Kiyohara Masakatsu
産総研
エレクトロニクス・製造領域
先進コーティング技術研究センター
- 〒305-8565 茨城県つくば市東1-1-1 つくば中央第5
- act-webmaster-ml*aist.go.jp
(*を@に変更して送信してください)
TOTO株式会社 総合研究所