独立行政法人 産業技術総合研究所【理事長 吉川 弘之】(以下「産総研」という)先進製造プロセス研究部門【部門長 神崎 修三】は、東陶機器株式会社【代表取締役社長 木瀬 照雄】(以下「TOTO」という)総合研究所【所長 佐伯 義光】と共同で、エアロゾルデポジション法(以下「AD法」という)を利用して、サブミクロン粒径のα-アルミナ微粒子を基材に吹き付け、焼結することなく常温で金属基板上に固化させ、バルク焼結体と等しい電気機械特性を持つ1µm( 1マイクロメートル:100万分の1メートル)以上のセラミックス厚膜を形成することに成功した。また、産総研では、この様なα-アルミナ微粒子の常温固化によるセラミックス厚膜の形成は、α-アルミナ微粒子が基材に吹き付けられた衝突時の温度上昇による表面熔融ではなく、粒子の破砕現象による微結晶粒子の変形と新生面形成による表面活性化が支配的である事を明らかにした。表面の硬さや耐薬品性などの表面機能を主に用いる窯業製品において、従来必要とされてきた1000℃以上の焼結工程を必要としなくなり、飛躍的な省エネルギー効果が期待できる。
TOTOでは、200mm四方の面積に均一な製膜を実現【図1参照】しており、実用化の対象として、液晶パネルや半導体などの製造装置部品や、電子基板などへの応用を検討している。
この様なAD法を利用したセラミックス微粒子の常温固化によるセラミックス膜の形成は、常温衝撃固化現象と名づけられ、これまでも産総研で圧電セラミックス材料であるPZT(チタン酸ジルコン酸鉛)などで確認されてきた。
産総研とTOTOは、共同で研究を推進し、原料微粒子の粒径分布、機械特性に注目し詳細な検討を重ねたところ、α-アルミナ微粒子の常温固化によるセラミックス厚膜の形成に成功し、バルク焼結体に相当するビッカース硬度やヤング率、絶縁破壊強さ、体積抵抗率、誘電率を達成した。形成された膜は緻密でナノスケールの微結晶組織になっている【図1参照】。
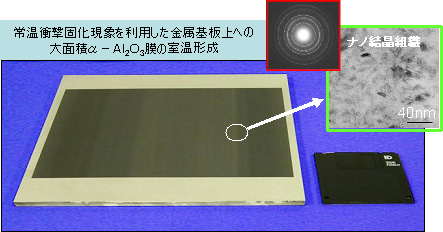
|
図1 エアロゾルデポジション(AD)法により金属基板上に常温(室温)形成されたα-アルミナ(Al2O3)厚膜とその結晶組織。
右上のリング状のパターンは、形成された膜の電子線回折像で、膜が周期的な結晶構造をもっている場合に現れる。膜がアモルファス(非結晶質)で無いことの証明。
|
一般にセラミックス材料は1000℃以上で焼き固める(焼結)のが常識であり、このため融点が低い金属やガラス、プラスチックとの複合化、集積化が困難で、セラミックス電子部品の高性能化や構造部品の軽量化の大きな課題となっていた。これまでもエネルギー消費の低減や金属、ガラス材料などと集積化することで新しい機能部品を実現するため、この焼き固める温度(焼結温度)を下げる試みが様々な研究者の間で検討されている。
この焼結温度を下げるには、1000℃以下の温度で熔融結合を促進する材料(焼結助剤)をセラミックス原料に添加したり、セラミックス原料粒子径をナノオーダーまで微細化することが検討されてきたが、一般に焼結温度の低減は、900℃程度が限界であった。また、多くの場合これらの低温で焼結した低温焼結体の特性は従来の高温で焼結した焼結体に比べ、密度は低く、機械的に脆い、絶縁性が低い、耐蝕性が低いなど、その電気的、機械的、化学的特性は劣っていた。
産総研 先進製造プロセス研究部門では、AD法を利用したセラミックス微粒子の常温固化によるセラミックス膜の形成に関する研究を、5年前の旧工業技術院 機械技術研究所の時代から、微粒子衝突によるセラミックス材料のコーティング技術として研究開発がなされた経緯があり、このとき圧電セラミックス(PZT)材料で金属、ガラス、シリコン基板上に緻密かつ高透明、高密着力の膜が形成できることを見出し、常温衝撃固化現象と名づけていた。
本研究開発は、主にこの旧工業技術院 機械技術研究所時代の研究成果を基にし、独立行政法人 新エネルギー・産業技術総合開発機構【理事長 牧野 力】(以下「NEDO技術開発機構」という)が、経済産業省からの交付金を原資として実施する「エネルギー使用合理化技術戦略的開発/エネルギー有効利用基盤技術先導研究開発」事業の「衝撃結合効果を利用した窯業プロセスのエネルギー合理化技術に関する研究開発」として、NEDO技術開発機構の委託契約に基づき、窯業製品における機能向上、省エネルギープロセスの実現を目指し、平成13年度から3年間にわたり産総研とTOTOが共同実施してきた成果である。現在、NEDO技術開発機構が、経済産業省からの交付金を原資として実施する、「ナノテクノロジープログラム/ナノ加工・計測技術」に係る「ナノレベル電子セラミックス材料低温成形・集積化技術(平成14~18年度)【プロジェクトリーダー 産総研 先進製造プロセス研究部門 集積加工研究グループ長 明渡 純】」プロジェクトの中でさらなる応用展開を推進中である。
今回の研究で産総研は、高分解能透過型電子顕微鏡(HR-TEM)による膜の微構造解析、微粒子衝突の計算機シミュレーション、製膜効率の評価や原料粒子の圧縮破壊強度測定などを実施し、サブミクロン粒径の原料粒子(α-アルミナ微粒子)は、基板上に吹き付けられた衝突時の温度上昇による表面熔融を殆ど経ないで、10~30nm(1ナノメートル:10億分の1メートル)前後の微結晶粒子に破砕・変形され緻密なナノ結晶組織【図1、2参照】のセラミックス厚膜が形成されること、また、破砕時に形成された新生面による活性効果が粒子間結合に対し支配的に働くことをつきとめた。【図2】はこの微結晶粒子破砕の様子を実験的に確かめた結果である。鉛などの重い元素を含むPZT(圧電材料)とアルミと酸素などの軽元素からなるα-アルミナ微粒子を混合して基板に吹き付け、常温でPZT/アルミナの混合膜を形成、これを電子顕微鏡(TEM)で組織観察すると、重い元素を含むPZTは黒く、軽い元素からなるアルミナは白く写り、膜内に存在する二つの材料の分布が明るさの違いとして観察できる。この結果、【図2】の左側の断面TEM写真にあるように基板面に平行な方向(基板衝突方向と垂直)に黒い層状のPZTの領域が観察され、この部分の領域がほぼ原料粉末の大きさに一致した。また、このとき膜内の変形した各原料粒子の領域内にも【図1】のTEM写真にあるような粒子径20nm前後のより微細な結晶組織が観察される。以上のことから、【図2】右側のモデル図にあるようにPZTの粒子は基板や膜表面への衝突で破砕・変形し、結晶組織が微細化していることが明らかになった。このため形成されたセラミックス膜は、常温でアモルファス相を殆ど含まないナノサイズの結晶構造体となる。また、この様なAD法を利用したセラミックス微粒子の常温固化によるセラミックス膜形成(常温衝撃固化現象)は、限られたセラミックス材料だけで生じるものでなく、セラミックス回路基板材として注目されている窒化アルミや超伝導材料でもある二硼化マグネシウムなど、窒化物、硼化物などの非酸化物系セラミックス材料でも生じる普遍的な現象であることを明らかにした。
そこで産総研とTOTOは共同し、上記製膜モデルに基づいて原料粒子の凝集を抑え、純度、圧縮破壊特性、製膜条件を検討し、高温(1300℃以上)でしか焼結できない99.9%純度のα-アルミナ微粒子を焼結助剤や有機バインダー(結合剤)など一切の添加剤を用いず、常温で固化することに成功した。ビッカース硬度:1500~2200Hv、ヤング率:300~350GPa、絶縁破壊強さ:150~300kV/mm以上、体積抵抗率:1.5×1015Ω・cm、誘電率(ε):9.8を達成し、世界で初めて、常温プロセスでバルク焼結体に等しい電気機械特性(バルク焼結体値では、ビッカース硬度:1400~2000Hv、ヤング率:350~380GPa、絶縁破壊強さ:10kV/mm以上、体積抵抗率:1.5×1015Ω・cm、誘電率(ε):9.9~10)のセラミックス厚膜を形成することに成功した。また、セラミックス厚膜はポア(気孔)がなく簡単な研磨を行なうと数nmレベルの平滑性も得られている。TOTOでは、プラズマ耐蝕性の開発にも取り組み200mm四方の面積への均一な製膜【図1参照】にも成功した。
本研究開発では、窯業プロセスで一般的に用いられる安価なサブミクロン粒径のα-アルミナを原料粒子として用いながら、従来必要とされてきた1000℃以上の焼結工程を必要としなくなり、同時に高温焼結されたバルク焼結体と同等の硬さや電気特性を実現、また、ナノレベルでポアのない緻密性や平滑性を得ることに成功した点で画期的なプロセスと言える。
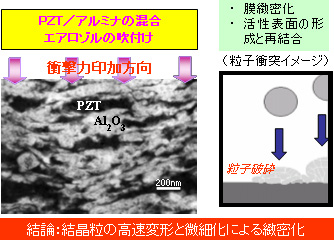 |
図2 エアロゾルデポジション(AD)法により形成されるPZT/アルミナ混合膜微細組織と粒子破砕による膜緻密化メカニズムのモデル
|
焼結せずに緻密なセラミックス部品が作れるため、焼き縮みなどの問題がなく、金属部材やガラス材料と高精度な集積、一体化が容易になり、様々な分野への応用展開に結びつくと考えられる。例えば、半導体関連産業や電子部品産業では、絶縁材料や高周波誘電体材料など電子セラミックス部品の回路基板との一体化、部品点数の削減などが強く求められており、本プロセスは携帯電話やパソコンなどの高速化、小形、低コスト化に繋がると期待される。
また、現在、研究開発が活発なMEMS(微小電気機械システム)などの分野で、プロセス温度の低減により、圧電セラミックスなど機能性酸化物材料を既存の半導体微細加工(Si微細加工)プロセスに導入でき、大幅な機能向上が図れると期待され、その実用化に弾みをつけると考えられる。この様な電子セラミックス分野への応用展開は、現在進行中のNEDO技術開発機構のナノテクノロジープログラム/ナノ加工・計測技術「ナノレベル電子セラミックス材料低温成形・集積化技術」プロジェクトの中で推進していく。
さらに、従来技術をはるかにしのぐ密着性と緻密性、平滑性が得られるため、耐磨耗性コーティングとして、機械、航空、エネルギー関連分野に、また、生体適合性セラミックス材料の金属部材コーティングを通して、耐久性の高い人工関節や生体インプラントの開発など医療関連分野などに結びつく可能性もある。
以上のような用途に対して、産総研 先進製造プロセス研究部門では、窯業プロセスにおける高効率化、高機能化の実証を目指して、引き続き研究開発を進める予定である。
一方、TOTOでは、まず液晶パネルや半導体の製造装置部品として静電チャックやプラズマ耐蝕性の高い部品の高機能化を図り、実用化、製品化を予定している。