ものづくりは次のステージへ
ものづくりは次のステージへ
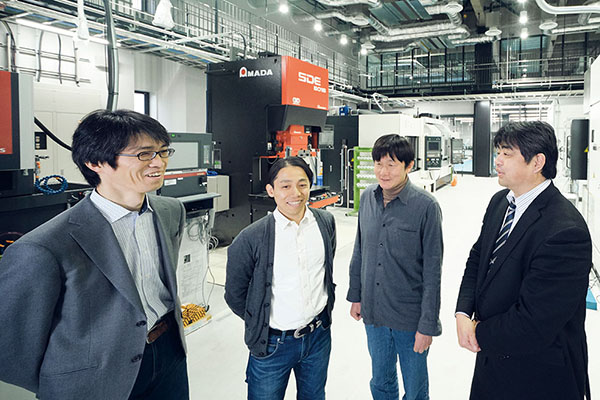
2019/04/30
ものづくりは次のステージへ人と機械が協働する次世代の製造現場を目指して
サイバーフィジカルシステム研究棟の1階に、「工場」を模した空間がある。ロボットが製造ラインで組み立てを行い、製品が自動で移動し、さまざまな加工機械が並んでいる。産総研がつくりあげようとしている未来の製造現場は、人とロボットはいかに協働していくべきなのか、AIをどのように活用すべきなのか、 IoTによって工場のネットワーク化はどう進めるべきか、などの技術をトータルで実証・実験するプラットフォームとなる。企業とともに未来の工場を模索、追求し、日本のものづくり再興を目指す。
人とロボットが協働して日本の製造業を支える
谷川サイバーフィジカルシステム研究棟にどのような模擬環境を設置するかを決めるにあたり、「労働生産人口減少により影響が大きい産業の環境」を解決すべき課題の一つとして掲げました。製造工場も近い将来直面する課題です。
工場の代表ともいえる自動車工場は特定の車種を大量に生産するため、ロボットによる作業の自動化が進んでいます。一方、部品等の製造工場では、事業の性格上、多品種少量生産が主流になっており、人間が工程を担う「セル生産方式」が採用されています。しかし、労働生産人口が減っていく中で、将来的に人の力に頼るわけにはいきません。すでに人手不足の影響が出ている現場もあります。そのような状況を踏まえ、この模擬工場では、まず、ロボットと人間が効果的に協働する仕組みを考えていきます。これまでの工場ではロボットと人間は別の仕事をしていましたが、これからは人間のフレキシブル性と従来のパワーに加え、多様な動きができるようになったロボットをどのように組み合わせていくかが重要となります。
また、加工機などを使いこなす熟練した職人たちの高齢化により、製造現場から「匠の技術」が失われつつあり、AIを活用し、彼らの技術を後世に残し、伝える仕組みをつくっていきます。
さらに、1工場で1つの製品の生産を完了させるのではなく、複数の工場をネットワーク上でつないで多品種少量生産に適応していく新しいダイナミックな生産体系、すなわち「つながる工場」の仕組みづくりにも取り組み、この模擬工場で実証実験を進めていく予定です。
これらの研究開発には、ロボットや加工技術、そして人間の動きを計測する技術など、多様な技術が必要となります。まずは堂前さんから工場にロボットを導入していく場合の課題について話してください。
暗黙知をデータ化する技術を開発
堂前これまでの大量生産の現場では、ロボットは特定の動きだけをしていればよかったのですが、1人の作業者が1つの製品を組み立てる変種変量生産の現場では、ロボットは非常に複雑な作業を要求されることになります。
また、短期間で次々と新しい工程に移っていく環境の中で、人と機械が協働しながら組み立て作業を行えるようにするには、作業者の動きのデータを取り、人の作業をどのようにロボットに置き換えていくかを見極めていく必要があります。
さらに、これまでのロボットは据え置き型でしたが、今後は人の代わりに工場内を自在に移動する必要も出てくると思います。ロボット自体が移動できる状態で、いかに作業精度を上げていくか、また作業自体を計画していくかも課題となると考えています。
谷川加工技術のデータ化についてはどうでしょう。
澤田加工技術のデータ化にもまだ多くの課題があります。例えば、熟練者の技能をデータ化する場合、熟練者はどこを見て、何を計測し、そこからどう判断して制御パラメータを設定するのかといった暗黙知を明らかにしていく必要があります。それには、まず、どのようなデータを取るべきか、そのデータがどのようにアウトプットにつながっているのかを突き止めなくてはなりません。その上で、作業と製品品質の関係性もみていかなくてはなりません。
谷川つながる工場についてはどうですか。
澤田工場と工場、装置と装置間をネットワークでつなぎ、作業工程の情報などをやり取りしながら製品をつくる「つながる工場」では、ある工場のある装置でトラブルが生じても、すぐに工場内あるいは他の工場にある同じ役割を担う装置とつないでスムーズに製品を完成させる、というビジョンを描いています。とはいえ、ネットワークで工場や装置をつなげば、すぐに「つながる工場」になるわけではありません。最近の製造装置は製造に関するさまざまなデータを自動的に取得していますが、メーカーによってデータの種類も形式も違うので、まずはそれらのデータを一元的に管理する仕組みをつくる必要があります。ここの模擬工場にはあえて異なるメーカーの装置を揃え、データの扱い方を検証していきます。これは将来的に標準化にもつながっていくと考えています。
つながる工場モデルラボ
A、B、C各工場の機械の稼動状況は、ネットワーク経由ですべて把握でき、どこかの機械(例えばC工場M3 マシニングセンタ)に異常が発生した場合には、すぐに代替可能な機械(この場合、C工場の待機中のM5 マシニングセンタやA工場の休止中のM3 マシニングセンタ)を割り当て、工程の組み替えやスケジュールの再調整を行う。
谷川現場の加工技術のデータをつくるにも、人とロボットの協働方法を見出すにも、作業者の動きの正確な把握が必要です。人間の動きの計測や解析は、どのように進めていくのですか。
多田工作機械やロボットであればセンサーを機器に組み込み、そこから情報を取得できますが、人の動きを計測するのは簡単ではありません。私は模擬工場を活用して信頼性の高い人間のデータを取る技術を開発し、その場にいる人間の動作をコンピュータ上に再現したいと考えています。
そのためには製品をつくる作業の流れの中で作業者の一連の動きを計測したり、非熟練者から熟練者までさまざまなレベルの作業者の動きや力のかかり具合などのデータを取得して、解析していく必要があります。現在は十数個のセンサーを作業者につけてもらう必要がありますが、将来的には少ない数のセンサーで人間の運動の計測・解析ができる技術も開発し、精度の検証も進めていく予定です。この動作分析は、人材育成プロジェクトの一環としても考えており、企業や大学の方々にきていただいて育成カリキュラムを実施し、その中でデータを集めていくことを検討しています。
また、人とロボットが協働するためには、データを後から解析するのでは間に合わないため、その場でリアルタイムに計測・解析する技術をつくる必要もあると考えています。
製造現場でAIをどう活用するか
谷川それぞれの技術領域で、AIはどう活用していけるでしょう。
堂前ロボットが物体を認識する部分にも、人とのインタラクティブなやりとりの部分にも、AIは広く活用できます。また、囲碁や将棋のAIが、人間では思いもよらない手を打ったりするように、製造現場のAIは人間が考えつかない効率的な工程、エラーが生じにくい新しい工程を生み出せるのではないかと期待しています。
多田人間の行動様式や認知様式などがデータ化されるということは、人間のフィジカルな情報がサイバー上で解析できるようになるということです。ある作業をするときに関節の角度はどう変化し、ねじりの強さや筋肉の張力はどの程度かということも把握できるようになれば、作業者が感じる負担も予測できるようになるでしょう。それはロボットが人と協働作業をするときに、負担なく作業できる環境をつくることにも役立てられます。これまでは数十人程度の作業者へのアンケート調査などから作業負荷を計測してきたのですが、将来的には工場で働く人にウェアラブルセンサーをつけてもらって、大規模にデータを取り、そこから人間の行動様式のモデル化につなげられると考えています。
谷川模擬工場から取れる多様なデータから、AIがさまざまな因果関係を見出すことで、1人あたりの生産力の向上につながる支援策をつくっていけるでしょう。また、工場全体を運用していく管理者への支援にも、AIは使われていくと思います。「もう少し人を雇おう」などの判断を行うのは人間ですが、AIはそのような経営判断のもととなる情報と解を提供できます。
澤田AIにより人間の作業予測ができるようになれば、工場で非熟練者などを対象に拡張現実(*1)技術を導入し、次の作業の指示を的確に行うようなことも考えられますね。
未来の工場の実現に向けて
谷川企業とともに研究を進めるこの模擬工場は、AIを実際の工場に入れていくという最終目的を目指し、企業とデータを共有しながら、どのようなビジネスに活用できるかを考え、導入モデルをつくっていきたいと思っています。皆さんはどうですか。
澤田「つながる工場」に関しては、将来的には工場同士、企業同士をつなげて、仮想的な生産ラインをつくる時代が来ると予想されます。この模擬工場と他県の公設試験研究機関などをつなげ、未来に向けた実験も進めていきたいですね。
堂前すでにロボットが人と同じ生産ラインの一部を代替している工場はありますが、人と環境を共有しながら、ロボットが新たにセル生産による組み立て環境をつくるような、未来のニーズに即した人と親和的に作業できるロボット技術をつくっていきたいです。
多田人間の運動計測に関する究極的な目標は、全国のあらゆる工場の作業者がウェアラブルセンサーを身につけ、各人の動きのデータをインターネット上で、リアルタイムに解析することです。それによって負荷の少ない働きやすい環境をつくることができれば、その技術は、人々の生活シーンにも応用され、住みやすい住宅や人が集まりやすいコミュニティをつくるためなどにも展開していけるでしょう。
谷川将来的には機械類の製造工場だけでなく食品工場のような超多品種を扱う製造現場も自動化していきたいですし、屋内から出て農業との連携なども考えていきたいですね。適用範囲を外に広げ、最終的には社会全体とつながることで、「Society 5.0(*2)」の実現も見えてきます。
堂前工場における人間とロボットの協働も、Society 5.0の実現につながっています。人とロボットの協働が可能になれば、その技術をオフィスや家庭にも広げて「ロボットと暮らす」を考えていけるようになりますからね。
澤田工場内には社会へ応用できる技術がたくさんあります。例えば工場内で部品などを自動走行車に乗せて運ぶ場合、作業者の安全確保が課題となりますが、安全は公共の場や家庭内などどのような場面でも重要で、工場内で安全を確立する技術は社会に応用できると考えています。
谷川この4月には産総研が中心となってコンソーシアムを立ち上げ、どのような研究をすべきか、どのように人材を育成すべきかなど、企業の方々と検討していきたいと思っています。皆さんも一言お願いします。
澤田考えるだけで手を動かさなくては、決して前には進みません。この模擬工場を、ぜひ皆様の思いつきを試す場にしていただきたいと思います。
堂前工場のノウハウは現場に集約されています。苦労されている課題などを共有し、協力して解決していきましょう。
多田人間の作業計測はまだあまり手のつけられていない分野です。製造現場における人間の動作に科学的なメスを入れて、動作分析を企業の方と一緒にしていければと考えています。
谷川これまで日本はものづくりで強くなってきましたが、現在は低迷し、将来的な人口減を考えると衰退の危機にあると言っても過言ではありません。これまで培ってきた技術を残し、さらに発展していくためには、各企業が連携し、情報を交換しながら、次世代の技術を積極的に取り入れる必要があると考えます。ぜひ産総研コンソーシアムを活用していただければと思います。
*1 Augmented Reality の訳。実在する風景(現実)にバーチャルの視覚情報を重ねて表示するこ とで、目の前にある世界を“仮想的に拡張する”というもの
*2 サイバー空間(仮想空間)とフィジカル空間(現実空間)を高度に融合させたシステムにより、経済発展と社会的課題の解決を両立する、人間中心の社会
人工知能研究センター
副研究センター長
谷川 民生
Tanikawa Tamio
人工知能研究センター
総括研究主幹 兼
つながる生産システム研究チーム研究チーム長
澤田 浩之
Sawada Hiroyuki
人工知能研究センター
オートメーション研究チーム
研究チーム長
堂前 幸康
Domae Yukiyasu
人工知能研究センター
デジタルヒューマン研究チーム
研究チーム長
多田 充徳
Tada Mitsunori