メタンからベンゼンを直接つくる!
メタンからベンゼンを直接つくる!
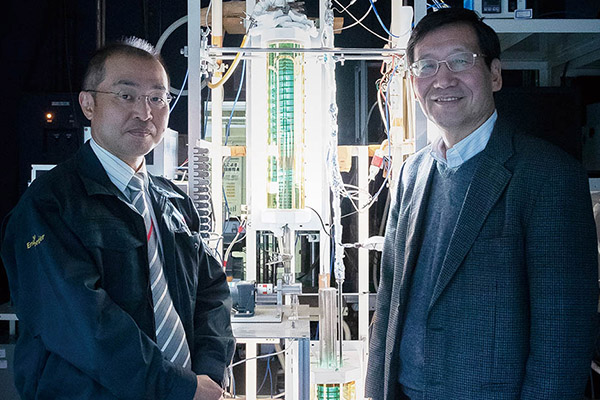
2019/01/31
メタンからベンゼンを直接つくる!ベンゼンの安定供給と完全国産化を推進
プラスチックや合成ゴムの原料となるベンゼンの世界的な不足が予測される中、産総研は石油を使わず、メタンから直接ベンゼンを得る、高効率な循環流動層プロセスを開発した。ベンゼンの安定供給と完全国産化を実現するこの技術は、今、実用化に向けて着実に歩を進めている。
社会に不可欠なベンゼンが足りない!新たな生成方法の模索が始まった
「ベンゼン」と聞いても、一般の人はそれがいかに重要なものか、ピンとこないかもしれない。しかし、ベンゼンがプラスチックや合成ゴムなどの原料であることを知れば、私たちの生活に必要不可欠なものであることが理解できるだろう。
ベンゼンは石油由来の基本原料の一つで、世界で年間4300万トン、日本国内だけでも年間400~500万トンが消費されている。しかし、近い将来、ベンゼンの供給量が足りなくなることはほぼ確実と言われ、欧米ではすでにベンゼン不足が始まっている。日本でも2030年頃から需要が供給を上回り、このままの状況が続けば、不足量はますます大きくなっていくと予測されている。
「その理由は、現在供給されているベンゼンのほとんどが石油からガソリンを精製するときの副産物だからです。世界の人口増加や経済発展に伴って、今後もベンゼンの需要が増え続ける一方、石油が安定的に供給され続ける保証はありません。また、世界的にハイブリッド車や電気自動車が普及し、ガソリンの消費量は減っています。そのうえ、日本の場合は自動車に乗る人も減少しているのです。使われないものはつくられない、ガソリンの生産量は減少し、連動してベンゼンの生産量も減ってしまうのです」
創エネルギー研究部門 炭素資源転換プロセスグループ上級主任研究員の張戦国はベンゼン不足の背景をそう説明する。現在は90 %以上のベンゼンが石油由来の方法でつくられており、ここ何十年もの間、世界中の研究者たちが石油以外の原料からベンゼンをつくる方法を模索し続けてきた。
その成果の一つに、石炭からベンゼンを取り出す方法がある。これはすでに実用化され、中国では試験的なプラントで生産されているが、プロセスの複雑さが課題になっている。石炭をいったんガス化してメタノールを合成し、さらにそれにメタノール転換技術を施し、結果として、エチレン、プロピレン、それにベンゼンの属する「芳香族」の成分を得る。そしてこの芳香族の中からベンゼンを分離・精製する。このような何段階ものプロセスを経てベンゼンをつくるのだ。
実用的な生産効率を達成するためには、単純なプロセスで生産できることが必要である。
1993年に、世界で初めてメタンからベンゼンを直接転換する方法(MTB反応)が報告されると、大きな注目を集めた。直接転換できることに加え、メタンの元となる天然ガス(シェールガスを含む)やメタンハイドレートは石炭より環境負荷が低いこと、また、石油に比べ、埋蔵量の豊富な天然資源であることも魅力的だった。この報告をもとに多くの企業が研究開発に参入したのだが、成果はなかなか出なかった。
産総研は2000年から研究をスタート
産総研がMTBプロセスの研究に着手したのは、報告から数年経った2000年のことだ。NEDOプロジェクトへの参加がきっかけだった。
「私たちは最初から実用化に照準を合わせ、そのために何が必要か、という観点から研究開発を進めました」と、張は当時を振り返る。
メタンをベンゼンに直接転換するには、酸素を含まない条件下で、メタンをモリブデン担持ゼオライトという触媒で反応させる必要がある。この触媒は細孔をもつ鉱物のゼオライトに金属のモリブデンを固定させたものであり、これを700~800 ℃まで加熱してメタンと反応させると、メタンをベンゼンと水素に転換できる。
研究チームはメタンと触媒を効果的に反応させる「流動層MTBプロセス」を考案した。炭素資源転換プロセスグループ長の倉本浩司はそのプロセスを次のように説明する。
「触媒のモリブデン担持ゼオライトの粒子を入れた容器の底に、気体は通しても粒子は通さないサイズの穴を開け、そこからメタンガスをゆっくり注入します。何もないと粒子は重力で下に溜まりますが、下から上に昇ってくるガスの力で粒子は浮き上がります。ガスの流速を調節すると両者の力は釣り合い、無重力のような状態が生まれて粒子はその空間で自由に動き回れるようになります。これを触媒粒子の流動化といいます。流動層の中ではガスの流れによって粒子は撹拌され、メタンと触媒をムラなく接触させることができます。その結果、良好な触媒反応が得られ、メタンからベンゼンと水素を効率よく製造できるというわけです」
基本的なプロセスはできた。しかし、実用化のためには、触媒の反応率をさらに30 %まで引き上げることが必要とされた。張らはそれを念頭に、さらに地道な改善を続けた。
触媒のバインダーフリー化で反応率が大幅に向上
触媒の反応率が低いままでは、よいプロセスがあってもベンゼンの収量は上がらない。反応率を高めるためには、触媒の流動性を高くしなければならない。そこで張は触媒をまとめるバインダー(接着剤)の存在に着目した。
「流動性をよくするには、触媒は丸い粒状であることが必要です。当初はバインダーを用いて触媒を丸く整形していました。しかし、バインダー成分は粒状触媒の40~60 %を占めることとなり、もともと反応率が低い上に、バインダーが半分もあったら、反応率はますます下がります。バインダーを使わずに触媒をつくれたら、それだけで反応率は上がると考えたのです」
触媒を使うことで生じる問題がもう一つあった。メタンが反応すると炭素が析出し、それが触媒の表面を覆ってしまい、活性を下げ、やがてMTB反応が進まなくなってしまうのだ。
「触媒が数時間で劣化するのでは、現実には使いものになりません。そこで触媒の長寿命化を目指し、炭素を触媒から効率よくかつ連続的に除去する方法を模索することになりました」
ここで張が取り組んだのが水素を使った触媒の再生方法の開発だった。化学的に考えれば、プロセスにメタンの代わりに水素を入れて反応させると触媒表面を覆っていた炭素は分解され、触媒が再び活性化するはずである。
2011年、産総研は企業との共同研究により、バインダーを使わない高性能触媒と、水素による触媒再生法を開発した。最終的な目標の反応率30 %まではまだ遠いものの、実用化の目処はつきつつあった。
二塔式の循環流動層プロセスで効率のよい連続反応が実現
その後取り組んだのが、連続的に触媒反応を起こし、ベンゼンを常に生成し続けるプロセスづくりだ。先の方法だと、触媒の再活性化を行うと、その間はベンゼンの生成を停止することになり、安定して供給し続けることができなかった。海外の大手石油会社では、触媒ペレットが動かないいわゆる固定層型触媒反応器を何本も並べ、1本ずつ順次メタンを供給してベンゼンを生成し、反応活性が下がるとメタンを水素に切り替え、触媒を再活性させる方法が試みられていた。しかし、張は最初からこの方法には問題があると考えていた。
「反応させる時間と触媒の再生時間はそれぞれ違いますし、反応時に外から加える熱の量と速度と、再生時に生じる熱の量と速度をそれぞれコントロールする条件も大きく異なります。実際のプラントにおいては、原料メタンと再生用水素ガスとの切り替えはそう簡単には行えません。反応塔(反応容器)と再生塔(再生容器)は、同じものを熱したり冷やしたりするのではなく、温度もサイズもそれぞれに適したかたちで個別に設計するべきだと考えました」
固定層型触媒反応器を並べるタイプのプラントの弱点はもう一つあった。触媒は使っているうちに劣化するため、数カ月に一度、運転を止めて触媒の入れ替えをする必要がある。しかし、プラントは連続稼働させる必要があり、数カ月に一度止めているようでは、プラントとして効率が悪すぎる。
「実用化を考えた場合、装置を動かしながら常に古い触媒を抜き、新しい触媒を足していくことで、連続的に運転させ続けられることが重要なのです」
そのような観点から張が構想したのが「循環流動層MTBプロセス」だ。まず、反応塔でメタンと触媒を反応させて、ベンゼンと水素のガスを得る。できたベンゼンと劣化した触媒粒子を再生塔に送り、再生塔上部のサイクロンでガスと粒子に分離。ここでベンゼンと水素を回収し、回収した水素の一部を触媒の再生に利用する。粒子は再生塔に落として水素と反応させ、再生したら再び反応塔に送る、というものだ。
MTB反応に用いる二塔式循環流動反応器の概念図と実装置
「私たちは十数年間のトライ&エラーを経て、触媒を循環させることで反応も再生も同時にできるプロセスを生み出しました。そこに、その性能を最大限に発揮できる温度、圧力、粒子を循環させる速度、再生条件などのノウハウを組み合わせることで、現時点で世界トップの反応率を実現しています」と、倉本は胸を張る。
ベンゼンの安定供給と完全国産化の実現を視野に
ここまでくれば、コストを含めて総合的な評価ができる段階に入ってきた。しかし、これをもう一歩実用化に向けて前進させるには、現状より一段階大きな試験プラントをつくって実証実験をしていく必要がある。これには企業の協力が不可欠だ。
「石油が今後も安定供給されるとは限りません。その一方、日本でメタンハイドレートの採掘などが進めば、ベンゼンの完全国産化が夢ではなくなります。そう考えるとこの技術は将来必ず大きく花開きます。化学分野だけでなく、エネルギー分野やその他の分野にもいろいろなチャンスがあると思います」(張)
「この技術は、ベンゼンの安定的供給に加え、国の喫緊の課題でもある環境負荷の低減と炭素循環システムの構築にとっても非常に重要な技術です。この技術の実用化を、企業の皆さんのご協力をいただきながらともに実現していきたい、そんなことを夢見ています」(倉本)
世界トップの技術は実用化まであと一歩のところまで来ている。残すは企業との連携だ。
創エネルギー研究部門
炭素資源転換プロセスグループ
上級主任研究員
張 戦国
Zhang Zhanguo
創エネルギー研究部門
炭素資源転換プロセスグループ
研究グループ長
倉本 浩司
Kuramoto Koji
ベンゼンの安定供給、完全国産化をぜひ一緒に実現しましょう。お気軽にご連絡を!
産総研
エネルギー・環境領域
創エネルギー研究部門