布を重ねてプレスするだけ!熱・薬品をいっさい使わず不織布を簡単接着
布を重ねてプレスするだけ!熱・薬品をいっさい使わず不織布を簡単接着
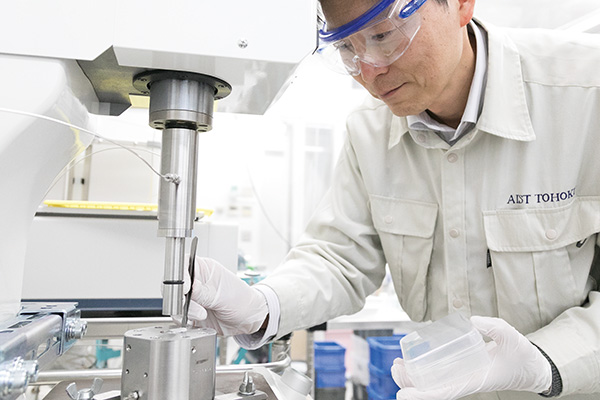
2018/03/31
布を重ねてプレスするだけ!熱・薬品をいっさい使わず不織布を簡単接着二酸化炭素による多孔質材料の製造
熱も薬品も使わずに、シンプルな装置で簡単に、しかもわずか数秒でできてしまう、二酸化炭素を使った新たな接着の技術は、応用範囲の広さが期待できる。
繊維を織らずに絡み合わせてつくる不織布。この不織布を重ねたところに二酸化炭素を注入し、ピストンで押す。それだけで布同士が接着して細かい穴の開いた構造の多孔質材料ができるという、驚くほどシンプルな材料製造技術が完成した。シンプルで低コスト、加工時間もかからないこの画期的な技術は、フィルターや触媒担持体、ギプスなどさまざまな分野での幅広い応用が期待できる。現在、実用化に向けて広く連携先を求めている。
任意の枚数の不織布を重ねて、二酸化炭素を入れてプレスするだけで接着ができる。
新発想の加工法はナノインプリント技術から始まった
「樹脂加工の方法はもう出つくし、新しく出てくることなどもうないと思っていました。まさか、まだこんな方法が残っていたとは……」
企業の担当者がこう感嘆の声をもらしたのは、化学プロセス研究部門の相澤崇史が開発した、新しい多孔質材料の製造技術を見たときのことである。実はこの方法は論文を投稿した際にも「常識的には考えられない。思い込みなのではないか」と査読者から疑問を呈されたほど、“常識をひっくり返した”ものだった。
この技術は、不織布などの樹脂製の布を容器に重ねて入れ、二酸化炭素を注入してからプレスすると、それだけで布が圧着されて多孔体ができるというものだ。接着剤などの薬品はいっさい使わず、加熱もせず室温のままでOK。驚くほどシンプルなので、「本当に可能なのか?」と思われても無理はなかった。
相澤がこの技術を発想した前段階には、宮城県産業技術総合センターから「なんとかしてナノインプリント技術を使えるものにしたい」という要望があった。ナノインプリント技術というのは、樹脂の表面に非常に微細な形状をプレスして転写する技術のことだ。例えば、樹脂の表面にナノスケールの微細な形状加工を行えば、反射防止やくもり止め、あるいは撥水や親水の機能をもたせることができる。メガネのレンズの反射防止にはコーティング剤が用いられてきたが、表面のコーティングは使っているうちに剥がれてきてしまう。それに対してナノインプリント技術はレンズ表面の形状自体を変えるために、半永久的にその機能を維持できるのだ。
これを情報記録用の媒体などに用いれば、細かい凹凸を刻むことができ、記録容量を大幅に増やすことができる。さらには半導体製造工程でも、光で加工する代わりにこの技術を応用できる。
そのようにさまざまな用途が期待され、2000年半ばにはナノインプリント技術がブームになった。宮城県産業技術総合センターでも熱ナノインプリント装置を導入したのだが、期待に反し、利用は一部企業にとどまった。それはなぜだろうか。
「加工に時間がかかり過ぎたのです。熱で樹脂を溶かして型押しし、冷めて固まったら型からはがすというのが一連の工程ですが、加熱・冷却に時間を要するため、厚めの樹脂では1つ加工するのに20分もかかりました。これでは大量に受注があっても対応できず、実用的ではありません。そのため広く普及するまでには至りませんでした」
実際、この技術は、反射防止フィルムと光ディスクで実用化されたものの広がりに欠けた。宮城県産業技術総合センターは、厚めの樹脂に適用可能なナノインプリント法を開発できないかと模索した。しかし、自分たちだけで取り組むのは難しいと考え、そこで思い出したという。
「そうだ、産総研に相澤さんがいる!」
室温で使える転写技術ができた!
相澤は超臨界での物性研究を専門とする研究者だ。超臨界水の混合部を世界で初めて観察したり、シンナーを塗料に混ぜる代わりに二酸化炭素を用いる塗装システムをつくったりと、基礎から応用まで幅広い実績がある。その相澤ならなんとかできるのではないかと声をかけたのだ。
「時間がかかる理由は温度の上げ下げにあるので、温度制御が必要な超臨界条件で加工する方法は使えません。それなら室温でできることを考えればよい。そこで液化炭酸ガスに可能性があるのではないかと気づきました」
液化炭酸ガスには樹脂の表面を柔らかくし、可塑化する働きがある。もちろん高温にすればより深くまで柔らかくなるのだが、ナノ単位の加工であれば、表層だけが柔らかくなるだけでも十分だろう。それなら、おそらく室温でもできるはずだ。二酸化炭素の扱いに長けていた相澤は、そう直感した。
試しに表面に傷をつけた平らな金属片で樹脂板をクリップで挟んで液化炭酸ガスで満たした容器に入れたのち、容器から取り出すと、見事、樹脂には傷と同じかたちが転写されていた。この予備実験での成功を受けて宮城県産業技術総合センターとの共同研究が始まり、2013年、判子を押す感覚で簡単に樹脂にナノ形状を与えられる新しいナノインプリント技術が完成した。
二酸化炭素は離型剤としても働くので、プレスした後の型離れがよいのもメリットだった。転写の工程にかかる時間はわずか30秒ほど。それまで20分かかっていた加工時間が圧倒的に短縮され、十分に実用に耐えるものとなった。この技術は、現在光学部品メーカーと実用化に向けた共同開発が始まっているという。
樹脂を接着させる新しいオリジナル技術を
ナノインプリント技術の開発を一区切りさせた相澤は、二酸化炭素を使うこの技術をさらに別の何かに応用できそうだ、せっかくなので世の中をあっと言わせるオリジナルな技術をつくりたい、と考えた。樹脂が柔らかくなる性質を用いるのなら、接着に応用できるのではないか。そこで転写技術で用いた装置を使って、樹脂板を接着する実験をスタートさせた。しかし、予想に反しうまくいかなかったという。
「二酸化炭素を用いるときの型離れの良さが、ここではデメリットとなりました。樹脂板と樹脂板をプレスしても、押し付けるのをやめればすぐに引き剥がされてしまい、接着できなかったのです」
では、どうするか。樹脂板の場合は二酸化炭素が接着面に残ることが問題だった。ということは、二酸化炭素が抜ける素材であれば可能なのではないか? 穴の空いている素材、例えば繊維ならどうだろうか。不織布のような細い繊維でできた安くて薄いシートを積層したものは、応用先もいろいろ考えられそうで、その点も好ましかった。
さっそく、同じシンプルな装置の中に、ほかの実験用に用意してあったティーバッグの袋を容器の大きさに切って重ねて入れ、二酸化炭素を充填してピストンで押してみた。プレスした後は、二酸化炭素を排気して取り除く。ナノインプリント技術とほぼ同じ、室温でできる簡単な作業だ。
プレス機に布をセットしてプレスすると、二酸化炭素が液化して、材料が柔らかくなり接合する。その後、排気をするため完成した多孔体には二酸化炭素が残らない仕組み。
「すると狙い通り接着できていたのです。2016年10月、初実験での成功でした」
ティーバッグの不織布の繊維を顕微鏡で観察すると、二酸化炭素を使わずにプレスしたものは繊維がつぶれていただけだったが、二酸化炭素を入れて加工した方は繊維同士の重なった部分がつぶれたうえに変形し、接合していた。思った通り、柔らかくなった樹脂同士がくっつきあっていたのだ。本当に、室温の二酸化炭素の中で布をプレスするだけで、新しい多孔質の材料ができていたのだ。
医薬、食品から建材、スポーツ用品まで幅広い応用に期待
この方法は、樹脂系の繊維であれば種類を問わず接着できる。それに、布は2枚であっても数百枚であっても一度 に接着が可能だ。加圧の力加減を変えれば空気の含有量 も変わるため、少し柔らかい風合いの残るもの、カチカチに 固まったものなど、異なる素材がつくれることもわかった。
「何かを挟んで層に機能をもたせることも、層の中に粉を 入れることも可能でした。目の粗さを段階的に変えたシー トを重ねて接着すれば目に勾配のついた長寿命なフィル ターを作れます。導電性のシートを挟めば電子デバイスに 応用できますし、薬剤を封入すれば医薬品に、酵素や触媒 を付着させれば、脱臭や反応用のカートリッジとしても使え ると考えられます。貫通孔が開いているので蒸れない素材 として医療、スポーツ用途にも応用可能です」
相澤が描く具体的な応用イメージの一つに、肌を通じて薬剤を体内に吸収させる医療用の経皮吸収パッチがある。喘息の薬を染み込ませたパッチや禁煙用のニコチンパッチなどがあるが、使用する薬剤の量を、重ねる不織布の枚数でコントロールできるので、患者さん一人一人に合わせたきめ細かい薬剤投与の対応が可能になると考えられる。
「接着に薬品を一切使わないこともポイントです。建材や医療用ギプス・スポーツ用プロテクターなど、密閉空間や身体に直接触れるものに使用しても安全ですので、化学物質過敏症の方でも安心して使っていただけるものになると思います」
プレスするだけという成型のしやすさや、多孔体ならではの通気性の良さも、応用するにあたってメリットとなる。
信念を形に!シンプルな技術ほど使われる
相澤には「シンプルな技術ほど使われる」という信念がある。シンプルな装置、簡便なプロセスで装置コストはかからないし、必要なのは安価な二酸化炭素のみで、加熱もしないので省エネ性が高くランニングコストも低い、室温で数秒でできてしまう生産性の高さ、これらがこの技術の売りなのだ。シンプルな技術である分、生産ラインへの導入のハードルは低い。今は空気の含有量を変えた材料の作成や、樹脂の繊維の太さを変えるなど、さまざまな実験をしているほか、接着強度や突き刺し強度の検証など多様な物性解析も進めている。
さらに企業へのサンプル配布もスタートさせ、実用化に向けた共同研究先の開拓を始めたところだ。
現在は、産総研にある卓上サイズの装置で作成可能な小型サンプルの検証実験をしている。しかし、実際は完成品のサイズに合わせた金型をつくれば、どのようなサイズでもつくれるため、樹脂多孔体の応用先はさらに広がるだろう。
「この新しい材料製造技術の可能性は企業の皆様に使っていただくことで広がっていきます。国の研究機関が生み出した技術なので、私はこの技術を、ぜひ日本の企業に実用化してほしいと願っています。もし興味をお持ちいただけたら、すぐにご連絡ください。いつでも説明いたしますし、呼んでいただければ私がお伺いします」と相澤は笑顔で結んだ。
化学プロセス研究部門
機能素材プロセッシンググループ
上級主任研究員
相澤 崇史
Aizawa Takafumi