- 高効率な連続生産フロープロセスの実現の鍵となる多段連続抽出分離システムを開発
- 多段連続抽出分離システムによる溶媒や未反応物の循環利用で、大幅な生産効率向上・廃棄物削減を達成
- 重要な香料成分であるバニリンの生産効率を従来技術よりも約17倍向上、廃棄物を約50%削減
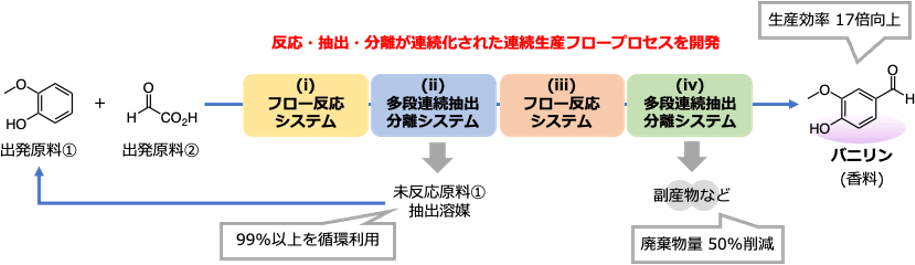
多段連続抽出分離システムを利用したバニリンの連続生産フロープロセス
※原論文の図を引用・改変したものを使用しています。
国立研究開発法人 産業技術総合研究所(以下「産総研」という)化学プロセス研究部門 フロー合成システムグループ 市塚 知宏 研究員、石坂 孝之 研究グループ長、同部門 化学反応場設計グループ 牧野 貴至 研究グループ長らは、連続的に反応・抽出・分離を実施可能な連続生産フロープロセスを構築するうえで鍵となる多段連続抽出分離システムを開発し、機能性化学品の高効率かつ低環境負荷な連続生産を実証しました。
抽出分離は機能性化学品の生産に必要不可欠な精製プロセスの一つですが、処理に多くの時間と溶媒を要するため、連続化や他のプロセスとの連結が難しいプロセスでした。産総研は、スラグ流を用いた高速抽出分離システムを効率的に多段化することで、最小限の溶媒量を用いて約3分以内に連続抽出分離ができるシステムを開発しました。今回開発した連続抽出分離システムをフロー反応システムと連結して使用することで、未反応原料や抽出溶媒を循環利用して目的物質を連続合成することが可能となります。例えば、香料の一つであるバニリンの連続生産フロープロセスを毎時数グラムの規模で運転したところ、従来技術のバッチ法と比べて約17倍の生産効率向上と約50%の廃棄物削減効果が実証できました。今回開発した技術を実用化することにより、バニリンなどの機能性化学品生産における生産性や環境負荷が大幅に改善され、持続可能なものづくりに貢献します。
なお、この技術の詳細は、2023年10月30日に「ACS Sustainable Chemistry & Engineering」に掲載されます。
医薬品、農薬、香料、電子材料のような高付加価値な化学品は、機能性化学品と呼ばれます。その世界市場規模は16兆円(2015年)を超え、2030年には36兆円に成長すると言われています(NEDO 「TSC Foresight Vol.31」より)。機能性化学品の多くは、段階的な生産方式であるバッチ法を用いて、多段階で複雑なプロセスを経て生産されています。しかし、この方法は、単位時間・単位体積あたりの生産量が低い、生産時に溶媒や未反応物などに由来する大量の廃棄物を生じる、さらに廃棄物の処理時に大量のCO2を生じるなどが大きな問題となっています。このような背景から、より高効率な生産方式であるフロー法が大きく着目されています。フロー法とは、原料を連続的に生産装置へと投入し、出口から連続的に生成物を回収する生産方式です。この方法は、バッチ法に比べ、高効率であり廃棄物を低減可能、省コスト、省スペースなど、さまざまな利点を持ちますが、これまでは主に石油化学に見られるような簡単な化学構造を持つ基礎化学品の製造に用いられてきました。近年、環境問題がクローズアップされる中で、その特長が再評価され、より複雑な化学構造を持つ機能性化学品連続生産フロープロセスの研究開発が国内外で活発に進められています。
産総研は、産学官連携で機能性化学品の製造プロセス革新を推進する目的で、2015年からフロー精密合成(FlowST)コンソーシアムを運営し、フロー法による機能性化学品の連続生産フロープロセスに係る基盤技術を開発してきました。これまでに、連続化したフロー反応システムを構築することにより、機能性化学品原料の連続合成を実証してきました(2020年7月13日 産総研プレス発表)。
今回の研究では、機能性化学品の生産に必要不可欠な抽出分離に注目しました。抽出分離は、反応後に生成物を精製するために用いられる重要なプロセスです。そのため、さまざまな反応を用いて複雑な化学構造を持つ機能性化学品を連続合成するためには、抽出分離をフロープロセスに組み込む必要があります。ただし、抽出分離は、溶媒の消費量が多く大量の廃棄物を生じてしまいます。また、多くの作業工数・時間(添加・混合・静置・分液など)を要するために連続化や反応プロセスとの連結が難しく、機能性化学品の連続生産フロープロセスを開発するうえで大きな障害となっていました。そこで本研究では、最小限の溶媒量を用いて極めて短時間内に連続処理を行うことができる高効率な連続抽出分離システムを開発しました。さらに、このシステムをフロー反応システムと連結することで、重要な香料成分であるバニリンをターゲットとした高効率で低環境負荷な連続生産フロープロセスの実証を進めました。
なお、本研究開発は、国立研究開発法人 新エネルギー・産業技術総合開発機構(NEDO)の委託事業「機能性化学品の連続精密生産プロセス技術の開発(2019~2025年度)(プロジェクトコードP19004)」による支援を受けています。
フロー反応システムと抽出分離システムから構成される化学品の連続生産フロープロセスにおいては、生成物を含む反応溶液がフロー反応システムから連続的に供給されてくるため、抽出分離システムには短時間内(数分以内)に連続処理できる能力が求められていました。しかし、従来のバッチ法を用いた抽出分離では対応することが非常に困難でした。これは、抽出分離が図1-①に示すように、(a)生成物を含む反応液へ溶媒を添加する、(b)2液を撹拌して反応溶液中の生成物を溶媒側へと抽出する、(c)溶液を静置して抽出液と残液が相分離するまで待つ、(d)相分離した抽出液と残液を分液する、といった多くの作業工数と時間を要する工程であるためであり、さらに大容量の場合は1回の抽出分離に数十分の時間を要するといった課題があったためです。加えて、高い回収率を得るために、この抽出分離を複数回行った場合(多段抽出分離)においては、回数を増やすごとに処理時間(数十分~数時間)と溶媒消費量が増大することが大きな問題となっていました。そこで本研究では、フロープロセスにおける高速での連続処理に対応できる連続抽出分離システムを開発しました(図1-②)。具体的には、スラグ流を用いた高速抽出分離システムを効率的に多段化することで(多段向流方式)、最小限の溶媒量を用いて約3分以内に連続抽出分離を実施することを可能にしました。まず、反応溶液と溶媒を混合するミキサー、目的成分を抽出する抽出管、抽出後に抽出液と残液を分離するセパレーター、から成る連続抽出分離システムを作成しました(図1-②-(1))。この方法では、抽出管において液-液間の物質移動に有利な液-液スラグ流を利用できるため、極めて高い抽出速度を得ることができます。これにより、1段あたり1分以内に抽出分離を行うことが可能です。さらに、溶媒の廃棄量を低減するため、抽出液の再利用が可能な多段向流方式という方法を用いて、この連続抽出分離システムを多段化しました(図1-②-(2))。これにより、従来技術と比べて約3分の1という少ない溶媒消費量でも高い回収率で抽出分離が可能となりました。
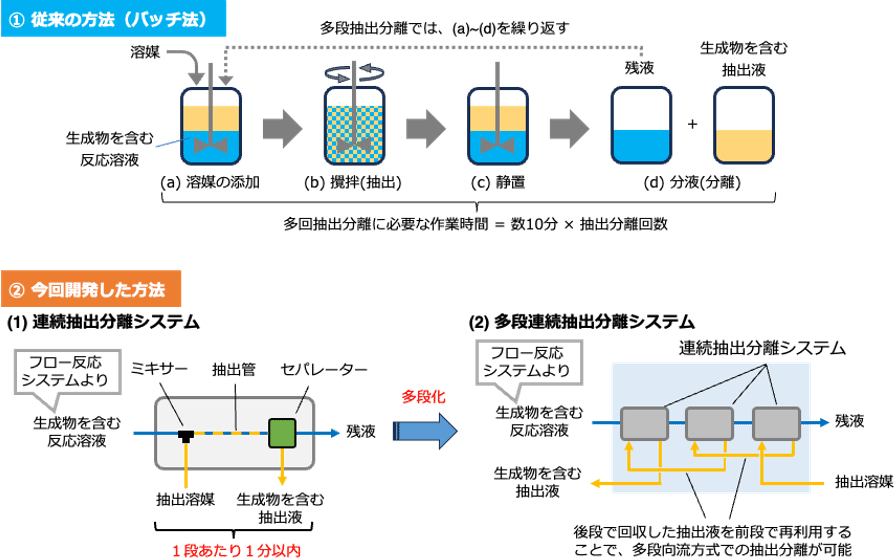
図1 従来の方法(バッチ法)と連続抽出分離システムおよび多段連続抽出分離システムとの比較
※原論文の図を引用・改変したものを使用しています。
開発した連続抽出分離システムを用いて、合成香料の一つであるバニリンの連続生産フロープロセスの実証を行いました。バニリンは、反応と抽出分離を2回繰り返す全4プロセスで作られます。今回開発した連続生産フロープロセスの概要を図2に示しました。このプロセスは、フロー反応システムと連続抽出分離システムが交互に配置・接続されており、出発原料を連続投入することで目的のバニリンを連続的に生産できます。第1工程のフロー反応システムは、芳香族求電子置換反応を高い反応効率で進行させることが可能です。続く第2工程では、多段連続抽出分離システムの高い処理能力を利用することで、99%以上の溶媒と未反応原料を循環利用しながら廃棄物を出すことなく、目的中間体を連続合成することに成功しています。また、抽出分離により目的中間体が高純度化されたことで、遅滞なく第3工程のフロー反応システムへ進むことが可能となっています。一方、第3工程では、高純度化された中間体と3相(固体触媒・中間体水溶液・空気)の接触効率を精密に設計することで、従来のバッチ法では数時間を要した酸化脱炭酸反応の反応時間を1分以内に飛躍的に短縮できる、環境調和性と高い安全性を兼ね備えたフロー反応システムを実現しました。さらに、第4工程では、多段連続抽出分離システムを用いて、合成されたバニリンを従来技術の3分の1以下の量の溶媒で選択的に抽出分離することができました。このように、一連のフロープロセスに連続抽出分離システムを組み込むことで、生産効率が大幅に向上され、高純度なバニリンを総収率71%、毎時数グラムの規模で連続生産できることを実証しました。
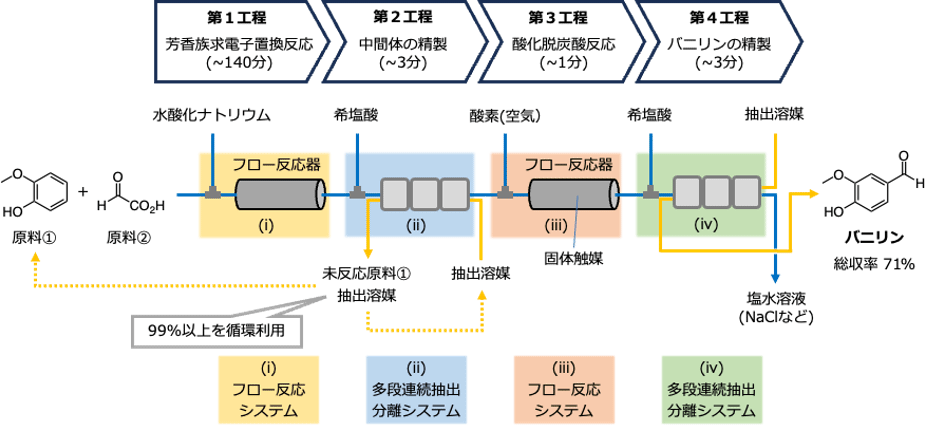
図2 多段連続抽出分離システムを組み込んだバニリンの連続生産フロープロセス
※原論文の図を引用・改変したものを使用しています。
今回開発した連続生産フロープロセスの生産効率や廃棄物発生量について、従来技術と比較しました(図3)。まず、生産効率の指標である空間時間収率(STY: Space Time Yield)を比較したところ、連続生産フロープロセスが従来技術のバッチ法よりも17倍以上高い生産効率を示すことがわかりました。これは、フロー法が有する高い接触効率などの特長により、反応効率が大幅に改善されて処理時間が短縮されたこと、加えて連続抽出分離システムの導入により生産プロセスの連続性が向上したことに起因します。また、廃棄物発生量の指標としてプロセス質量強度(PMI: Process Mass Intensity)を比較しました。その結果、従来技術と比べて廃棄物量を約50%削減できることが明らかになりました。これは、抽出効率の改善による溶媒使用量の低減と、未反応原料や抽出溶媒の循環利用による効果です。
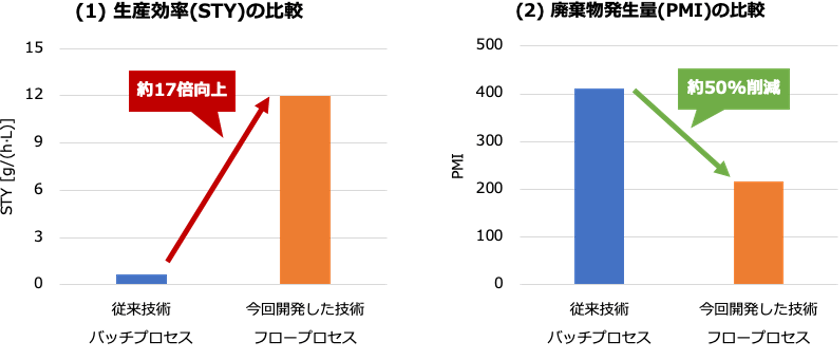
図3 従来技術と今回開発した技術の比較(生産効率・廃棄物発生量)
※原論文の図を引用・改変したものを使用しています。
本研究において、連続生産フロープロセスへ今回開発した連続抽出分離プロセスを適切に組み込むことにより、機能性化学品の連続生産での大幅な生産効率向上と廃棄物削減が可能であることが実証できました。本研究ではバニリンの生産プロセスですが、対象物質の合成ルートに合わせて、使用する触媒や反応システム、あるいは、多段連続抽出分離システムなどを最適化することにより、他の機能性化学品に対応した連続生産フロープロセスを構築することも可能です。今後は、連続生産の適用事例を増やすとともに、生産スケールの向上やプロセスの自動制御などの要素技術を確立し、連続生産フロープロセスの社会実装を目指します。
掲載誌:ACS Sustainable Chemistry & Engineering
論文タイトル:Telescoped two-step continuous-flow synthesis of vanillin
著者:市塚 知宏、佐藤 雅英、三浦 詩穂、牧野 貴至、石坂 孝之
DOI:10.1021/acssuschemeng.3c05168