国立研究開発法人 産業技術総合研究所【理事長 石村 和彦】先進パワーエレクトロニクス研究センター【研究センター長 山口 浩】ウェハプロセスチーム 加藤 智久 研究チーム長らは、株式会社ミズホと不二越機械工業株式会社と共同でSiCウェハの平坦化を高速で達成するラッピング技術を開発した。特に、低速度だった鏡面化工程では従来の12倍の研磨速度が得られ、枚様式加工法の鏡面研削工程に匹敵する新たなバッチ式加工技術を確立した。
なお、本技術の詳細は、2021年9月1日よりオンラインで開催される砥粒加工学会学術講演会(ABTEC2021)にて報告される。
SiCパワー半導体素子の実装が、大きな電力を制御する発電・送電システム、産業用ロボットや自動車、鉄道、情報通信機器といった、電力を必要とする産業や社会で始まっている。これらの普及拡大には、パワー素子の基板となるSiCウェハの製造コストの低減が最も重要である。SiCウェハ加工工程には、さらなる量産性向上(高速化および並列処理)も必要である。
SiCウェハは、極めて加工の難しい高硬脆材料である。これまでSiCウェハの平坦化は、研削加工あるいは研磨加工で行われている。前者は枚葉式で量産効率が悪い。後者はバッチ式で複数枚一括処理が可能である。しかし、シリコンウェハの量産加工に比べて加工速度が遅いため、単位時間あたりの処理枚数では6倍以上の時間がかかっている。SiCウェハは、6インチから8インチへ大口径化が進もうとしている。今後、市場拡大に伴って量産規模が増大すると、それに対応してSiCウェハを今より効率よく生産できる加工技術が必要となる。
ウェハの平坦化には、ラッピングやポリッシングに代表される研磨技術が、量産に向いたバッチ式加工技術として知られている。高硬度のSiCの研磨ではダイヤモンドスラリー(以下、「スラリー」という)を用いても研磨速度が上がらないため、鏡面化工程(表面粗さRa=1 nm程度)までは研削による枚葉式加工に頼らざるを得ない。研磨加工では、プレストンの経験則に従って研磨定盤の回転数や加工圧力を高めることで研磨速度が向上できる。しかし、定盤の遠心力によってスラリーが切れてしまったり、摩擦熱によって研磨を継続することが困難だったりという課題があり、研磨速度を高められなかった。そこで、ダイヤモンド砥石を定盤に成型した固定砥粒定盤を作製し、高速研磨装置と組み合わせることで、これらの問題の解決を試みた。(図1)
本研究開発は、民活型オープンイノベーション共同研究体つくばパワーエレクトロニクスコンステレーション(TPEC;Tsukuba Power-Electronics Constellations)において実施された。
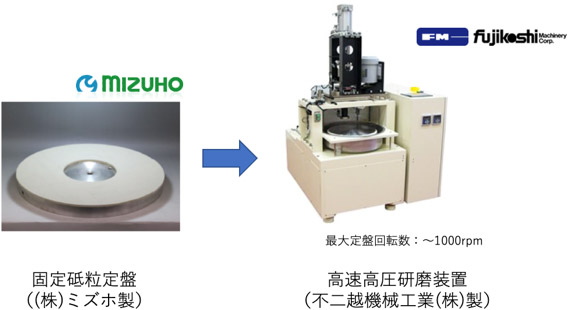
図1 本開発の設備構成
図2はSiCウェハの各種研磨条件での研磨速度を比較したグラフである。金属定盤とスラリーを使った加工では定盤回転数200 rpm超で加工が困難となった。一方で、固定砥粒定盤を用いた場合は700 rpmにおいても定盤回転数と研磨速度が比例することを確認した。これはスラリーを用いた代表的な加工条件(例:荷重200 g/cm2、回転数:50 rpm)と比較しておよそ12倍の研磨速度であり、従来の研削加工に匹敵する速度に達している。また、高速で研磨されたSiCウェハのRaは約0.5 nmであり、従来の鏡面研削加工と同等の表面品質を達成している。(図3) これらの成果から、固定砥粒定盤と高速研磨装置との組み合わせの優位性が示された。
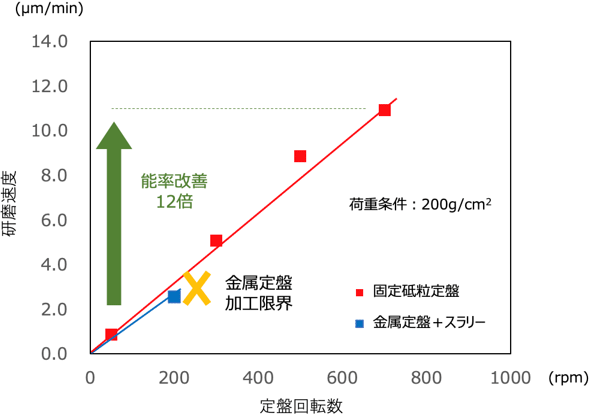
図2 各種研磨条件における研磨速度比較
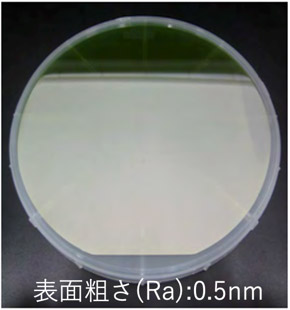
図3 本開発よって高速研磨された6インチSiCウェハ
またスラリーを使った研磨とは異なり、加工液としては水しか使用しないため環境負荷も少なく、水の供給量を制御して定盤を充分冷却しながら研磨能率を確保できる利点も新たに見いだされた。
定盤を使った研磨は主に加工圧力と定盤回転数で加工速度を制御するため、複数枚のウェハを同時に加工するバッチ式加工が可能である。図4は、SiCウェハを複数枚同時に加工した際の定盤回転数と研磨速度の関係である。ウェハ枚数が増え加工面積が増しても研磨能率を維持できることを確認した。すなわち、1バッチあたりのウェハ加工枚数を増やすことで、一枚当たりの加工時間を大幅に短縮できることが分かった。また、摩滅を抑えた高硬度の砥石を使うことで、研削加工より砥石損耗コストも抑えられるので、大口径SiCウェハを量産するプロセスの高速化と低コスト化の両立が実現可能である。
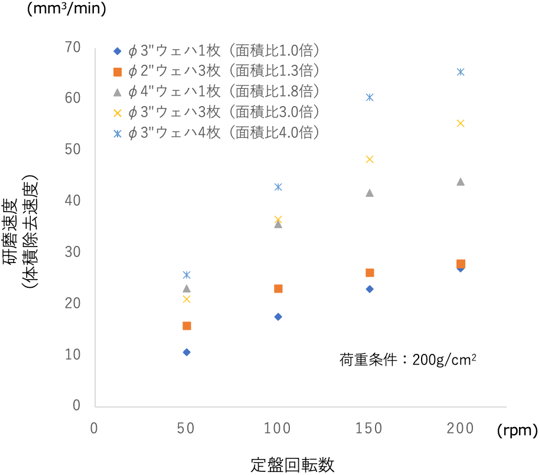
図4 複数枚同時研磨における研磨速度比較
先進パワーエレクトロニクス研究センターで保有している6インチ対応SiCウェハの一貫加工工程に本開発の研磨技術を導入し、同じく研究センター内のパワーデバイス開発へ応用することで技術実証を進める計画である。