独立行政法人 産業技術総合研究所【理事長 吉川 弘之】(以下「産総研」という)近接場光応用工学研究センター【センター長 富永 淳二】と韓国サムスン電子株式会社【代表理事副会長 尹 鐘龍】(以下「韓国サムスン電子」という)デジタルメディアR&Dセンター【センター長 朴 魯柄】は共同で、可視レーザー光と特殊な薄膜(熱体積変化膜)を組み合わせた熱リソグラフィー法と呼ばれる技術により、最小50nm(1ナノメートル:10-9メートル)サイズのドットパターンを作製することに成功した。可視レーザー光を直接描画に利用するのではなく、照射により薄膜上に熱を発生させ、その熱を利用したことと、熱により体積が変化する新規な薄膜材料を適用し、薄膜の構造を最適化することにより、極微細加工を可能にした。
今後の研究により、低コストのリソグラフィー技術として超高密度光ROMディスク原盤作製技術への実用化をめざす。
将来の超高密度光記録では、ピットサイズ100nm以下の微細加工が要求されており、代表的な加工技術としては、光リソグラフィー法や電子線リソグラフィー法が知られている。これらの技術を用いて100nmサイズの描画は可能であるが、光リソグラフィー法では短波長のレーザー光源や新規な光学系材料の開発、電子線リソグラフィー法では真空雰囲気や高電圧等の設備や装置が必要である。これらの装置は開発費や大型の装置といった点で非常に高価であり、このことは言うまでもなく装置及び加工品のコスト高を招く結果となる。また、光源などの開発は、特殊ガスや特殊光学材料の使用が必然であり、これに伴いその開発費も増大する。一方、近接場光顕微鏡を用いたリソグラフィー法は、高価な光源を使わず、可視光で100nmサイズのリソグラフィーを実現しているが、その描画速度は100µm/s(1マイクロメートル:10-6メートル)程度であり、実用的ではない。そこで、低コストで実用的なリソグラフィー技術が求められてきた。
今回我々は、以前から研究を継続している、可視レーザー光の照射で発生する熱によりドットパターンを形成する熱リソグラフィー法と新たに利用した新規材料であるテルビウム・鉄・コバルト(TbFeCo )と酸化シリコン・硫化亜鉛(ZnS-SiO2)を用いた熱体積変化膜により、50nmサイズのドットパターンを作製することに成功した。通常この大きさのドットを作製するためには、電子線や近接場光を用いたリソグラフィー法でなければ不可能と考えられていたが、今回の技術はそのような方法を用いることなく、50nmサイズの極微細構造を高速で作製することに成功した。
なお本研究成果の詳細は、2003年8月30日~9月2日に福岡大学七隈キャンパス(福岡市城南区)で開催される、第64回応用物理学会において発表される。
また、本研究に関連した特許を3件出願中である。
通常、光ROMディスクは原盤と呼ばれる金型から射出成型で作製される。この金型にはピットと呼ばれる小さなくぼみがあり、このピットがディスクに転写され、このピットを元に映像や音楽が再生される。代表的な光ROMディスクであり現在市場に出回っているDVD-ROMは、ピットの大きさがおよそ400nmであるが、将来の超高密度光ROMディスクではその大きさが数十nmになると考えられている。このサイズのピットを作製するための技術がリソグラフィーという方法である。大きさ400nmのピットの場合は紫外線を用いることでリソグラフィーを行うことができるが、サイズ数十nmのリソグラフィーを行う場合、通常、深紫外光などの短波長の光(光リソグラフィー法)や電子線(電子線リソグラフィー法)を用いる必要がある。これはリソグラフィーでは、加工サイズが小さくなるに従い、短い波長の光源が必要となってくるからである。しかしながら、光リソグラフィー法では、短波長の光源の開発は年々困難になっており、その開発費用も膨大である。また、新たな光源のための周辺技術の開発が必要となるが、そのためにも膨大な費用が必要となってくる。電子線リソグラフィー法では、サイズ10nm程度の描画が可能であるが、真空雰囲気が必要であり装置の大型化を招き、また電子源の寿命が一万時間以下などといった短所があり、これらについてもやはり高コストであるといえる。これらの手法及び装置は開発費や大型の装置といった点で非常に高価であり、このことは言うまでもなく装置及び加工品のコスト高を招く結果となる。一方、近接場光を利用したリソグラフィー法も研究されており、可視光で100nmサイズの描画が可能ではあるが、描画速度が100µm/s程度であり、非常に遅いため現実的な生産手段とはなり得ない。従って、低コストで簡便であり、かつ実用的な描画技術が求められてきた。
産総研近接場光応用工学研究センターと韓国サムスン電子デジタルメディアR&Dセンターは共同で、光記録技術の研究を進めている。その中で光ROMディスク原盤作製に必要な新規な微細加工技術の研究開発も行っており、本研究はその一環として行われた。本研究で行われたドット形成技術である熱リソグラフィー法及び、試料として使われた光磁気記録材料であるTbFeCoの特性も本センターで研究されてきたものである。
熱リソグラフィー法の原理は、光スポット内の温度分布を利用している。光を物質に照射し、その物質が光を吸収する性質を持っているならば、光のエネルギーは熱に変換される。光スポット内には光強度の分布が存在するため、その温度分布は光強度分布を反映し、熱分布が生じる。この分布は、スポット中心の光強度が一番強いため、中心の温度が一番高温になる分布を示す【図1参照】。従って、ある温度以上の領域をスポットの大きさより小さくすることができ、その領域内で化学的、物理的な反応を起こさせることによって微細なリソグラフィーが可能となる。ただし、熱の分布はレーザー光のパワーや試料の移動速度に依存するため、これらの値は最適化されなくてはならない。前回までの研究では、この方法でフォトレジスト中の微小な領域に熱化学反応を発生させ、リソグラフィー及びその後の微細加工を実現していた。しかしながら、100nm以下の大きさを持つ構造作製が困難なことや結果の再現性に難があるといった問題があった。そこで今回は、新たな材料を見いだし、これを薄膜構造とすることで上記欠点を克服し、50nmサイズのドット形成に成功した。新規材料はTbFeCoとZnS-SiO2である。この2つの材料は、加熱によって相互拡散し、また拡散後には体積が膨張するという性質を有しており、【図1】で示すような微小領域にのみこの現象を発生させることで、極微細なリソグラフィーを行っている。
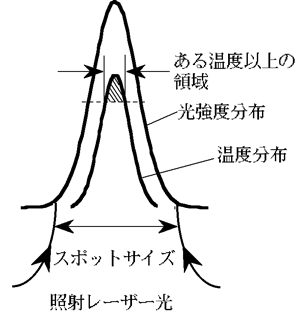
|
図1 スポット内の光強度分布及び熱分布
|
試料である熱体積変化膜は、SiO2製ディスク基板(厚さ0.6mm)にZnS-SiO2 (表面層)/ TbFeCo/ZnS-SiO2(底面層)の多層構造をスパッタリング法で作製した【図2参照】。この試料を光ディスク評価装置にのせ、速さ3m/sで回転させながら青色のパルスレーザー光(波長:405nm)を照射した。この光ディスク評価装置にはディスクの半径方向に微動(精度40nm)可能となっている。可視レーザー光は基板側から入射し、薄膜上にフォーカスされる。試料が回転していても、常に可視レーザー光が薄膜上にフォーカスされる。また、レーザー照射は、試料が一回転する間のみ行われ、その後、外側に200nm移動させ、再びパルスレーザーを照射する。これを30回繰り返し、ドットパターンを作製した。作製したドットの観察と大きさを測定するために、原子間力顕微鏡(AFM)を用いた。
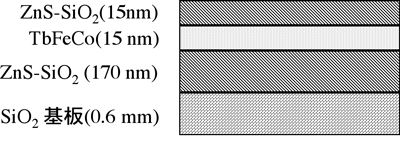
|
図2 試料構造
|
【図3】に作製されたドットパターンのAFM像を示す。左側が上面図、右側が上面図の点線に沿った断面図である。(a)、(b)、(c)はそれぞれパルス周波数15、18.75、30MHzを入射させたときの結果である。回転速度と入力したレーザーのパルス周波数の関係から、パルスが照射されている間に、試料が移動する距離はそれぞれ、100、80、50nmとなる。走査範囲は(a)、(b)、(c)ともに5µm×2.5µmである。上面図の縦方向が回転方向である。【図3】より、およそ直径が100、80、50nmのドットが形成されていることがわかる。また、断面図よりドットの高さは、(a)の直径100nmのドットで20nm程度であることがわかる。(c)は50nmのドットを形成した時のAFM像であるが、断面図を見ると直径50nmのドットもクリアに形成されていることがわかる。この大きさは電子線リソグラフィー法で作製した大きさに匹敵する。通常の光リソグラフィー法では回折限界より短い距離を持つ近接した構造物を作製することは理論的に不可能である。今回使用した光学系とレーザー波長より、回折限界は310nmであり、今回の結果は、回折限界以下の近接ドットが作製できている。従来、このサイズのドットやこれほど近接したドットの作製は、電子線や近接場光顕微鏡を用いたリソグラフィー法でしか実現しなかった。しかし、電子線リソグラフィー装置は高価、大型の装置、大消費電力であり、高コストといった問題がある。一方、近接場光顕微鏡を用いた技術では、速度が遅いため現実的な生産手段とはなり得ないといった問題があった。今回の技術は、半導体レーザーや小型の装置を用いるので、低コスト、低消費電力であり、また速度3m/sでドット作製を行っているので近接場光顕微鏡を用いた技術より、105倍も高速で作製でき、実用化レベルの描画速度といえる。
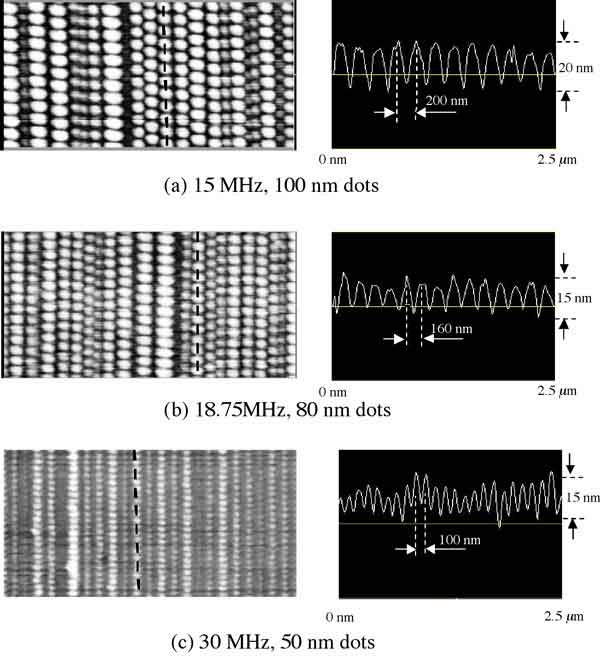
|
図3 AFM像 左側:上面図、右側:断面図
|
次にドットで文字を描画する実験を試みた。文字描画のためにディスクの回転速度、パルスレーザー照射のタイミング、照射時間、照射出力を最適化し実験を行った。【図4】はそのAFM像である。産総研の英語名の略称である‘AIST’と共同研究企業である‘SAMSUNG’の文字が観察されている。この結果により、本技術が周回上にドットを作製するだけではなく、更に複雑なリソグラフィーを行えることを示唆している。各ドットの大きさは約110nm、一文字の大きさは約1µmである。回転ぶれのため、ドットが最大約100nmずれてはいるが、現在この回転ぶれを小さくすることを試みており、更に精度よく文字が描画できると考えている。
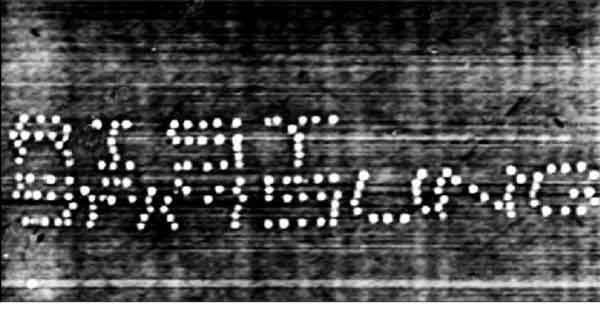
|
図4 文字‘AIST、SAMSUNG’のAFM像
|
以上のように、今回の研究で熱体積変化膜と熱リソグラフィー法を組み合わせ、以前には不可能と考えられていた微細な構造物を作製することに成功したが、解決すべき問題は残っている。例えば、実験では200nmごとに作製しているので各列は同じ間隔で並ぶはずであるが、欠落した列も観測されることやドットの大きさも列ごとに異なることなどである。これはレーザー光のフォーカス条件が列ごとに変化することが原因と考えられる。均一なドット作製をするためには、更なるレンズ駆動部分の精度向上や薄膜構造の最適化などを行う必要があると考えている。
今回の成果は、本技術が従来のリソグラフィー技術で達成可能な構造物より遙かに微細な構造物が作製可能であることを示したものである。均一なドットの作製、ドットの直径や高さの制御が当面の課題であるが、今後、更なる実験を通して問題点を克服し、低コストのリソグラフィー技術として超高密度光ROMディスク原盤作製技術への実用化をめざす。