独立行政法人 産業技術総合研究所【理事長 吉川 弘之】(以下「産総研」という)極微プロファイル計測研究ラボ【ラボ長 一村 信吾】は、株式会社明電舎【代表取締役社長 片岡 啓治】と共同で「大容量型高純度オゾン発生装置」を開発し、半導体デバイス製造プロセスへの応用を研究開発してきている。
この度、同装置から得られる超高濃度オゾンガス(濃度90%超)を用いて、高品位のシリコン酸化膜(高集積メモリ素子等に使用可能なデバイス品質酸化膜)を、400℃という極めて低温で作製する手法の開発に成功した。
オゾン(O3)は、非常に反応性の高い酸化剤であることから半導体デバイス製造プロセスなどへの応用が期待されており、特に低温酸化プロセスの実現には高い関心が寄せられている。しかし、熱反応などにより供給過程で容易に分解して酸素(O2)となってしまうため、プロセスへの応用には特別な技術の開発が必要であった。今回、産総研では、オゾン酸化プロセス用に赤外線ランプ加熱を用いた局所加熱(コールドウォール)型酸化炉を新たに作製し、オゾン発生装置から得られる超高濃度オゾンガス(濃度90%超)を、オゾンの分解を抑えて酸化用の試料基板(シリコン基板)に導入する手法を開発した。
作製した酸化炉を用いて、数十Pa~1,000Pa(約100分の1気圧)までの圧力範囲でオゾン圧力と流量の精密・安定制御の基に、超高濃度オゾンによるシリコン酸化膜の作製を行った。この結果、(1)900℃の高温熱酸化法で実現されたシリコン酸化膜の成長速度を400℃のオゾン酸化法により実現し、酸化プロセスの500℃低温化を実証した。(2)400℃で作製したシリコン酸化膜の電気特性(絶縁耐圧、酸化膜中の不純物密度、酸化膜・シリコン基板界面の欠陥密度など)は、高集積メモリ素子など先端デバイスで使用されている高品位シリコン酸化膜の特性と同等であることを明らかにした。(3)600℃で作製したシリコン酸化膜では、絶縁耐圧が従来の高温熱酸化膜の特性を凌駕することを確認した。
酸化プロセスを低温化するためには酸素分子以外の酸化活性種が必要であり、これまでプラズマなどの活性化手段を用いる試みが進められていた。しかし、活性種の安定供給が困難なことや酸化膜本体にダメージを誘発しやすい懸念が指摘されていた。本成果は、超高濃度オゾンを用いる酸化プロセスが、ダメージを誘発する危険性が無く、かつ酸化活性種であるオゾンの精密・安定供給ができる反応制御性の高いプロセスとして、十分に実用可能であることを示唆するものである。半導体デバイス製造における画期的な低温酸化プロセスの実現に大きく貢献する成果と考えられる。
オゾン(O3)は、フッ素(F)に次ぐ強力な酸化剤であり、少量であっても金属や半導体の酸化膜形成や有機物の分解などの様々な酸化プロセスに利用できることに加えて、最終副生成物が酸素(O2)であり環境への負荷が小さいという特長を有するため、広い分野にわたる応用が期待されている。特に、先端半導体デバイス作製プロセスの一つであるシリコン酸化膜作製プロセスへのオゾンの応用については、従来法では900℃程度の高温が必要であったものが、プラズマなどの支援なしに飛躍的な低温化が可能であることが予想されたため、そのプロセスの開発が期待されていた。
産総研 極微プロファイル計測研究ラボは、既に「大容量型高純度オゾン発生装置」の開発に成功しており、実用プロセスに必要な量の高濃度オゾンを安全に制御性良く利用する技術を確立していたが、先端半導体デバイス用酸化膜作製プロセスへの応用を実現するためには、オゾン特有のプロセスの開発と、作製した酸化膜がデバイス品質のものであることを実証する必要があった。例えば、高濃度オゾンは熱や金属表面との反応により容易に分解して酸素となって反応活性を失ってしまうため、従来の酸素熱酸化法で用いられている全体加熱(ホットウォール)型酸化炉への適用は困難であり、シリコンの加熱方法が異なる新しい酸化炉の開発や高濃度オゾンの供給技術の確立が是非とも必要であった。また、オゾンの流れの中に極めて微量であっても金属不純物が検出されてはならないだけでなく、最終的には、作製した酸化膜の電気容量や漏れ電流、耐電圧などの電気的特性が、先端デバイスの酸化膜として使用可能であるほどに良好であることを実証する必要があった。
以上の観点から、今回、産総研 極微プロファイル計測研究ラボでは、オゾン酸化炉の開発およびプロセス条件の最適化を行い、高濃度オゾンを用いたデバイス品質シリコン酸化膜の低温作製プロセスの開発に成功した。
従来の酸素熱酸化法では、前述のように炉内壁全体が高温のプロセス温度に保たれたホットウォール型の酸化炉が用いられるが、このような炉に高濃度オゾンを導入すると、オゾンは内壁から受け取る熱によりシリコン試料に到達する前に分解して酸素となってしまう。今回、新たに開発した酸化炉では、炉全体を高温にするのではなく、集光された赤外線ランプ光をサセプタと呼ばれる熱吸収体に照射してサセプタのみを加熱し、その上に接触したシリコンを間接的に加熱する方式となっている。サセプタ以外の部分は全て熱を伝え難い石英製であるため、高濃度オゾンは試料直前まで高温に曝されることなく、1,000Pa付近までの高い圧力であっても高濃度を保ったまま供給される。【図1】
今回、開発された酸化炉を用いてシリコン酸化膜を作製したときの酸化膜成長速度を酸化温度別に示したグラフが【図2】である。図中の点線は、従来法である酸素熱酸化法(900℃)による成長速度の代表的な値を文献から引用して書き込んだものである。この図から、高濃度オゾン酸化法では400℃という低温で従来法と同等の酸化膜成長速度が得られていることがわかる。オゾン酸化におけるこのような酸化速度の促進はオゾンの反応性が高いだけでなく、活性化エネルギーと呼ばれる反応するために超えなくてはならないエネルギー障壁が、酸素に比べて約4分の1と低いために低温でも反応しやすくなっているという理由もある。特に、このことは酸化速度の温度による変化が小さいことを示しており、オゾン酸化では、温度ムラによる酸化膜の均一性の劣化が少ないということが予想され、今後、新プロセスを大面積試料へ適用する際に有利な要因となる。
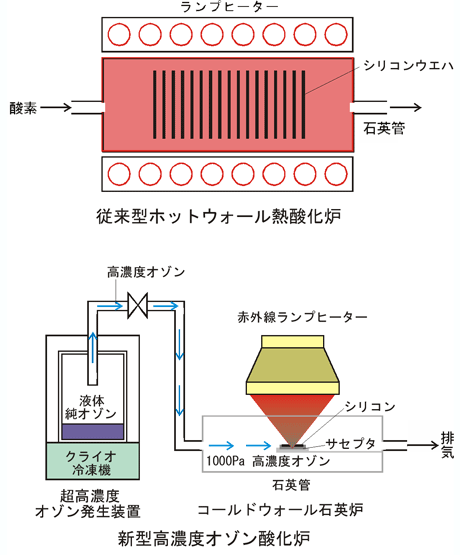 |
図1.従来型酸化炉と新型オゾン酸化炉の比較
|
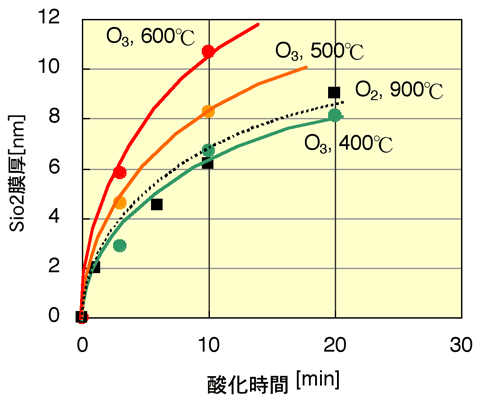 |
図2.酸化膜成長速度の温度依存性
|
高濃度オゾン酸化炉により作製したシリコン酸化膜の品質は、酸化膜の上にアルミニウムなどの金属電極を蒸着して「金属-酸化膜-シリコンの構造」(MIS構造)を作り、その電気特性を測定することにより調べることができる。測定する主な電気特性は、電気容量-電圧特性、漏れ電流-電圧特性などで、これらの値から、酸化膜-シリコン界面の整合性(界面準位密度)、酸化膜中の欠陥の量(固定電荷密度)、絶縁破壊電圧などのデバイス特性に重大な影響を及ぼす特性値が明らかとなる。高濃度オゾンにより400℃で作製した酸化膜では、これらの値がそれぞれ5×1010cm-2eV-1以下(Dit)、1.0×101cm-2以下(Nf)、13 MV/cm以上(Ebd)となり、いずれもデバイス品質酸化膜に要求される水準を充分満たしていた。【図3】
また、600℃で作製した酸化膜では、これらの特性値はさらに向上し、特にEbdは14MV/cm以上となり従来法により作製した酸化膜の特性を超える良質な膜となっていた。
一般に低温での酸化では、プラズマなどを用いて反応の活性化を行う必要があるが、プラズマ中のイオンが試料にぶつかることで酸化膜がダメージを受けやすいという問題が懸念されている。オゾン酸化ではそのような活性化手段の支援を必要とせず、ダメージを抑えた高品質の酸化膜が得られるという特長を有する。
以上によって、今回、開発に成功した高濃度オゾン酸化プロセスは、従来法より飛躍的に低温なプロセス条件において、デバイス品質のシリコン酸化膜の作製に適用可能であることが実証された。
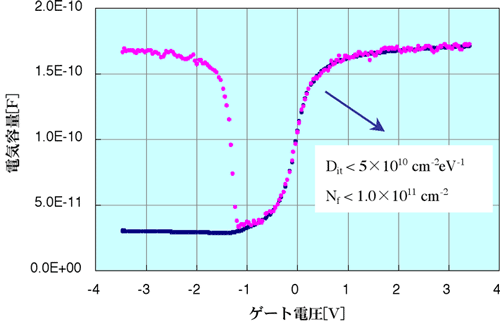 |
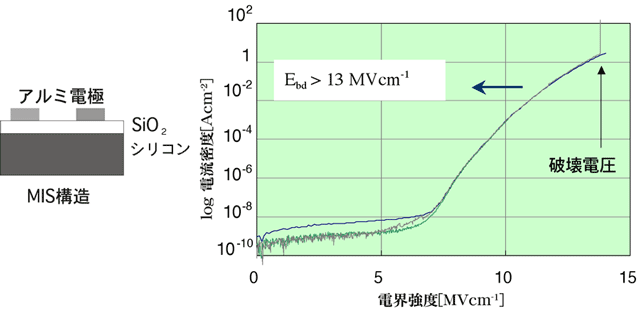 |
図3.MIS構造と400℃で作製したオゾン酸化膜(膜厚5nm)の電気特性
(電気容量-電圧特性、漏れ電流-電圧特性)
|
今回、開発した高濃度オゾン酸化プロセスは、極めて低温なプロセスであるにも係わらず、高品質なシリコン酸化膜の作製が可能であり、今後さまざまな酸化プロセスに適用することにより画期的な低温化が実現すると期待される。それらの中から例を挙げて説明する。【図4】
一つは、液晶パネルなどの制御に用いられる薄膜トランジスタ(TFT)のゲート酸化膜作製プロセスへの適用である。液晶パネルの大型化や高速化に伴い、現在、次世代高性能TFTを大型ガラス基板上に作製する技術の開発が検討されている。しかし、液晶パネルに用いられる比較的低品質なガラス基板は高温プロセスに耐えることができないため、400℃程度の低温で高品質なゲート酸化膜を作製できるプロセスの開発が必要である。これまでに述べてきたように、産総研が開発した高濃度オゾン酸化プロセスは、液晶パネル用高性能TFTの開発における多くの課題を解決できることが期待されるため、今後、それらの課題を念頭においた研究開発を進めていく予定である。
もう一つの例は、フラッシュメモリなどに代表される不揮発性メモリ用の高性能ゲート酸化膜作製プロセスへの適用である。不揮発性メモリのゲート酸化膜は、膜厚こそ最先端の論理デバイスやDRAM先端デバイスの2nm前後に比べてその数倍の厚さであるが、低い漏れ電流値や高い絶縁破壊電圧など、酸化膜の高い信頼性が要求されている。産総研が開発した高濃度オゾン酸化プロセスは、これらの課題に関しても解決の糸口を与えるものであると期待される。
更にまた、非常に薄くても高品質な酸化膜の作製が可能であるオゾン酸化法の特長を活かして、ナノテクノロジーの研究開発の基盤を支えるナノスケールの標準物質(極薄膜スケール)として、高品質極薄シリコン酸化膜を作製し供給することも産総研に課せられた役割と考えており、現在その計画を進めている。
なお、本成果は、一部が米国物理協会誌“Applied Physics Letters”に来月掲載(掲載号未定)され、2002年9月17日より名古屋で開催予定の「固体素子材料に関する国際会議(SSDM2002)」および2002年9月24日よりカナダ・バンクーバーで開催予定の「第10回半導体先端加熱プロセスに関する国際会議(RTP2002)」で発表する予定である。
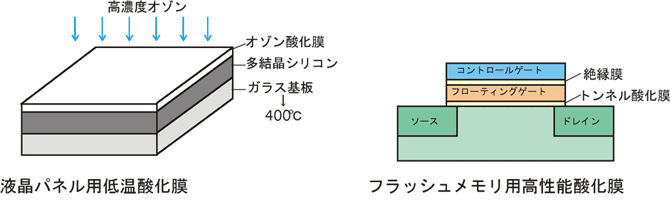 |
図4.高濃度オゾン酸化プロセスの適用例
|