独立行政法人 産業技術総合研究所【 理事長 吉川 弘之 】(以下「 産総研 」という)ナノテクノロジー研究部門【 部門長 横山 浩 】の 村田 和広 主任研究員は、従来のインクジェット技術に比較して1/1000以下の超微細液滴(サブフェムトリットル)の吐出が可能な技術( サブミクロンインクジェット技術 )を開発した。この技術を用いて、導電性高分子や金属超微粒子などの様々な材料を、直径1ミクロン以下のドットで、基板上に精密に配列させることに成功した。【図1~3】
図1 サブミクロンドット印字例
(ドット間隔は3µm)
|
|
図2 サブミクロンドット印字例
(ドット間隔は3µm)
|
|
図3 複雑図形の描画例 【導電性高分子】
(線幅3µm、格子部分のピッチ10µm)
|
さらに、ハリマ化成株式会社【 代表取締役社長 長谷川 吉弘 】(以下「 ハリマ化成 」という)筑波研究所【 所長 松葉 頼重 】が開発した「安定分散した金属ナノ粒子ペースト( ナノペースト )【図4】」をインクとして用いた共同研究によって、表面実装技術の鍵を握る線幅が数ミクロンの超微細配線を基板上に直接描画することに成功した。【図5】 大気中しかもデスクトップでの超微細配線の形成は、表面実装技術に革新をもたらし、電子機器の一層の小型化を可能にし、開発・製造スピードを大幅に短縮することができるものと期待される。
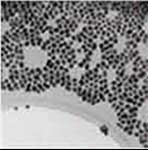
図4 安定分散した金属ナノ粒子の電顕写真
(粒径は約5nm)
|
|
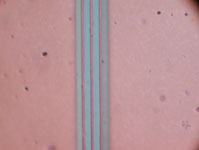
図5 ナノペーストのポリイミド基板上への印字例
(線幅3.6µm、ラインスペース1.4µm)
|
また、本技術は、表面実装技術分野のみならず、バイオ、光、超微細加工技術などのナノテクノロジー分野における様々な革新的応用が期待される。
産総研では、さらに、この技術分野の研究の深化と応用範囲の拡大のために、今回発表した金属ナノ粒子以外の分野についても広く共同研究を行うことを検討しており、ナノテクノロジー分野の研究の活性化と幅広い応用分野の開拓を目指していく。
急速に進む電子情報機器の小型化の一方で、従来の半導体製造技術は、高価な装置、複雑な工程、膨大な資源消費など高環境負荷の装置産業として抱える問題も大きい。一方、こうした技術の対局に位置する簡便な製造プロセス、低コスト、低環境負荷、省資源、省エネルギーの新プロセスである直接回路描画法の開発は、プリンタブル電子回路のみならず、従来の半導体産業においても革新をもたらすと期待されていた。
また、現在、世界的に研究が進められているナノテクノロジー分野の研究成果の実用化にあたっては、「ナノの世界」と「マクロの世界」を有効に結ぶ手段が不可欠で、有機、無機、バイオなど様々な材料を「微細量・任意の位置」に配置するツールの開発が強く望まれていた。
現在、一般に市販されているインクジェット方式の最小ドット量は、4ピコリットル程度である。4ピコリットルの体積とは、直径20ミクロン程度の球体積に相当する。人間の目には可視限界が存在するため、通常の印刷用途としては数ピコリットルの吐出量でも十分であるが、微細回路形成などの産業用途を考えた場合、さらなる液滴の微細化が望まれていた。しかしながら、微細液滴の吐出には、ノズルのつまり、使用できる溶液の制限など多くの問題があり、実現が困難であった。
こうしたニーズを背景に、産総研では、ナノテクノロジー分野での研究開発ツールとして「サブミクロンインクジェット技術」を開発した。
今回、産総研は、従来のインクジェット方式とは異なる「独自のインクジェット方式」を開発し、最小ドット径1ミクロン以下、液滴体積量としては“サブフェムトリットル”の微細液滴の形成と配列に成功した。これは市販のインクジェット方式に比べ、1/1000以下の体積の微細吐出量であり、インクジェットによる回路形成技術として、現在、世界最高レベルである。産総研では、この装置を用いて、カーボンナノチューブ、導電性高分子、セラミックスなど様々な溶液の配列が可能な事を確認している。さらに、ハリマ化成が開発した「安定分散した金属ナノ粒子ペースト(ナノペースト)」をインクとして用いて、ガラス基板やポリイミド基板状に回路描画を行った結果、数ミクロンの線幅の金属微細配線を直接描画することに成功した。
従来の技術が、資源、エネルギー、環境、設備投資など多くの問題を抱えているのに対し、今回開発した技術は、“必要な部分にだけ必要な資源を配置する”省資源、省エネルギーの環境適応型技術であることが大きな特徴である。また、高価な製造設備は必要とせず、大気中でしかもデスクトップで超微細加工を行うこともできるので、「電子インク、有機EL、有機トランジスタなどの印刷プロセスにより作製可能な革新的デバイスの製造法」への応用も期待できる。さらに、露光マスクや蒸着マスクなどを必要としないため、回路設計から試作までの時間が大幅に短縮され、開発速度の飛躍的な向上をもたらすことも期待される。
開発した装置は実験室レベルではあるが、装置構成が簡単であり、実用化にあたっての問題はない。このようなサブミクロンのドットなどを印字できるインクジェット技術は世界的にも例が無く、今回、ハリマ化成との共同研究で行った表面実装技術分野における応用例のみならず、バイオ、光、超微細加工技術などのナノテクノロジー分野はもちろん、多くの産業および研究開発分野においても幅広い応用可能性を持つ。
産総研では、さらに、この技術分野の研究の深化と応用範囲の拡大ために、今回発表した金属ナノ粒子以外の分野についても広く共同研究を行うことを検討しており、ナノテクノロジー分野の研究の活性化と幅広い応用分野の開拓を目指していく。