独立行政法人 産業技術総合研究所【理事長 吉川 弘之】(以下「産総研」という)先進製造プロセス研究部門【研究部門長 三留 秀人】高性能部材化プロセス研究グループ【研究グループ長 吉澤 友一】福島 学 研究員、中田 昌幸 元産総研特別研究員らは、氷を利用してマイクロメートルサイズの細孔(気孔)を持つ超高気孔率セラミックス多孔体を作製する技術を開発した。
今回開発した作製技術の特徴は、冷凍庫内でゼリー(ゲル)が凍る現象をセラミックス多孔体の製造に適用した点にある。新たに開発したゲルは、微量のセラミックス粉末と、大量の水分を保水できる高分子から構成されている。このゲルを凍結すると、ゲル内に細孔源となる氷が形成され、これを乾燥し氷を取り除いて焼成すると、マイクロメートルサイズの細孔を有する90%以上の高気孔率セラミックス多孔体が製造できる(ゲル化凍結法)。含まれる水(氷)の部分が細孔となるため、ゲルの水分量を変えることで気孔率をコントロールできる。凍結温度を変えると氷結晶のサイズが変わるため、細孔のサイズを調整することができる。また、鋳込み成形を用いるため、製品に近い複雑な形状に成形することが可能である。フィルターや触媒担体をはじめ幅広い用途への適用が期待できる。
本法により、セラミックスの種類に依存せず、炭化ケイ素、コーディエライト、アルミナ、ジルコニアの高気孔率多孔体が得られた。得られた多孔体は、最高93%の気孔率をもち、ハンドリングはもちろん切断、研磨などの機械加工に十分な強度も併せもつ。また、製造には職人的ノウハウが必要なく、企業等への速やかな技術移転も可能である。
なお、本研究成果は北九州市で開催される日本セラミックス協会第21回秋季シンポジウム(9月17日、18日)および米国ピッツバーグ市で開催されるMaterials Science & Technology Conference & Exhibition - MS&T'08国際会議(10月8日)にて発表予定である。
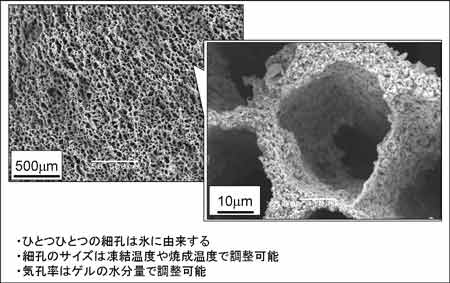 |
ゼリー(ゲル)が凍る現象を利用して作製した高気孔率(約90%)の炭化ケイ素
|
多孔体とは、その内部に細孔(空隙)を有するものであり、廃水や排ガス等に含まれる有害物質を細孔のサイズによってふるい分けるフィルターや、触媒担体など環境浄化部材として利用されている。セラミックス多孔体は、プラスチックをはじめとする樹脂材料や金属材料よりも耐熱性や耐腐食性が優れていることから、過酷な環境での使用が可能である。特に近年、資源の有効利用の観点から水のリサイクル(フィルターで廃水から有害物質を取り除き、工業用水等に再利用する)、産業機器や自動車から排出される人体に有害な微粒子を除去するための脱塵フィルターなどにセラミックス多孔体の更なる適用が期待されている。
通常、多孔体製造には原料セラミックス粉体が緻密化しない温度で焼成する方法が用いられているが、この方法では、得られる気孔率は最大でも50-60%程度であった。高気孔率化を得るためには、樹脂ビーズや炭素などの造孔剤をセラミックス粉体に大量に添加し、酸化除去することにより細孔として付与する手法がある。しかしながら、この手法では、造孔剤が除去されて形成された細孔が孤立して存在し、細孔同士の連通性が悪くなる点が問題となっていた。一方、市販のスポンジにセラミックススラリーを染み込ませ、スポンジ部分を酸化除去して多孔体を得る方法もあるが、細孔のサイズはコントロールができず、極めて低強度であるという問題点があった。これらの手法では、造孔剤やスポンジの酸化除去時に大量の二酸化炭素や、有害なガスが発生するため、環境に負荷を与えてしまう問題点もあった。
産総研先進製造プロセス研究部門では、セラミックス部材の高次構造制御に関する研究開発を長期に渡り行ってきており、その中で上記のセラミックス多孔体の作製方法に係わる問題点に早くから着目し、それらを一体的に解決し、なおかつ地球環境に優しい製造法を確立するための研究開発を進めてきた。
今回開発した製法は、微量のセラミックス粉末と大量の水分を含むゲルを凍結させて多孔体を得る手法(ゲル化凍結法)である。ゲルを凍結した後に、内部に形成された氷を取り除き、焼成することで、超高気孔率の多孔体を得る手法である(図1)。水(氷)が細孔源となるため、ゲルに含まれる水分量を調整することにより、気孔率をコントロールできる。開発したゲルは、大量の水分を保水することが可能であり、現在最大93%程度まで気孔率を増大させることができている。また、凍結温度を変えることで、細孔径を調整することも可能である。ゲルを凍結させるということは、「家庭の冷蔵庫(冷凍室)でゼリーを凍らせる」のと同じ操作であり、鋳型と冷凍庫があれば職人的ノウハウも必要とせず、簡単に高気孔率体が得られるのが特徴である。
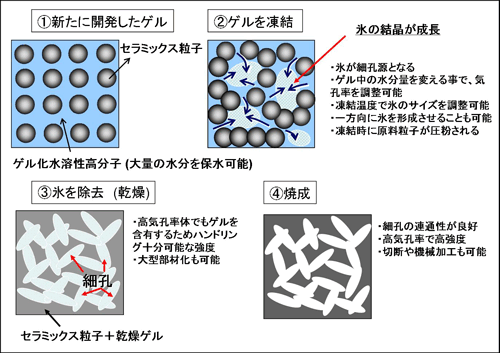 |
図1 超高気孔率セラミックス多孔体の作製プロセス
|
得られた気孔率90%の炭化ケイ素多孔体の概観写真を図2に示す。型を用いて成形するため、棒状、円筒状、板状など製品に近い形状に成形することが可能である。90%以上の気孔率を有する焼成体でも、切断、研磨等の機械加工は十分に可能であった。加えて、乾燥体、脱脂体のハンドリングにも問題は無かった。凍結時に、原料セラミックス粒子が充填されるため、高強度体が得られるものと考えられる。
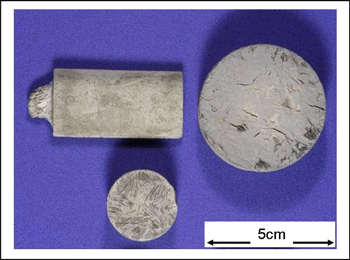 |
図2 作製した気孔率90%の炭化ケイ素多孔体の概観
|
図3の電子顕微鏡写真は、左図がゲル化後に-50℃、右図が-20℃で凍結し、乾燥、焼成により作製した気孔率87%のコーディエライト多孔体である。観察される一つ一つの細孔は、氷が形成した跡と考えられる。凍結温度によって細孔サイズをコントロールすることが可能であるため、低い温度で凍結した場合は、左図のような微細な細孔を付与することができる。これらの多孔体は最大4MPaという高い圧縮強度を有していた。
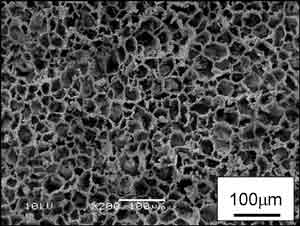
-50℃で凍結、乾燥、焼成 |

-20℃で凍結、乾燥、焼成
|
図3 コーディエライト多孔体の電子顕微鏡写真
|
また、本法によれば、氷が細孔となるため、樹脂系造孔剤やスポンジを用いた場合と比較して、二酸化炭素等の放出を圧倒的に低減できることから、低環境負荷の作製プロセスであることも大きな特長である。
以上のように、ゲル化凍結法により、超高気率セラミックス多孔体が簡便かつ低環境負荷のプロセスで作製できるようになり、セラミックス多孔体の高性能化と用途の拡大への目処がついたものと考えている。
今後は、細孔の連通性の向上、細孔サイズの更なる低減など、特性の更なる向上を図っていく。本技術は、酸化物、非酸化物を問わずあらゆる粉末に適用可能であり、またプロセスに大型で特殊な装置も必要とせずに、高気孔率で機械加工可能な強度を有するセラミックス多孔体を簡便、安価に供給できる技術である。今後、同セラミックス多孔体を、フィルターや触媒担体に加え、吸湿材、吸着材、燃料電池、衝撃吸収材、断熱材や生体材料などの多種多様の細孔径や気孔率が要求される部品や、既存部材の軽量化等にも適用し、用途の拡大を図っていきたいと考えている。サンプル提供は可能であり、積極的に企業等との共同開発に発展させたいと考えている。