独立行政法人 産業技術総合研究所【理事長 吉川 弘之】(以下「産総研」という)先進製造プロセス研究部門【研究部門長 三留 秀人】高性能部材化プロセス研究グループ 吉澤 友一 研究グループ長は、美濃窯業 株式会社(以下「美濃窯業」という)と共同で炭化ホウ素セラミックスの常圧焼結技術を開発した。
今回、金属蒸気を含む雰囲気中で炭化ホウ素セラミックスの緻密(ちみつ)化が大幅に向上することを発見し、これを用いて常圧焼結で理論密度の95%以上の高密度焼結体を得ることに成功した。得られた焼結体の機械的特性は、市販のホットプレス焼結体に迫る値を示し、実用にも十分耐えられる。
今回開発した炭化ホウ素セラミックスの常圧焼結技術によって、複雑な形状の部品作製や焼結体の価格の大幅な低減が可能となり、硬質軽量部材として広く利用されることが期待される。
本研究の詳細は、平成20年3月20~22日に長岡市で開催される日本セラミックス協会年会で発表される。
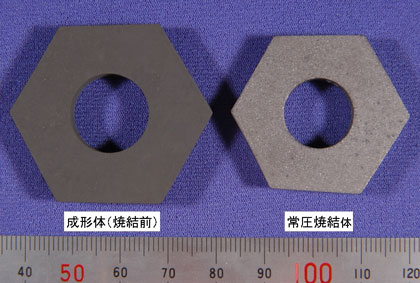 |
炭化ホウ素セラミックスの成形体(焼結前)と常圧焼結体の外観
|
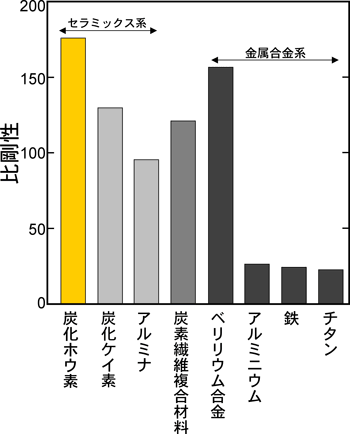 |
図1 各材料の比剛性 |
近年、省エネルギー、省力化、生産の効率化などの観点から、材料、部材などに対する要求が厳しくなってきている。セラミックスは、高温でも安定で、優れた硬さ、耐食性、軽量性などを有し、過酷な環境で使用される半導体製造装置、高温用部材、耐摩耗部材、精密機械などの機械部品に利用されている。今後、省力化や省エネルギー化、環境問題対応のため、機械のメンテナンス頻度、摩擦損失、潤滑油使用量などの低減が強く求められてくることから、高い耐摩耗性を有する部材が望まれている。また、生産効率の向上は、国際競争力を高めるために重要であり、生産機械の高速動作を可能にする
剛性が高く軽量な材料が熱望されている。
炭化ホウ素は、実用セラミックスの中で最高の硬さと最高の軽量性を有する。また、高い弾性率を有するため、弾性率を材料の比重で除した値である比剛性は、他のセラミックス、炭素繊維複合材料やベリリウム合金をしのぎ、実用材料では最高の値を示す(図1)。このため、耐摩耗部材や比剛性の高い軽量部材として期待されている。以上のように、炭化ホウ素は優れた特性を示すが、実用セラミックスとして広く用いられている炭化ケイ素と比較すると極めて焼結が難しい。現在、炭化ホウ素セラミックスの工業的な焼結法としては、ホットプレスなどの高温で型を用いて加圧をする加圧焼結法が用いられているため、常圧(無加圧)で焼結して得られる他のセラミックスと比較して製造コストが極めて高く、また、製造できる形状、大きさなどにも大きな制約がある。優れた特性をもつ炭化ホウ素セラミックスを広範囲に適用するためには、通常のセラミックスと同様に常圧(無加圧)で焼結できる技術(常圧焼結法)の開発が求められている。
産総研先進製造プロセス研究部門高性能部材化プロセス研究グループでは、窒化ケイ素、炭化ケイ素、アルミナなどの構造用セラミックスの高性能化や新規製造プロセスの研究に取り組んでいる。その研究の一環として、セラミックスメーカーである美濃窯業と共同で実用セラミックスとしては、最も硬く、最も軽量な炭化ホウ素セラミックスの常圧焼結技術の開発に取り組んできた。
現在、炭化ホウ素セラミックスの工業的な焼結法としてホットプレス法が用いられているが、この方法では原料粉末を高温で耐熱性の型に入れて加圧する必要があるために、単純な形状の成形体しか焼結できず、また、焼結後に高価なダイヤモンド工具を用いた研削加工によって、所要の形状に加工する必要がある。そのため、製造コストが極めて高く、製造できる形状、大きさなどにも大きな制約がある。
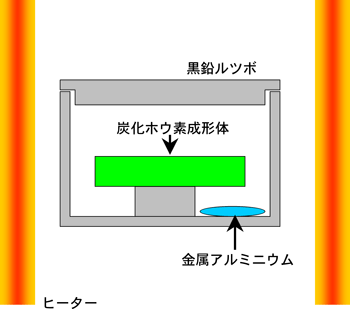 |
図2 開発した焼結方法 |
一方、加圧を必要としない常圧焼結法に関するこれまでの研究では、比較的多くの焼結助剤(焼結を促進する補助材料)を添加するものがほとんどであった。この焼結助剤を添加すると、炭化ホウ素セラミックスがもつ高硬度、軽量性という利点が損なわれるため、大量に添加することは避ける必要がある。
本研究では、加圧や焼結助剤添加をせずに、金属蒸気を含む雰囲気中で焼結すると炭化ホウ素セラミックスの緻密(ちみつ)化が大幅に向上すること、金属蒸気としては、特にアルミニウムにその効果が大きいことを新たに見いだした。具体的には、図2に示すように黒鉛ルツボの中に焼結助剤を添加していない炭化ホウ素成形体とアルミニウムを接触しない位置に配置し、常圧のアルゴン雰囲気、焼結温度2200℃以下で焼結したところ、理論密度の95%を越える高密度な炭化ホウ素セラミックス焼結体を得ることができた。
得られた炭化ホウ素セラミックス焼結体には、1重量%未満のアルミニウムが含有されるが、ごく少量であるため炭化ホウ素セラミックスの性能には影響しない。また、本成形体にシリコンやタングステンなどの他の焼結助剤を1%程度添加することによって、さらなる高密度化も達成された。
今回の開発により常圧焼結が可能となったため、1回の焼結で多数の焼結体が製造でき、従来の方法である、1回の焼結で1個の焼結体を製造し、その後に切断などの加工が必要な加圧焼結(ホットプレス)法と比較して大幅な生産性の向上が期待できる。また、既存の種々の成型法が利用できることから、これらの成形法を用いて所要の形状(複雑な形状を含む)を成形し、焼結することができるため、焼結後の研削加工が最小限となり複雑形状部品を安価に作製することが可能となった。これらの生産性の改善から、製造コストを2/3以下に低減することも期待できる。図3にホットプレス法と常圧焼結法による複雑形状製品の製造プロセスの概要図を示す。
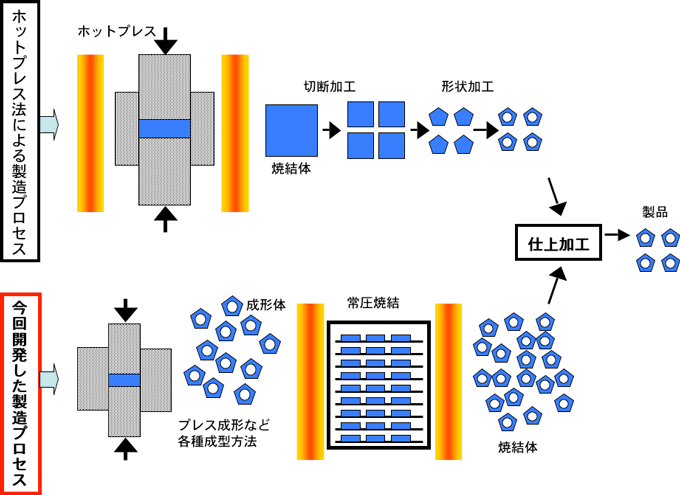 |
図3 ホットプレス法(上)と常圧焼結法(下)による製造プロセスの概要図 |
本法により試作した常圧焼結炭化ホウ素セラミックス材、市販のホットプレス焼結材、焼結助剤(13重量% TiB2)を多量に添加した常圧焼結材(論文値)の機械的特性を図4に示す。図より本法で作製された試作常圧焼結材は、市販のホットプレス材に迫る値を示し、実用にも十分耐えられることが分かる。
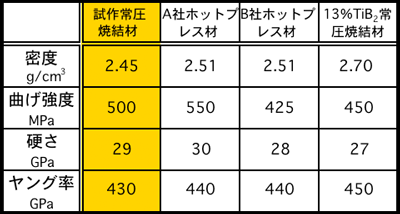 |
図4 開発材と市販ホットプレス材の機械特性 |
図5は、今回開発した技術により金型で成形した六角形の穴あき部品と、金型成形後に成形体を旋削加工し、丸みを付与してから焼結した円柱状部品 (焼放し状態:研削加工は行っていない)である。
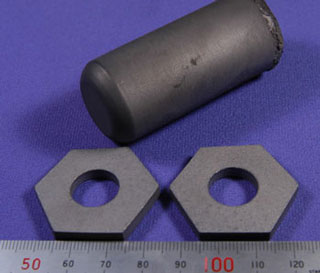 |
図5 常圧焼結炭化ホウ素セラミックスの焼放し体の外観 |
今後は、金属蒸気中で常圧焼結すると緻密(ちみつ)化が大幅に向上することなどの学術的根拠の解明を進めるとともに、焼結条件のさらなる改善や多種の成型方法の適用など製造プロセスの検討を行う。また、炭化ホウ素の欠点である脆(もろ)さを克服するために、これまで蓄積してきた炭化ケイ素の高靱化手法を本材料にも適用するなどの検討を行いたい。
本技術は、極めて硬くて軽く、比剛性の大きい材料を安価に供給できる技術であり、これまでに使用されているサンドブラスト用のノズルやメカニカルシールなどの低価格化、さらに耐摩耗部品やハードディスク基板、半導体露光装置用高速移動ステージ、複雑形状の機械部品など、軽量性・耐摩耗性が要求される用途への新たな展開を図りたいと考えている。サンプル提供は可能であり、ユーザー企業との共同開発に発展させたいと考えている。