独立行政法人 産業技術総合研究所【理事長 吉川 弘之】(以下「産総研」という)先進製造プロセス研究部門【研究部門長 三留 秀人】先進焼結技術研究グループ【研究グループ長 渡利 広司】杵鞭 義明 研究員および加賀 久 元産総研特別研究員らは、新東工業株式会社【代表取締役社長 永井 淳】(以下「新東工業」という)と新東ブイセラックス株式会社【代表取締役社長 川合 悦蔵】(以下「新東V」という)との共同研究により、遠心力による均一加圧を利用した新プロセス(遠心加圧溶融法)を開発し、ビスマス-テルル系高性能熱電厚膜の作製に成功した(図1)。このプロセスでは、単結晶に近い構造の厚膜が得られ、熱電特性は実用レベルの性能を示した。
熱電厚膜を用いた熱電発電素子は、空冷フィンとしても働き、自然冷却でも発電に充分な温度差を確保でき、また曲面形状の排気ダクトなどにおいても使用できるという特徴を持つ。今回開発した遠心加圧溶融法は、単結晶に近い熱電厚膜が得られるだけではなく、従来の熱電厚膜作製法より、製造工程が大幅に簡略化でき、材料歩留まりが飛躍的に改善できる。
なお、本研究成果は日本セラミックス協会2008年年会(3月21日)、日本金属学会2008年春期大会(3月27日)、2008年春季第55回応用物理学関係連合講演会(3月30日)にて発表予定である。
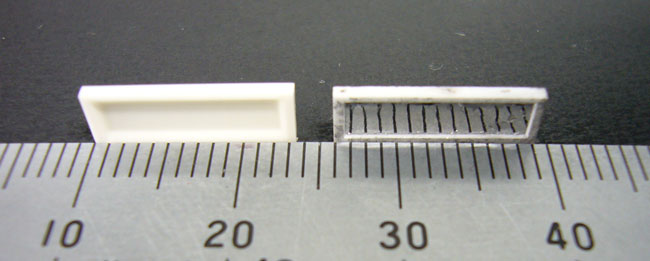 |
図1 基板(左)と基板上に成膜した厚さ200 μmの熱電厚膜(右) |
熱電発電とは、熱エネルギーを直接電気エネルギーに変換する技術である。特徴として、可動部分がないため信頼性が高くメンテナンスフリーで長寿命であること、小規模でも効率が低下しないこと等が挙げられる。製造工場、自動車等から大量に発生する未利用の廃熱を熱電発電により電力に変換して有効利用できれば、社会が直面しているエネルギー・環境問題の解決に大きく貢献できる。しかしながら、民生・産業用として使用するにはエネルギー変換効率が低く、発電素子の製造コストが高いことから、一部の特殊な例を除き民生用に採用された例はこれまでなかった。そこで、廃熱エネルギーを高効率・低コストで電気エネルギーとして回収する熱電発電技術の開発が強く望まれている。特に、熱電厚膜を用いた発電素子は、形状デザインの自由度が高いため、希薄かつ分散した多種多様な熱エネルギー源に適用しやすく、廃熱エネルギーの有効利用のためには重要と考えられている。
産総研、新東工業、新東Vは、これまでに遠心力を利用した非接触型加圧による焼結装置(遠心焼結装置)を開発し、厚膜、積層体、小型形状のセラミックスの遠心焼結技術を確立してきた(2004年2月2日プレス発表)。
一方、熱電厚膜は、主にスクリーン印刷焼結法やメッキ法によって作製される。前者は焼結を利用するため、膜の密度は約80%と低い。後者は、製造工程が複雑であり、また厚さ数百 μm状の厚膜の作製は困難である。
そこで、遠心焼結技術やその関連技術を、熱電厚膜作製に応用し、高出力化、低コスト化、小型化を目指した共同研究に取り組んできた。
今回、開発した方法(遠心加圧溶融法)は、あらかじめ溝加工を施した型(絶縁酸化物の基板)に原料粉末を所定量充填した後、蓋をかぶせて閉鎖空間とする。この基板に、厚さ方向の遠心力を加えながら、原料を溶融・凝固させて熱電厚膜を得る方法である(図2)。密度がほぼ100%の膜が得られ出力の増加に貢献する。また、メッキ法に比べて簡単な工程であり、しかも、かなり厚い膜の作製も可能である。
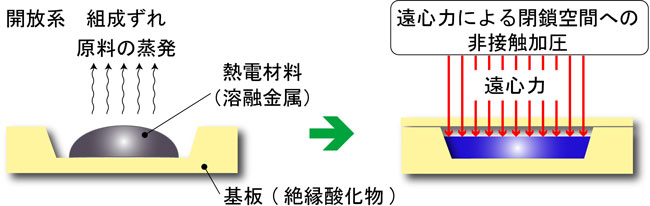 |
図2 遠心力による密閉空間への非接触加圧により高性能熱電厚膜の作製が可能 |
この方法には以下のような特徴を持つ。
-
遠心力を利用するため、非接触で均一加圧が可能である。そのため、基板のパターンにそって均一な膜厚の厚膜が成膜でき、パターンの形状デザインを熱流に合わせて設計することにより、廃熱を効率的に利用することが可能となる。
-
閉鎖空間内部で原料粉末を加熱するため、蒸発による組成ずれがなく、組成の制御が容易である。また、蒸発による損失がないので、投入原料すべてが熱電素子として利用され、後加工も不要であることから歩留まりが向上する。
-
原料粉末量を調整することで厚さ数十μmから数mmまでの厚膜が成膜可能である。
遠心加圧溶融法によってビスマス-テルル系熱電厚膜(厚さ200μm、幅3mm、長さ12mm)を作製したところ、室温での出力因子が4.2×10-3W/mK2であり、無次元性能指数は熱電材料として実用レベルである1を上回っていた。均一加圧など遠心加圧溶融法特有の要因により、基板の厚み方向にc軸が揃った単結晶に近い構造ができたため高い電気伝導率が達成され、このような高性能が実現したと考えられる。
遠心加圧溶融法によって作製した厚膜熱電素子を図3に示す。溝加工を施した基板にビスマス-テルル系p型、n型となるよう原料粉末を交互に充填し、1000Gの遠心力を印加しながら、材料の融点以上に加熱し、冷却することでp型、n型熱電厚膜素子を作製した。得られた厚膜熱電素子(厚さ200μm、幅1.5mm、長さ12mm)は7対のp-n素子対で構成されており、すべての素子が高い出力因子を示した。
以上のように、遠心加圧溶融法により高性能の厚膜熱電素子が簡単な工程で作製でき、熱電発電素子の高出力化、低コスト化、小型化への目処がついた。
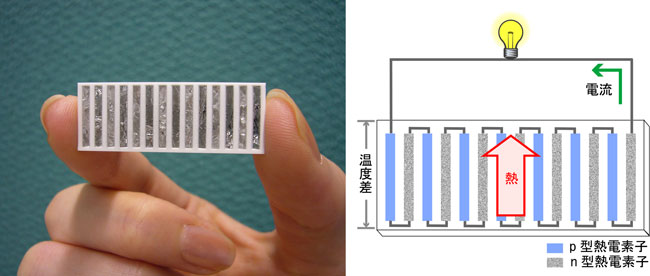 |
図3 基板に成膜した7対のp-n素子対で構成したビスマス-テルル系厚膜熱電素子 |
今回、遠心加圧溶融法という画期的な高性能厚膜熱電素子を作製する技術を開発した。今後は実用可能な熱電発電素子の開発を進め、早急に廃熱エネルギーの有効利用を実現させ、エネルギー・環境問題に貢献していきたい。