独立行政法人 産業技術総合研究所【理事長 吉川 弘之】(以下「産総研」という)環境化学技術研究部門【部門長 島田 広道】分子触媒グループ 宮沢 哲 主任研究員は、大阪有機化学工業株式会社【代表取締役社長 鎮目 泰昌】(以下「大阪有機化学工業」という)と共同で医薬中間体の生産に有用な多段衝突型マイクロリアクターの開発に成功した。
本マイクロリアクターは幅、深さ200マイクロメートル(µm)の溝(マイクロチャンネル)が多数有り、内部で反応溶液を多段衝突させる構造になっているので、2種類の反応溶液をマイクロリアクターに流すだけで十分なミキシングを達成するとともに化学反応を完結させることができる。さらに、従来、超低温(-70℃以下)を必要とする合成反応を-30℃で行うことができるようになった。そのため冷却コストの低減により環境負荷も軽減できる。
具体的には、水素化イソブチルアルミニウムという試薬を用いて種々のエステル類から種々の医薬中間原料であるアルデヒド類を高速、高選択的かつ低環境負荷で生産する事ができた。
この技術は、反応釜(フラスコ)を用いずにフロー系で化学反応を行うので、精密な反応制御が要求される医薬中間体・電子材料合成において、研究開発から生産までのリードタイムを大幅に短縮する新たなツールとして期待される。
本技術の詳細は、2006年1月26、27日に京都で開催される第4回マイクロ化学プラント国際ワークショップ(The Fourth International Workshop on Micro Chemical Plants)で発表される。
マイクロリアクターの構造
|
多段衝突型マイクロリアクター
|
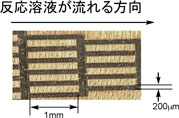
幅、深さ200マイクロメートルの
マイクロチャンネル |
微細加工技術により作成された溝(マイクロチャンネル)内で
2種の反応溶液が多段の衝突を繰り返すことにより反応が選択的に進行する
|
化学反応を行う装置は反応釜(フラスコ)を用いて内容物を攪拌しながら行うバッチ式リアクターが最も一般的であり、様々な分野においてバッチ式リアクターを使用して化学物質の合成が行われている。バッチ式リアクターでは、スケールアップのために必要量に応じて使用する反応釜を選択し反応釜毎に反応条件の最適化研究をしなければならない。その為、研究・開発から実生産まで長いリードタイムが必要であった。
これに対して、超微細加工技術により作成された溝幅数百マイクロメートルの流路(マイクロチャンネル)を利用してフロー系で化学反応を行うマイクロリアクター技術は、従来のバッチ式生産システムに比べて以下の点で優れている。
-
反応装置が小さいため、加熱・除熱等の熱制御が容易である。
-
マイクロチャンネル中の流体制御により、従来のバッチ式リアクターと同等以上のミキシング効果が得られる。
-
マイクロチャンネル中の流速を制御することにより生産量を任意に調整することができる。
マイクロリアクター技術は、精密な化学反応の制御が要求される医薬中間体産業、短いライフサイクルの中で常に高性能な材料の供給が求められている電子材料産業においてリードタイムを短縮する新技術として期待されている。
さらに世界中で環境意識が高まる中、化学産業においては廃棄物の少ない生産プロセスが求められている。しかし、医薬中間体や電子材料産業においては大量生産・消費を基にした従来の生産プロセスでは、精密な反応制御、迅速な研究・開発・生産と環境負荷低減を両立することは難しい。
産総研では、持続発展社会を実現するために有害物質排出の最小化、エネルギー効率の向上、循環型資源への原材料転換などを目指して産業技術の研究開発を行っている。
この目標の下、産総研は大阪有機化学工業と共同で医薬中間体合成に最適な新しいマイクロリアクターの開発並びにこれを用いた医薬中間体として有用なアルデヒド類の合成に取り組んできた。
アルデヒド類は合成化学上、種々の化学物質へ誘導する上で極めて有用な中間物質群であり、医農薬、電子材料等に使用される中間原料のひとつである。アルデヒド類の合成法としては、対応するエステル類を水素化イソブチルアルミニウム(以下DIBAL-H)という試薬によって還元反応するのが原料コスト、原子利用効率(低廃棄物量)の観点から好ましい方法として知られている。しかしながら、DIBAL-Hによる還元反応は、温度が高いと一旦生成したアルデヒドがさらにDIBAL-Hと反応してアルコールになってしまうため、超低温(-70℃以下)の条件下において行わなければならず、工業的にはごく一部において実施されているにすぎない。大きな反応釜(バッチ式リアクター)を用いて超低温の反応を行うには、冷却コストが掛かりすぎるためである。そのため、DIBAL-Hに代わる反応試薬の開発が進められ、室温付近でエステル類の還元反応を行う手法も開発されたが、原子利用効率、廃水処理等において問題があった。
今回開発に成功したマイクロリアクターはアルミニウムの基盤に幅、深さ200マイクロメートルの溝(マイクロチャンネル)を多段で配置した構造を有する。マイクロリアクターの2カ所の注入口に導入された流体(DIBAL-Hとエステル)は内部で多段の衝突を繰り返すことにより高い選択性で反応が進行し、目的とするアルデヒドが出口から流出してくる。さらに、本マイクロリアクターは、従来、超低温(-70℃以下)で実施されていたエステル類のDIBAL-H還元反応が-30℃の条件下においても高い選択性と再現性を持って実施することができた。冷却コストの低減に伴う省エネルギー、環境負荷低減に資する次世代型化学プロセスと言える。
なお、本研究成果の一部は、独立行政法人新エネルギー・産業技術総合開発機構プロジェクト「マイクロ分析・生産システムプロジェクト」の再委託研究「配位重合用フロー系マイクロミキサーの開発」(H14-H16)で得られたものである。
マイクロリアクター技術による医薬中間体合成例
|
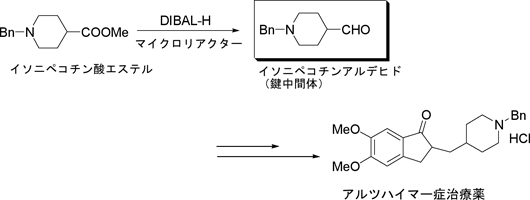 |
今回開発したマイクロリアクターによるアルデヒド合成は、さらに検討を重ね実用化に結びつける予定である。また、アルデヒド合成反応以外にも、極低温条件を必要とするプロセスが多くあるので、それらの反応にもマイクロリアクターの適用をはかる。